Success Story
Peerless Pump replaces old CMMS with UpKeep
Prior to implementing UpKeep, Peerless Pump’s maintenance team was attempting to use an existing CMMS with poor results. The lack of a mobile solution necessitated printing paper work orders that required hours daily to manage. Upon implementing UpKeep, the maintenance team has streamlined their process, built out their knowledge base for better troubleshooting, and can now send reporting easily and with confidence that the numbers are accurate.
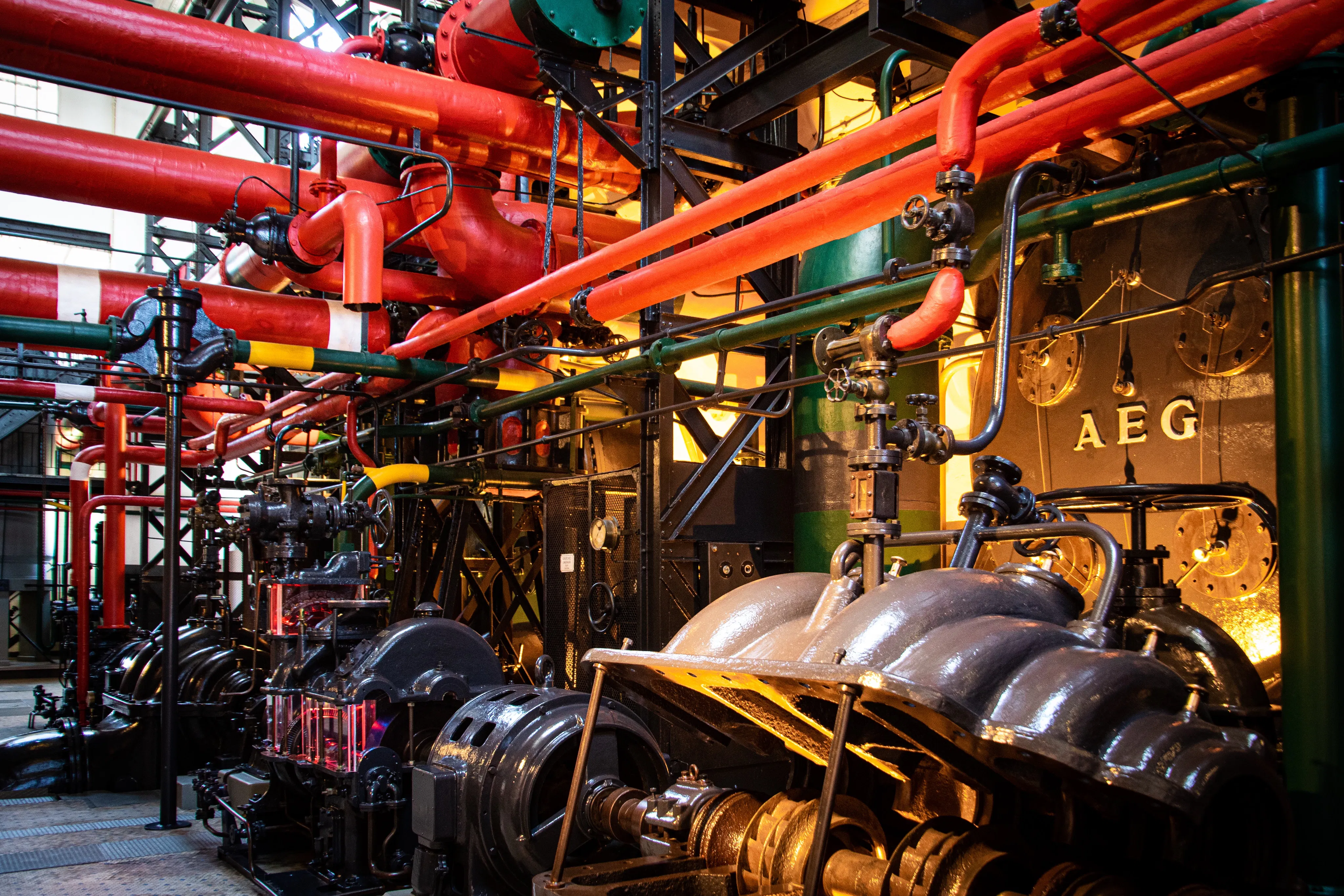
Peerless Pump is an established manufacturer of horizontal and vertical pumps with installations in Commercial Buildings, Municipal Facilities, and Industrial Warehouses. As their Maintenance Manager, Kevin is responsible for the repair, upkeep, and asset lifecycle management of their 300,000-square-foot facility in Indianapolis, Indiana.
Challenges
While a CMMS system was in place, it could have been more efficient and easier to use. For example, every morning started with Kevin printing off paper work orders from 5:15 - 6 AM and then physically distributing them in a team meeting. There was no mobile app, so any communication required the technicians to leave the floor and return to the office, or Kevin needed to leave the office and attempt to find someone in the 300,000-square-foot facility. The maintenance team also fulfilled work orders for internal requests from other groups, and those usually came in the form of hallway conversations. To capture those, someone would need to write them down and then return to the office to enter them on the computer. As a result, Kevin spent 8-10 hours daily processing jobs, leaving little time for anything else.
The user experience of the existing CMMS also provided challenges. To find any history required 12-15 screens to click through and another 6-8 screens to put in any additional notes. The net result was that technicians avoided doing either, leaving significant knowledge gaps.
Monthly reporting was also laborious and prone to error. Kevin regularly provided percentage of completion reporting for reactive and preventive maintenance orders to management, which could take up to two days to complete. First, Kevin would export the data from the old CMMS into Excel, but inevitably he would discover information that he knew needed to be corrected. Then he would manually fix the bad data and repeat the process. The team also had a monthly meeting where they would review 3-400 work orders to verify that the status of each was accurate.
Solution
Kevin knew there had to be a better way and started searching for a new CMMS. In particular, he was looking for a mobile-first solution and began researching by watching videos on YouTube. Kevin found the user interface of UpKeep to be the most user-friendly and accomplished precisely what his team needed. Other solutions went deeper into use cases like purchase orders, which he didn’t think fit maintenance as well. UpKeep felt like it was built by people with a background in maintenance.
To implement, Kevin began by setting up their assets, which allowed the team to automate reactive work orders. Once that was set up, they implemented preventive maintenance. Getting work out to people is much smoother now because he doesn’t have to walk out of the office to find people to hand them a piece of paper. New work orders automatically appear in the queue on everyone's mobile device. Their morning team meeting begins with everyone pulling out their phone, quickly reviewing, and heading out to start the day.
Results
After implementing UpKeep, the daily management of work orders has decreased dramatically, from 8-10 hours to less than 2. Kevin has replaced his high-volume printer with a much smaller desktop version and only prints as needed. Work order requests are created internally from other team members' mobile devices, which Kevin can quickly review. The need to run back and forth to the office in a 300,000-square-foot facility has been eliminated.
Now that entering notes is easy and convenient on everyone’s mobile device, the technicians not only enter notes but can also attach photos for reference, creating a robust knowledge base. As a result, the team can reference similar problems and troubleshoot more quickly. Monthly reporting is also now a breeze. Kevin simply takes a screenshot of the UpKeep dashboard, and his monthly reporting is done.
Since Kevin has decreased the time spent manually managing work orders, he’s also been able to improve Peerless Pump’s bottom line in other ways. For example, after implementing Upkeep, Kevin was able to take on managing their camera system, which an independent contractor previously managed. That contractor charged a minimum of $700 per visit, which has now been eliminated. Kevin has also been able to take on the responsibility of managing badge access for their facility, freeing up bandwidth for other teams.
Overall Kevin and his team are saving hours each day with the automation UpKeep has provided, and work is processed and completed more quickly, resulting in an improved experience for Kevin, the technicians, and management.
Want to keep reading?
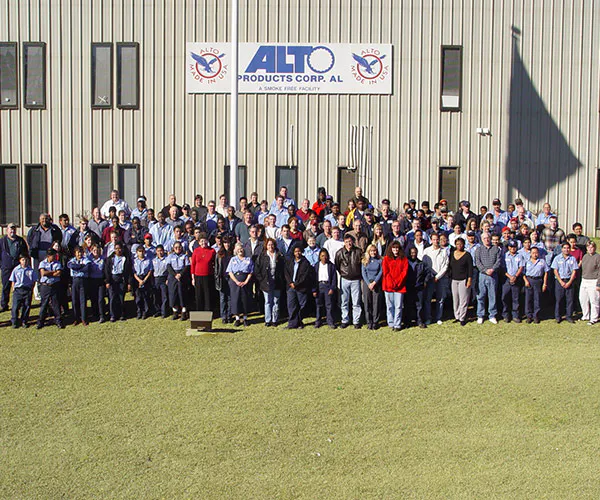
Equipment / Manufacturing
Alto Products moves from reactive to preventive maintenance
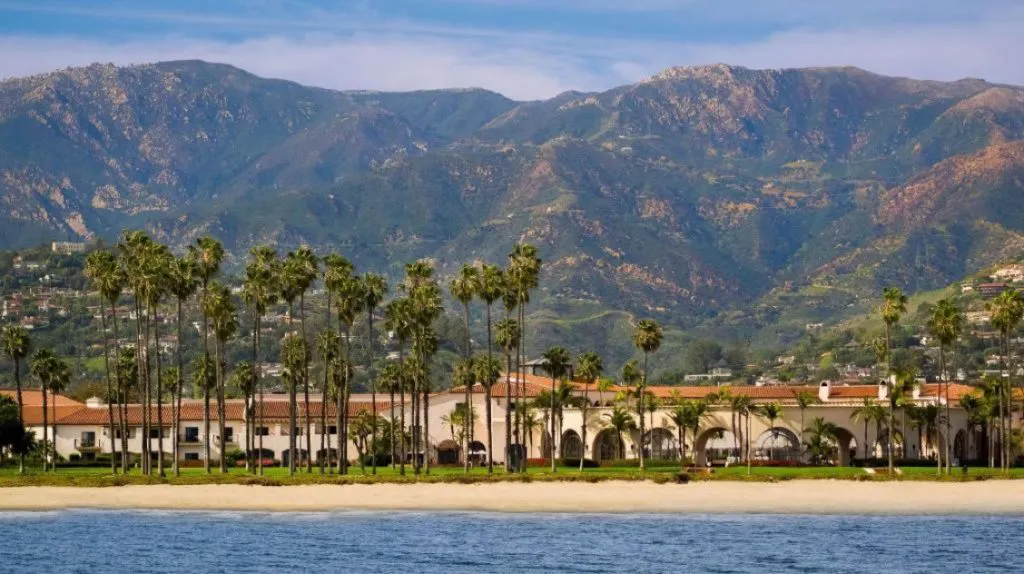
Equipment / Manufacturing
Innovative Micro Technology creates a safety-focused culture
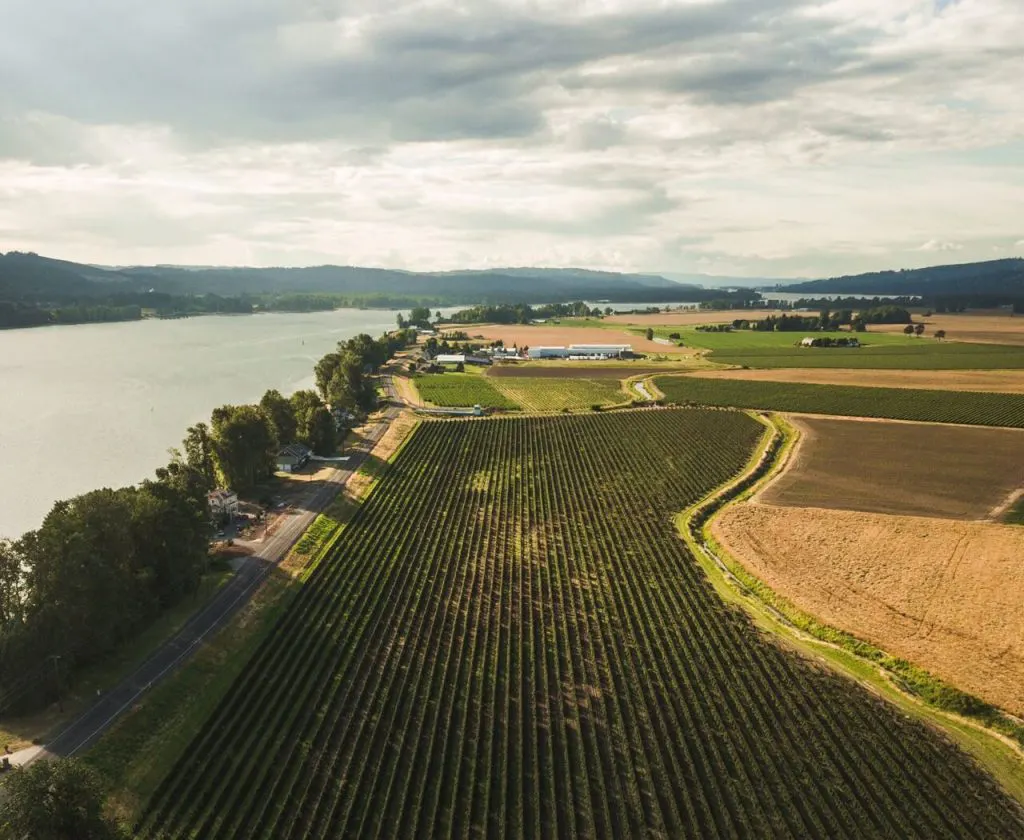
Equipment / Manufacturing
Columbia Fruit saves money with organized inventory
4,000+ COMPANIES RELY ON ASSET OPERATIONS MANAGEMENT
Leading the Way to a Better Future for Maintenance and Reliability
Your asset and equipment data doesn't belong in a silo. UpKeep makes it simple to see where everything stands, all in one place. That means less guesswork and more time to focus on what matters.
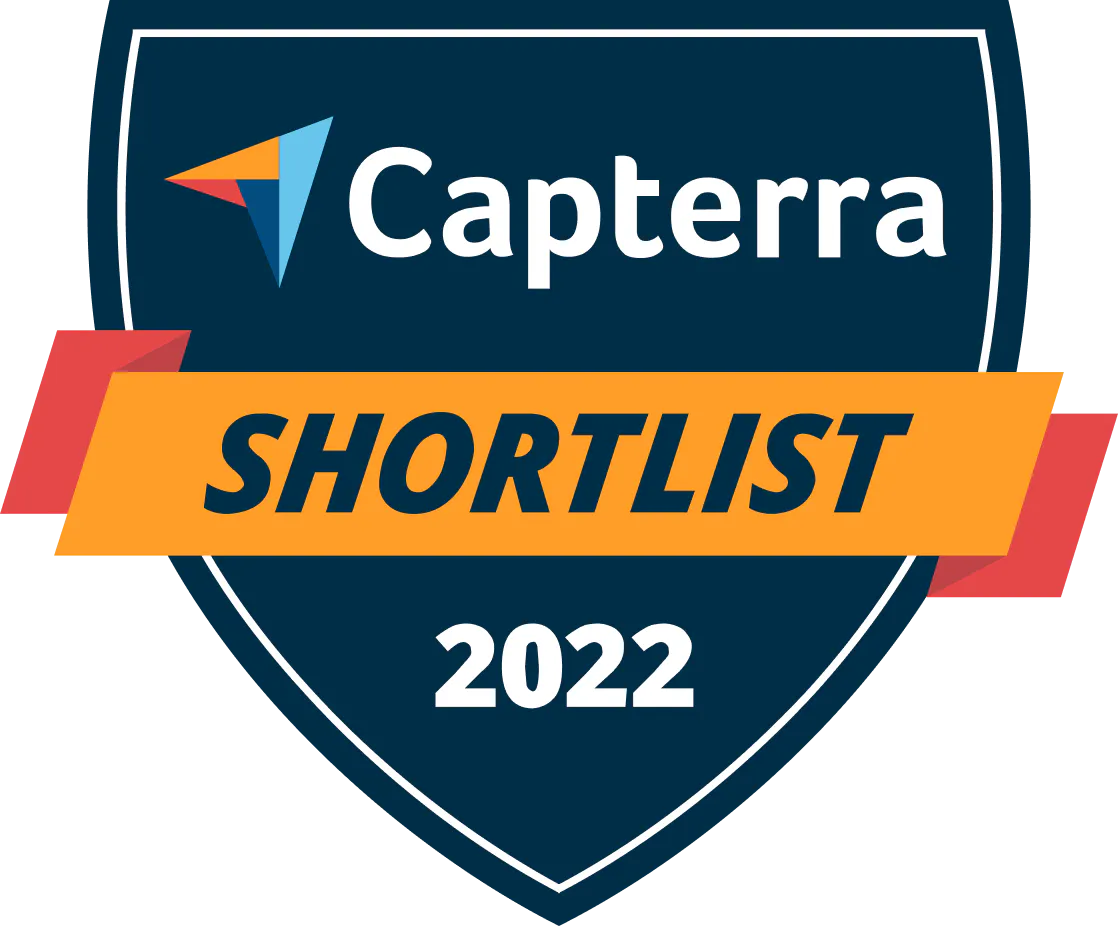

![[Review Badge] GetApp CMMS 2022 (Dark)](https://www.datocms-assets.com/38028/1673900459-get-app-logo-dark.png?auto=compress&fm=webp&w=347)
![[Review Badge] Gartner Peer Insights (Dark)](https://www.datocms-assets.com/38028/1673900494-gartner-logo-dark.png?auto=compress&fm=webp&w=336)
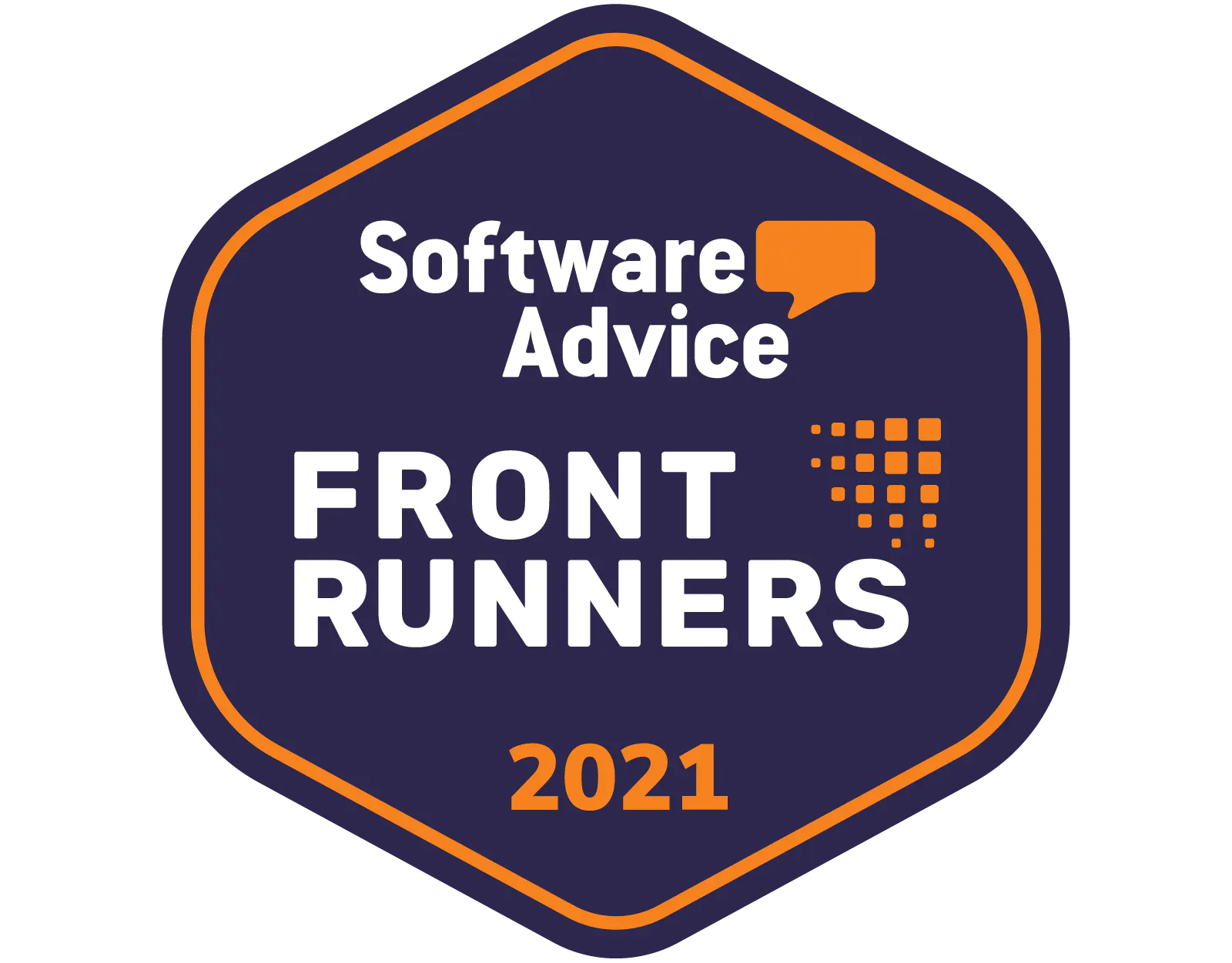