Mining Company increases plant availability by 5%
When one North American plant of a worldwide mining consumables and media manufacturing company needed to automate its maintenance processes, it selected UpKeep’s asset operations management system.
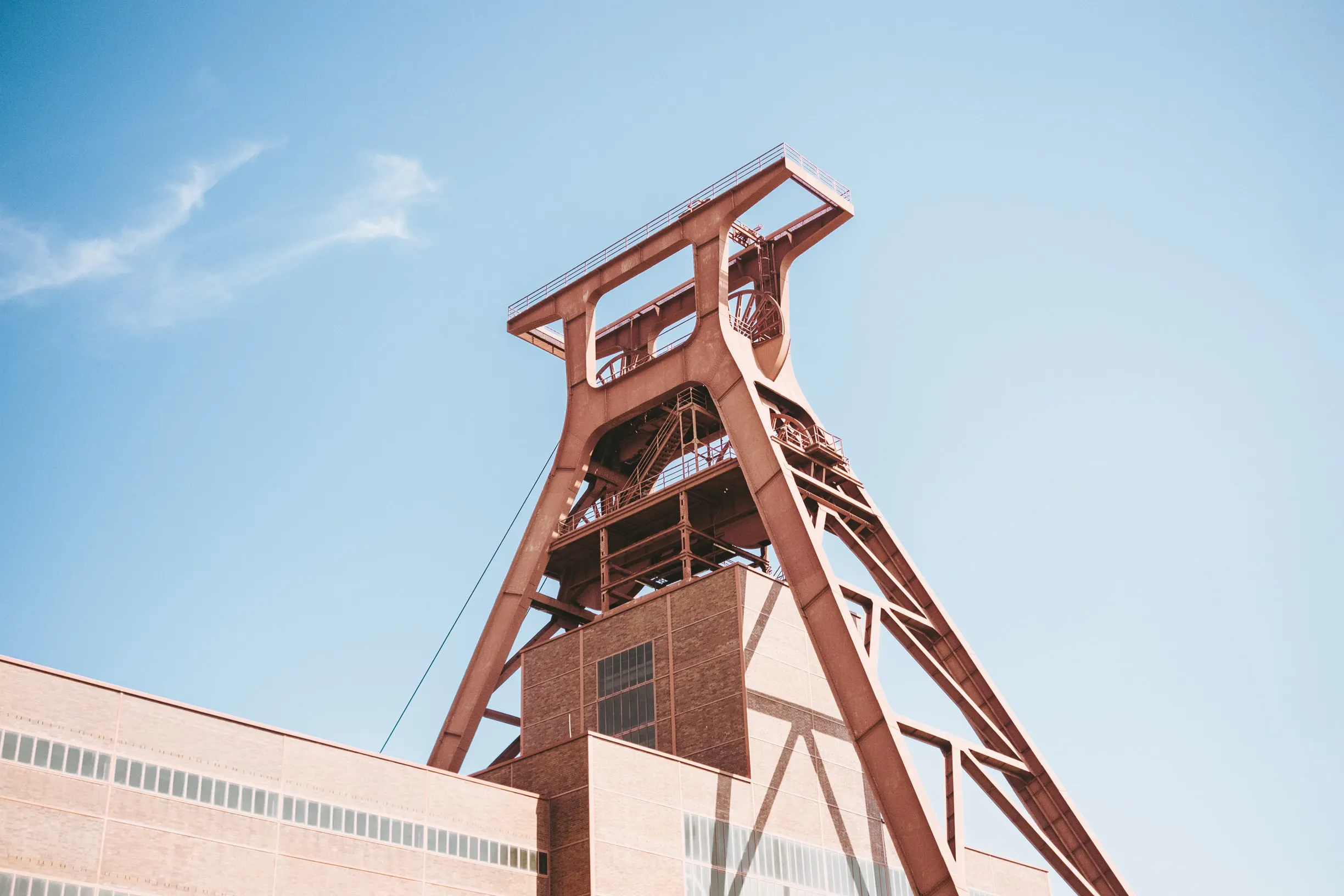
Challenge
The company was managing its work order and maintenance processes using Excel spreadsheets, which was labor-intensive and difficult. It was easy to miss dates when sheets of paper were involved. Resources were dedicated to handling reactive maintenance requests, and short-term solutions often failed to resolve equipment issues.
Solution
By using UpKeep, this manufacturer has been able to streamline its work orders, move from a reactive mindset to both a preventive and predictive one, and identify high-priority equipment repair or replacement issues. The management team can see “repeat offenders” in the system, allowing them to prioritize solutions and problem-solve for those specific issues.
Results
One of the most important key performance indicators (KPIs) for the company is online availability or the amount of time that the plant is available to run. Since implementing UpKeep, the facility has boosted this availability by 5 percent, which translates to a savings of $40,000 to $50,000.
Obvious Choice and Smooth Onboarding
Prior to UpKeep, the company stored all its information on Excel spreadsheets. printing daily and weekly worklists. Technicians went through them on a daily basis, initialed tasks as they completed them, and traded for new sheets. The amount of paper quickly became overwhelming.
When the maintenance manager went in search of a new solution, he narrowed the choices down to three or four. UpKeep matched what the company was looking to do within that particular plant. Being able to use the mobile app and the fact that UpKeep could link work orders to a technician’s iPad were advantages. That meant a technician could go out to the field and enter all the information, even if he didn't have a connection to the internet. When he came back, the system would automatically uplink that information.
Once the selection was made, the onboarding and training process began. The company was pleased with the support it received from UpKeep. For instance, it had a vast program to manage spare parts that could be restructured and imported into UpKeep. Since buy-in from technicians was a bit slow, it was helpful for the organization to emulate what it had in its spare parts management system so it was familiar.
While skepticism frequently comes with change, the fact that UpKeep was easy to use made a big difference. The team felt like it was really easy to understand. In fact, the best craftsman was technology-challenged and initially scared to switch to UpKeep, but today, he's one of the most avid users of the new system.
Mobile App Increases Efficiency
Maintenance technicians and managers are frequently on the move, and UpKeep’s mobile app is easy to take along throughout the day. Being able to use an iPad or phone to just take a picture and fill out a work order on site was a big plus. Even if all information is not immediately available, the technicians were able to placemark a work order and add anything else later.
Trigger Reminders Keep Team on Its Toes
Instead of trying to remember when preventive maintenance is due or that a work order must be completed today, UpKeep flags these events with a red date to help the team remember.
The team’s goal was to keep the plant up and running at top-notch all the time, requiring a great deal of proactive efforts. The triggers have been extremely helpful. The manager generates a nightly checklist and sets realistic goals using what he calls TIME–giving technicians the tools, the information, the material, and an example of what he wants to see them accomplish.
The Shift Toward Predictive Maintenance
Before UpKeep, the company was handling mostly reactive maintenance requests, leaving little time to manage data entry. However, as the organization continued to use the system, it could see reactiveness started to decrease. The team was getting less behind.
Now the plant is continuing to move forward with preventive maintenance. For example, instead of waiting for a conveyor to start faulting by jamming, the technicians respond to a preventive maintenance work order in UpKeep, which has them measure how much the chain has stretched and how much play is in the rollers. At a certain point before failure, the chain is replaced.
Reports Help Share Successes
While the changes in efficiency became quickly apparent to the maintenance team, they wanted to make sure that the rest of the employees in the facility understood the scope of their work. Now, all open work orders are displayed on a local monitor so everybody can see them. UpKeep helps keep the technicians accountable to make sure that nothing's behind, but more importantly, it shows everyone how many work orders are actually completed. Usually, about 50 work orders are open simultaneously with an additional dozen or so added every week.
Other reports such as aging, which technicians are signing in, and work order completions are also helpful. The aging report is most important to me because it allows the management to monitor response time, which drives everyone to perform even better.
Capturing the Data to Make Better Decisions
The company is beginning to utilize more of UpKeep’s analytic capabilities. UpKeep captures information every day, so the organization can easily go back and search for a particular piece of equipment and see everything that has been done within a certain period of time. For example, if the team just changed out a part 12 weeks ago and it’s failing again, they will dig deeper and find out why.
Before UpKeep, it was easy for a technician to perform a short-term fix to a problem but fail to communicate the issue for a long-term fix because there was no easy way to record the information. For example, someone on third shift might perform a short-term fix on a hydraulic pump, forget about it, and three days later, the pump fails completely. Since it takes six to eight hours to change out a hydraulic pump, addressing that problem when it first occurs before the pump fails keeps the facility running.
The efficiencies gained also allow the team to move toward both a preventive and predictive maintenance mindset. If some component is only going to last nine months, the team can upgrade around seven and a half months before a failure occurs.
Improvements Abound Throughout Facility
The company has seen improvements in all areas, from water savings to improvement in the hydraulic system, the electrical system, and in lift conveyors. Just getting the information out there in front of the team on a regular basis is critical. Technicians are now getting out there and getting the work done.
Prior to UpKeep, the team was in survival mode, just trying to keep everything up and running. Now, the company has gained significant efficiencies that are seen in every aspect of its facility.
It’s reflected in its online availability, which is measured weekly. The availability of the plant has increased close to 5 percent, which amounts to a dollar savings of $40,000 to $50,000.
The savings is also coming across in labor because the maintenance team now has a chance to focus on other things. It no longer needs to hire electrical or mechanical contractors, which is not only a significant savings but also gives the technicians new opportunities which they enjoy.
Finally, the facility is garnering some corporate recognition as well. During a monthly management meeting, a corporate executive reviews all the plants across the globe for operational excellence. This facility using UpKeep is always recognized as the number one facility.
Want to keep reading?
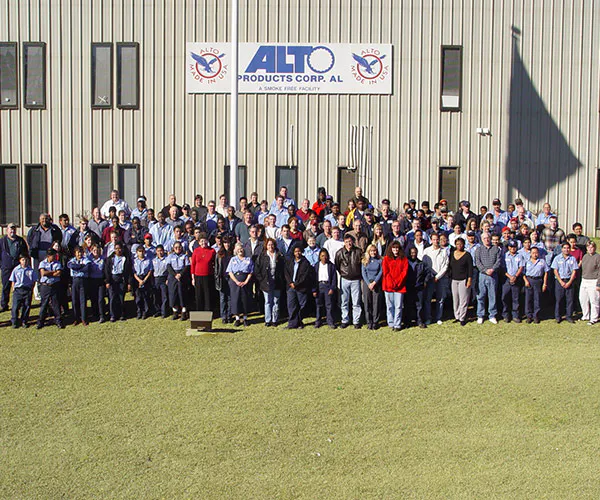
Equipment / Manufacturing
Alto Products moves from reactive to preventive maintenance
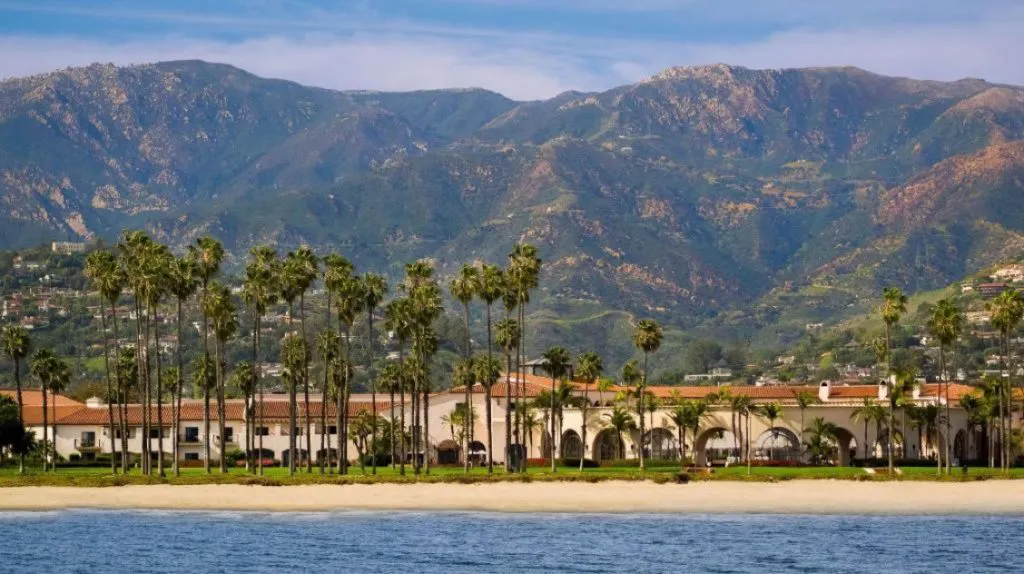
Equipment / Manufacturing
Innovative Micro Technology creates a safety-focused culture
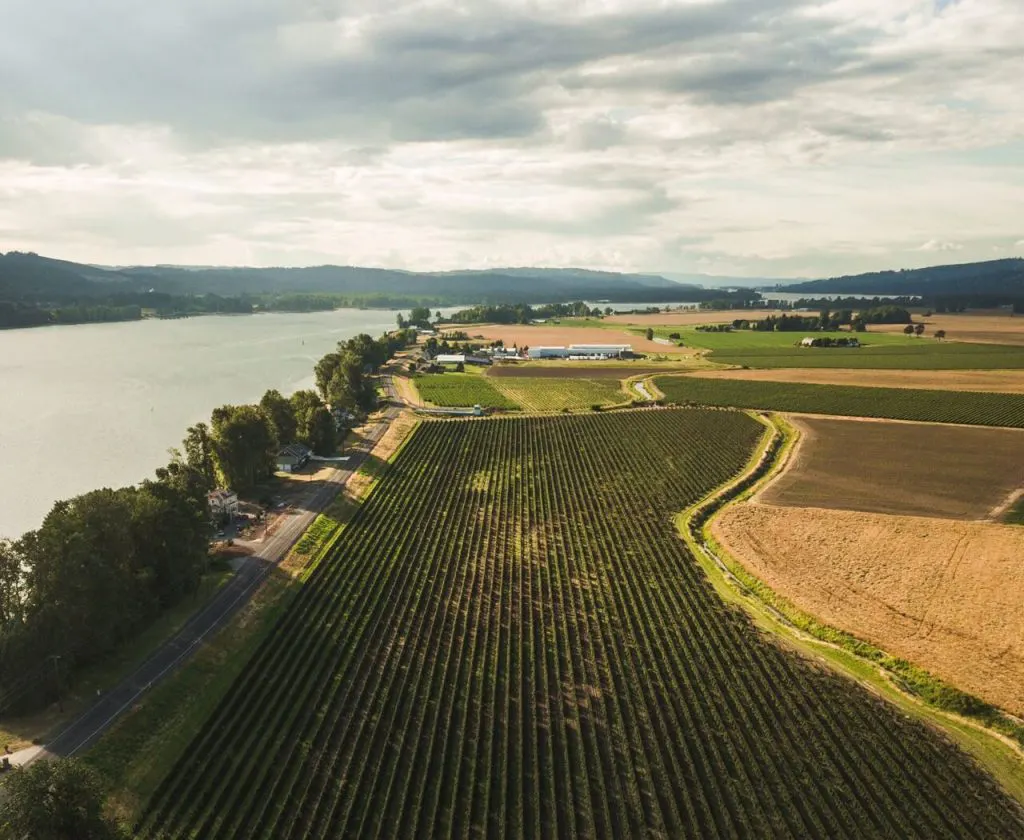
Equipment / Manufacturing
Columbia Fruit saves money with organized inventory
4,000+ COMPANIES RELY ON ASSET OPERATIONS MANAGEMENT
Leading the Way to a Better Future for Maintenance and Reliability
Your asset and equipment data doesn't belong in a silo. UpKeep makes it simple to see where everything stands, all in one place. That means less guesswork and more time to focus on what matters.
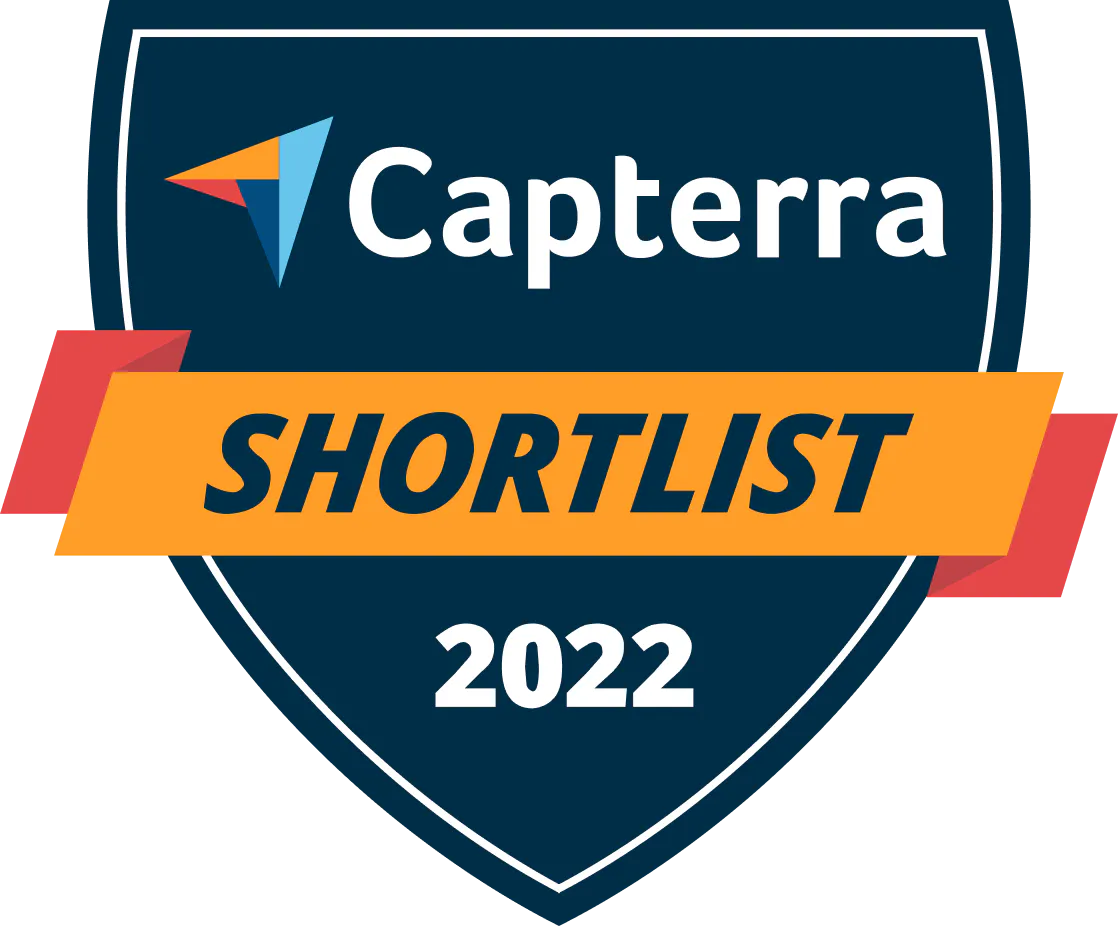

![[Review Badge] GetApp CMMS 2022 (Dark)](https://www.datocms-assets.com/38028/1673900459-get-app-logo-dark.png?auto=compress&fm=webp&w=347)
![[Review Badge] Gartner Peer Insights (Dark)](https://www.datocms-assets.com/38028/1673900494-gartner-logo-dark.png?auto=compress&fm=webp&w=336)
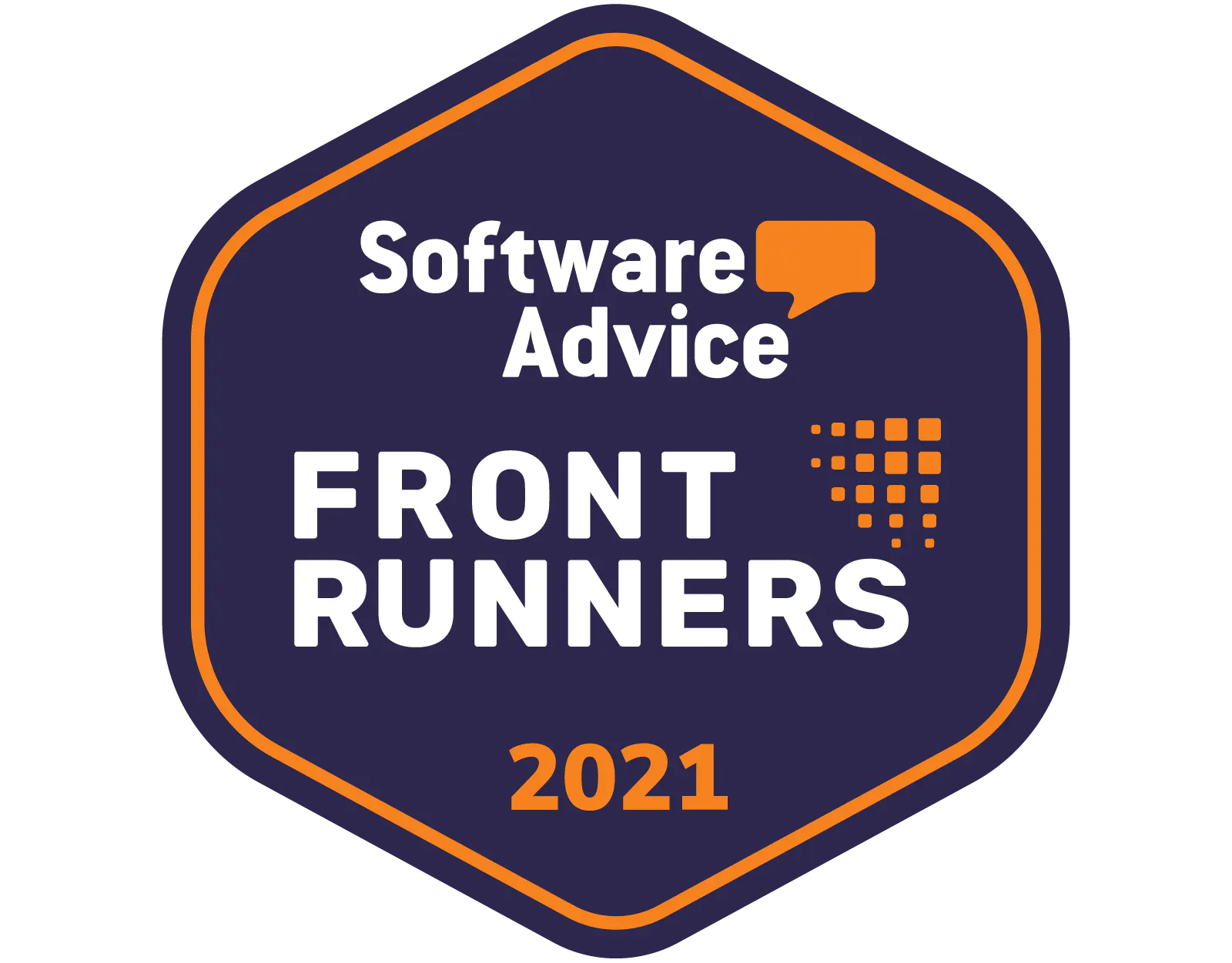