Technology company focuses on creating more resource-efficient factories
A technology company focused on creating more resource-efficient factories and resilient supply chains was starting a new distribution facility and decided to implement UpKeep’s mobile-first solution from the very beginning.
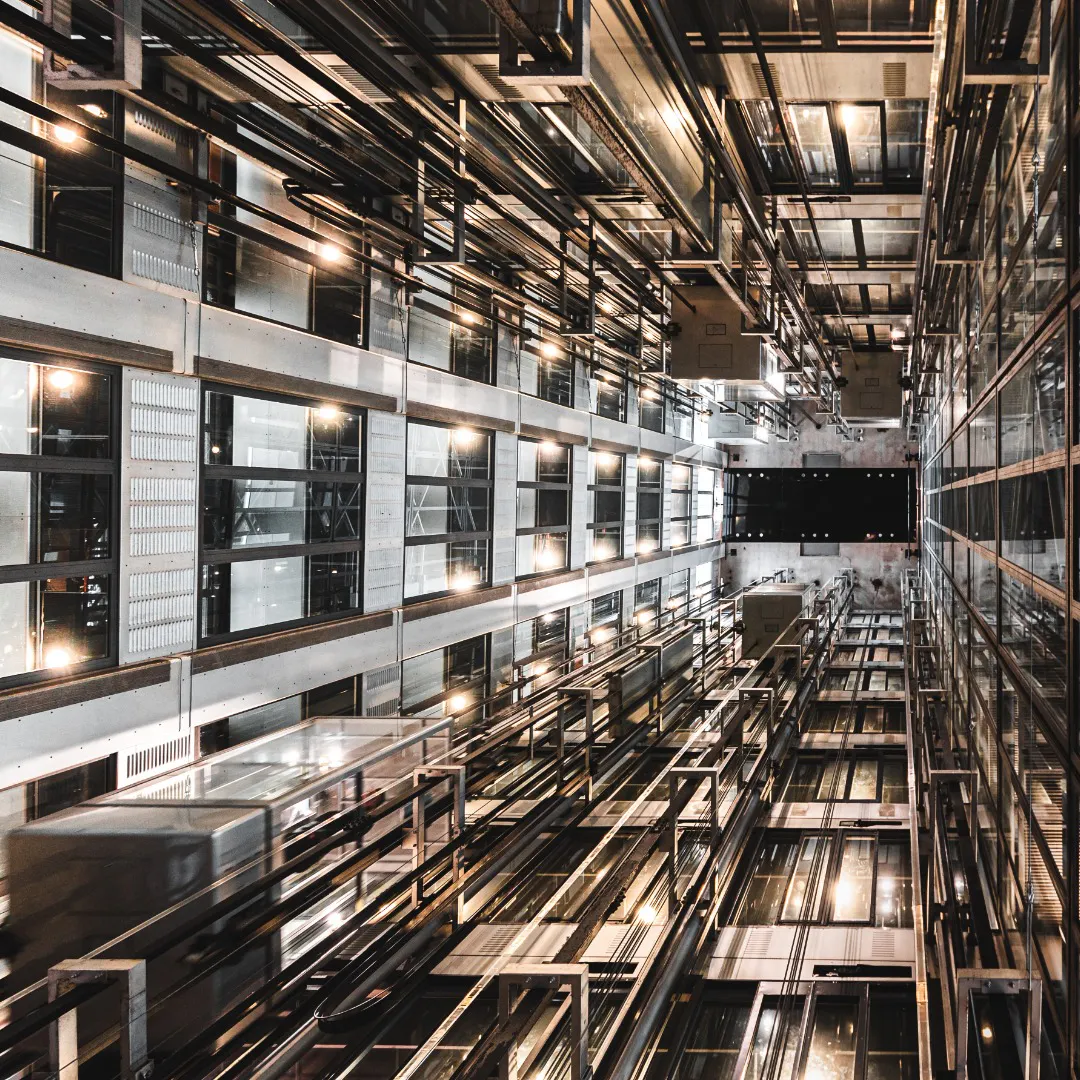
The company needed a solution to manage maintenance for its distribution system in a new 1.4 million square foot warehouse. It wanted to integrate all its spare parts into a system as soon as they arrived as well as manage work orders efficiently on a mobile-based platform. Since this facility was essentially a start-up, the main challenge did not revolve around existing problems but instead focused on simply getting thousands of parts and assets loaded into the system during implementation.
Solution
Based on the previous experience of the maintenance manager, the company chose UpKeep as its computerized maintenance management software (CMMS) system. Although the company is only a few months into implementation, UpKeep has successfully helped it establish a solid foundation for its new facility. Many exciting plans for the future are already in the works.
The start-up wanted a balance between cost vs. product features and leveling between the two, and the management felt that UpKeep was a good fit in all categories.
Selection Based on Experience
The maintenance manager wanted to find a solution with a better graphic interface for users and an application that was available on mobile phones. Work orders had to be entered conveniently and paper-based filing systems had to be eliminated.
UpKeep allows the company to assign specific people to tasks on-site. They can see what needs to be done, and they can transfer the work to someone else. Paperwork is no longer lost; all information is in UpKeep.
Implementation in Progress
The facility selected UpKeep from the very beginning and began testing and installation before the facility began operations.
The distribution center has been importing data into UpKeep, which has included roughly data for 1,000 assets and 2,000 parts.
The 1.4 million square foot warehouse is essentially a very large machine. The company broke it down into groups, tagging locations and then assets within that location. When an issue or a downtime error occurs, the team can just scan the QR code, locate the problem, and initiate the work order. The data is filled in automatically.
Identifying Recurring Deficiencies During Start-Up
Since the facility was in the commissioning phase and focused on bringing systems online, it really wanted to identify recurring deficiencies. Each week, the facility can look at the top three offenders and just keep whittling down these issues one at a time.
The organization appreciates the fact that reports and analytics can be tailored to show exactly the data the team is most interested in seeing, not the measures that are currently irrelevant to them.
The division is tailoring the features within the analytics to specifically find what it wants, identifying major offenders and providing substantial evidence to support investigation and resolution.
More Efficient Use of Labor, More Data
The maintenance team is made up of eight individuals. UpKeep has not only eliminated the need to run back and forth from the worksite to the office to record data but also resulted in capturing more information on the whole.
Instead of jotting down notes on paper and feeding them back to a commissioning team for resolution, technicians can just pull out their phones, scan where they are, and take three minutes to make a work order. That reduces the amount of missed opportunities to document because it is so convenient. The center is capturing a lot more data than anticipated.
Future Plans
As the facility moves forward, it is beginning to consider which key performance indicators (KPIs) will be most valuable to track.
The facility is capturing downtime, maintaining inventory of spare parts, and performing trend analysis. In the future, it will focus on preventative and predictive maintenance in order to stretch out part life as much as possible. UpKeep will help them identify and track issues so they know the best time to swap out a part.
Since the operation is somewhat complex, UpKeep gives the organization a means to pinpoint those areas that make the most sense to watch.
A distribution center doesn’t have typical downtime, but if a driver is sitting at a door waiting for his load, that’s lost time. UpKeep allows the center to break things down further and keep track of which specific area was down. UpKeep allows better management and monitoring of a complex system.
In addition, the center plans to establish all preventive maintenance tasks in UpKeep with step-by-step directions. The long-term goal is to continue to improve access, use, trend analysis and accountability for spare parts.
Want to keep reading?
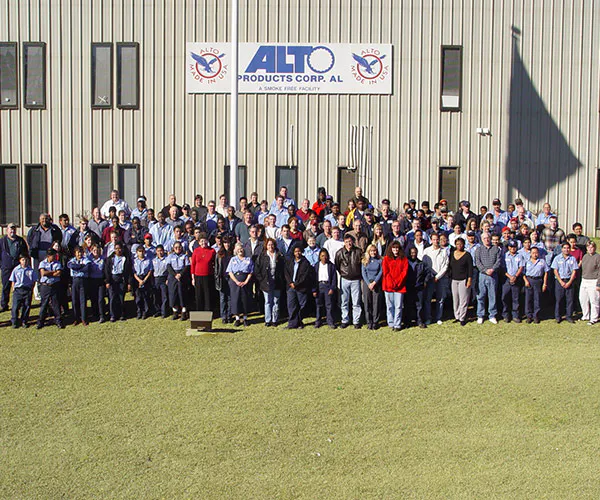
Equipment / Manufacturing
Alto Products moves from reactive to preventive maintenance
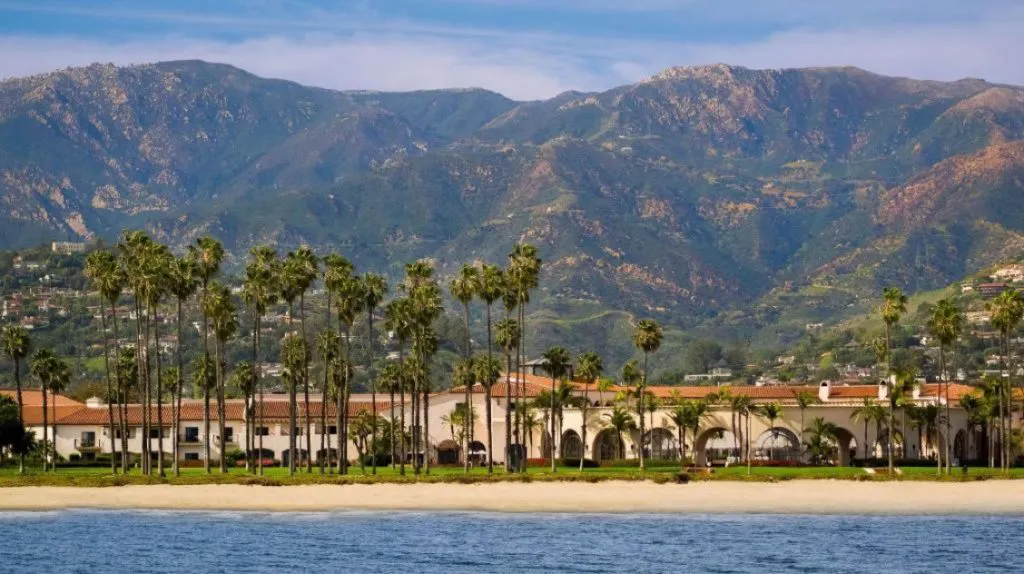
Equipment / Manufacturing
Innovative Micro Technology creates a safety-focused culture
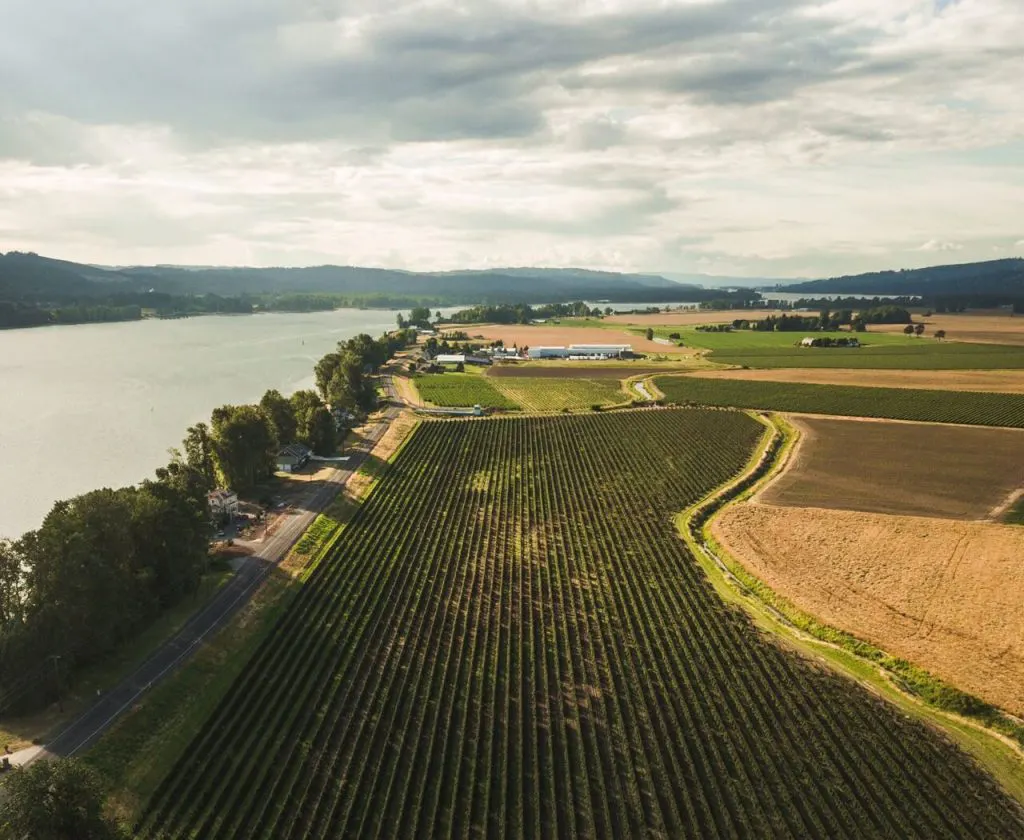
Equipment / Manufacturing
Columbia Fruit saves money with organized inventory
4,000+ COMPANIES RELY ON ASSET OPERATIONS MANAGEMENT
Leading the Way to a Better Future for Maintenance and Reliability
Your asset and equipment data doesn't belong in a silo. UpKeep makes it simple to see where everything stands, all in one place. That means less guesswork and more time to focus on what matters.
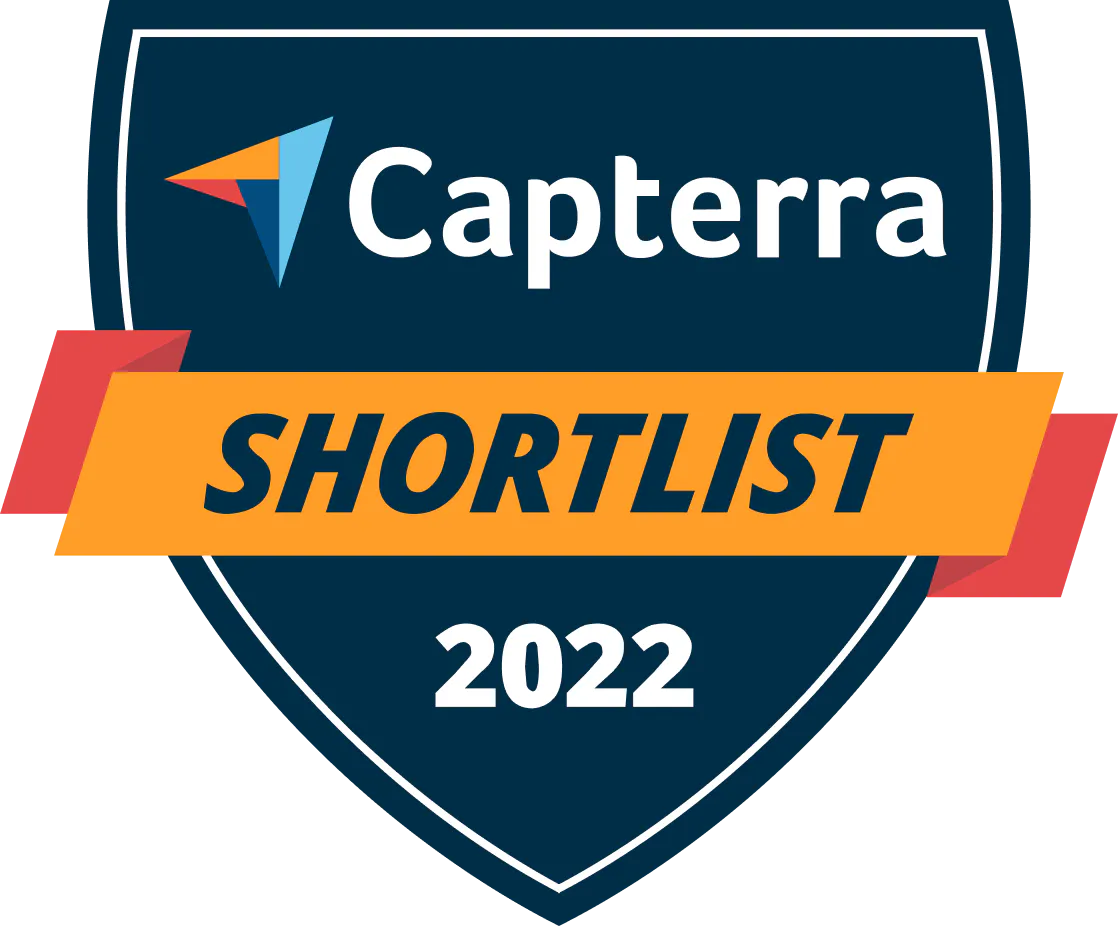

![[Review Badge] GetApp CMMS 2022 (Dark)](https://www.datocms-assets.com/38028/1673900459-get-app-logo-dark.png?auto=compress&fm=webp&w=347)
![[Review Badge] Gartner Peer Insights (Dark)](https://www.datocms-assets.com/38028/1673900494-gartner-logo-dark.png?auto=compress&fm=webp&w=336)
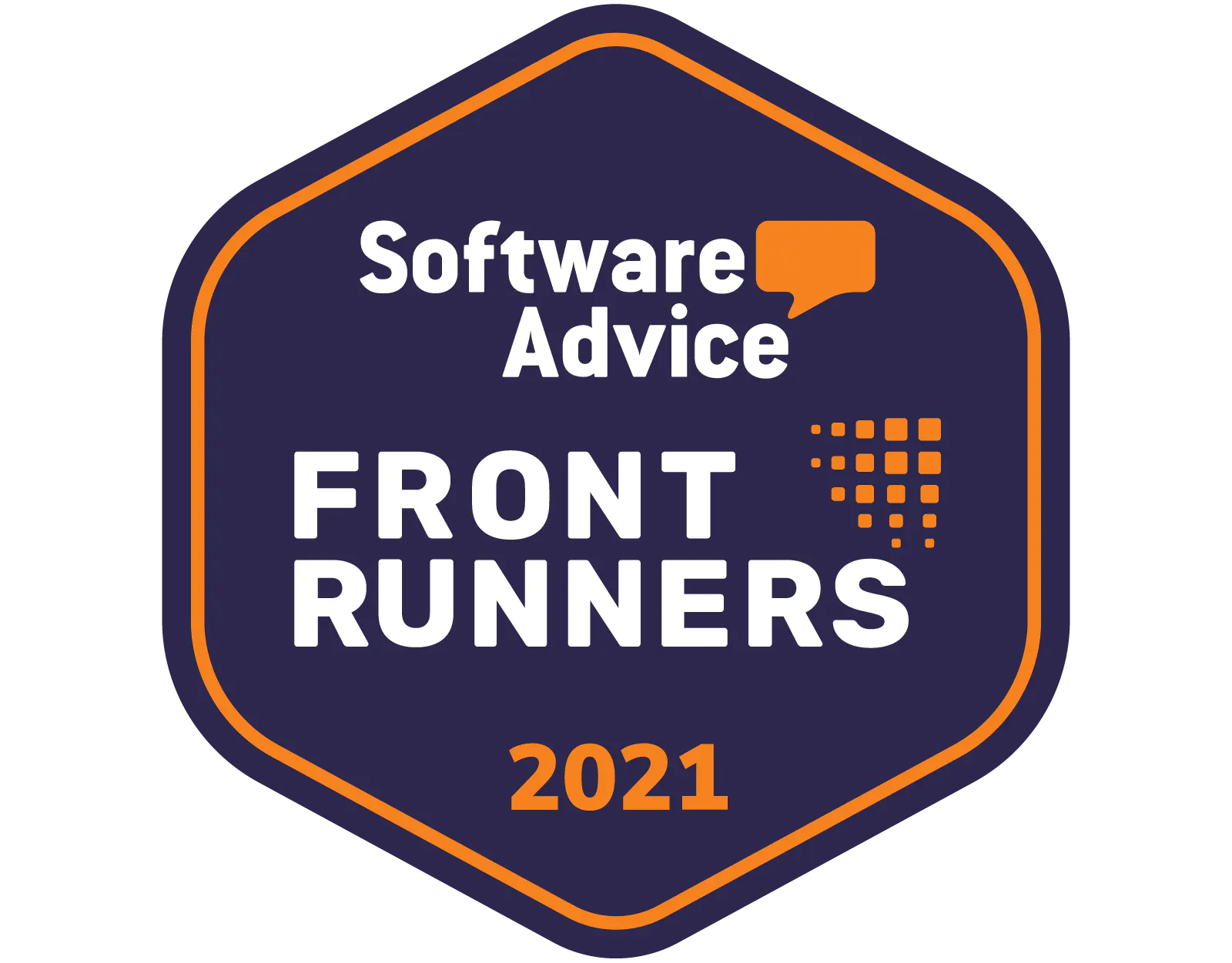