Concrete Company saves money by eliminating double buying
A concrete business was having difficulty assigning work orders efficiently. It also frequently purchased duplicate emergency parts, costing the company tens of thousands of dollars each year. Management knew something needed to be done.
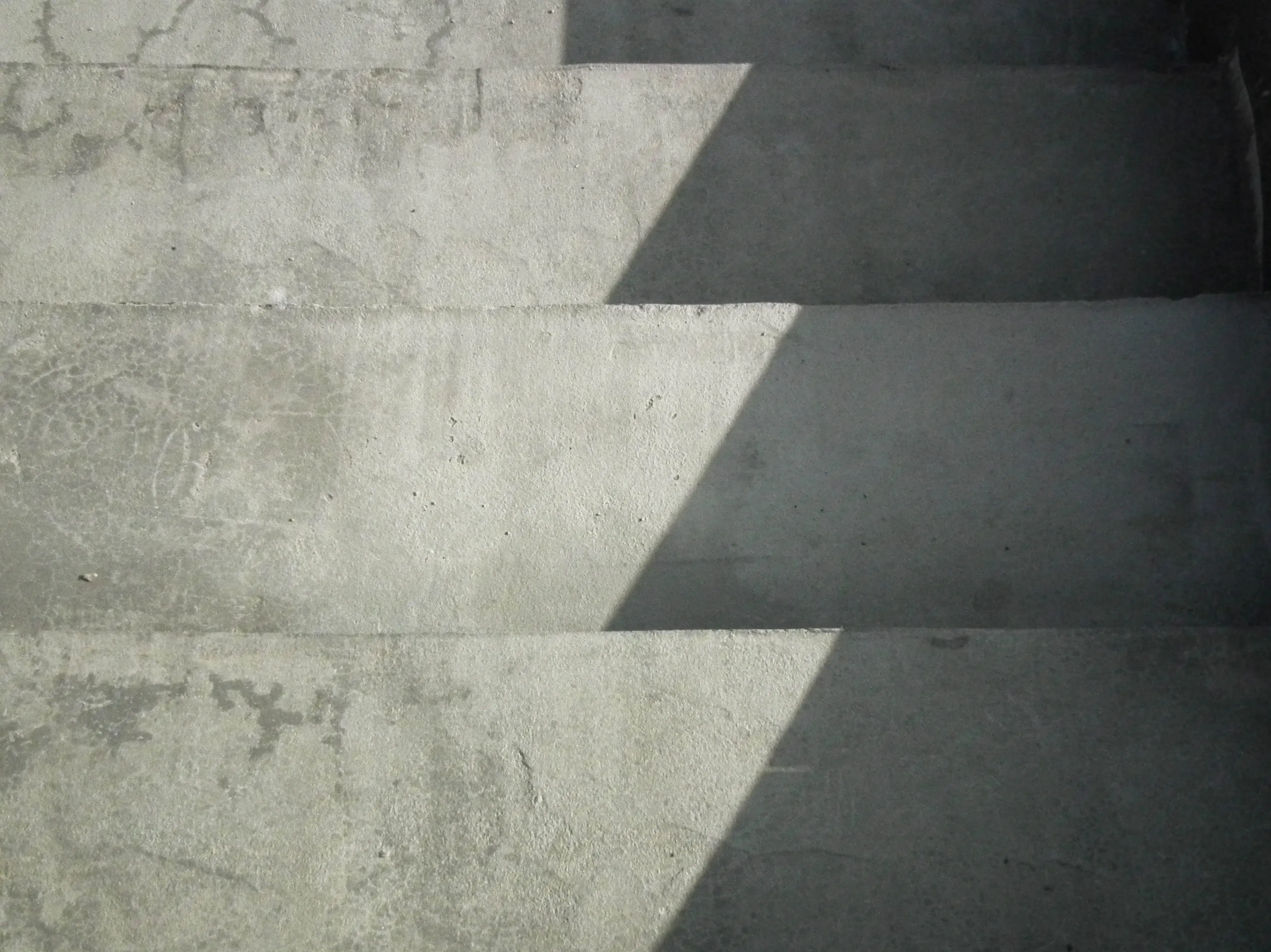
Challenge
A maintenance team of three was responsible for keeping multiple plants up and running. The operations manager spent much of his day simply trying to assign work orders to the right technicians. The company needed a solution to help prioritize maintenance orders and keep track of inventory.
When concrete equipment needed repair, technicians often couldn’t find necessary parts. As a result, the technicians would simply repurchase parts in order to get the equipment back up and running as quickly as possible. Inventory costs were exceedingly high.
Solution
The company implemented UpKeep’s mobile-first solution to start handling its work orders and inventory management. Today, the maintenance crew easily starts their day with a prioritized work list, has reduced its inventory costs by tens of thousands of dollars, and has increased productivity by at least 10 percent.
Ease-of-Use Means Enthusiastic Implementation
The company understood that it needed its maintenance team’s buy-in to be successful in UpKeep implementation. Because the app was easily loaded onto phones and simple to navigate, acceptance was quick and enthusiastic.
Even some of the older team members who were generally skeptical about technology found the tool useful and simple. They just check it every day to pull up their work orders; they don’t have to ask what needs to be done. UpKeep tells them the jobs, in priority order, and where the parts are located. The team is more efficient.
Tracking Inventory Eliminates Double Buying
Maintenance managers approved emergency part purchases in order to deliver superior customer service during equipment breakdowns. However, this was costing the company tens of thousands of dollars.
UpKeep now tracks all available spare parts. When technicians need parts, they can see if the company has it, find its exact location and note the cost. Since emergency parts are needed between two and four times a month, this improvement has saved the company a considerable amount of money.
Want to keep reading?
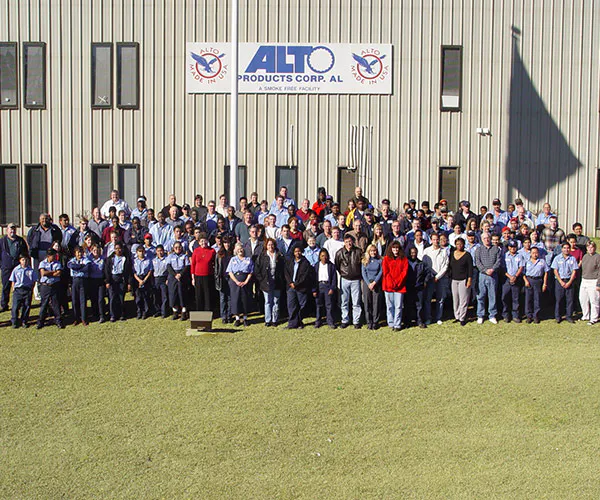
Equipment / Manufacturing
Alto Products moves from reactive to preventive maintenance
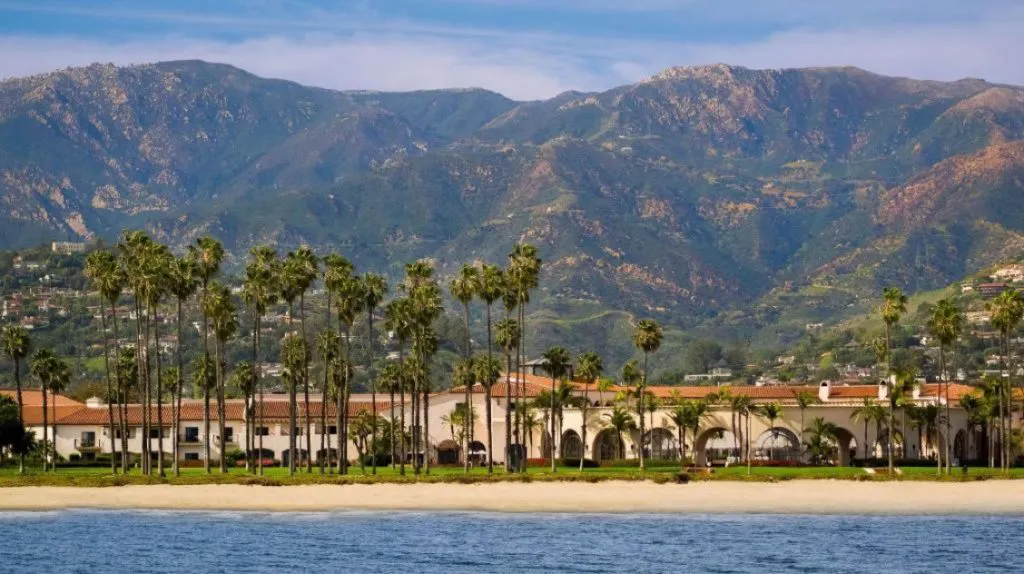
Equipment / Manufacturing
Innovative Micro Technology creates a safety-focused culture
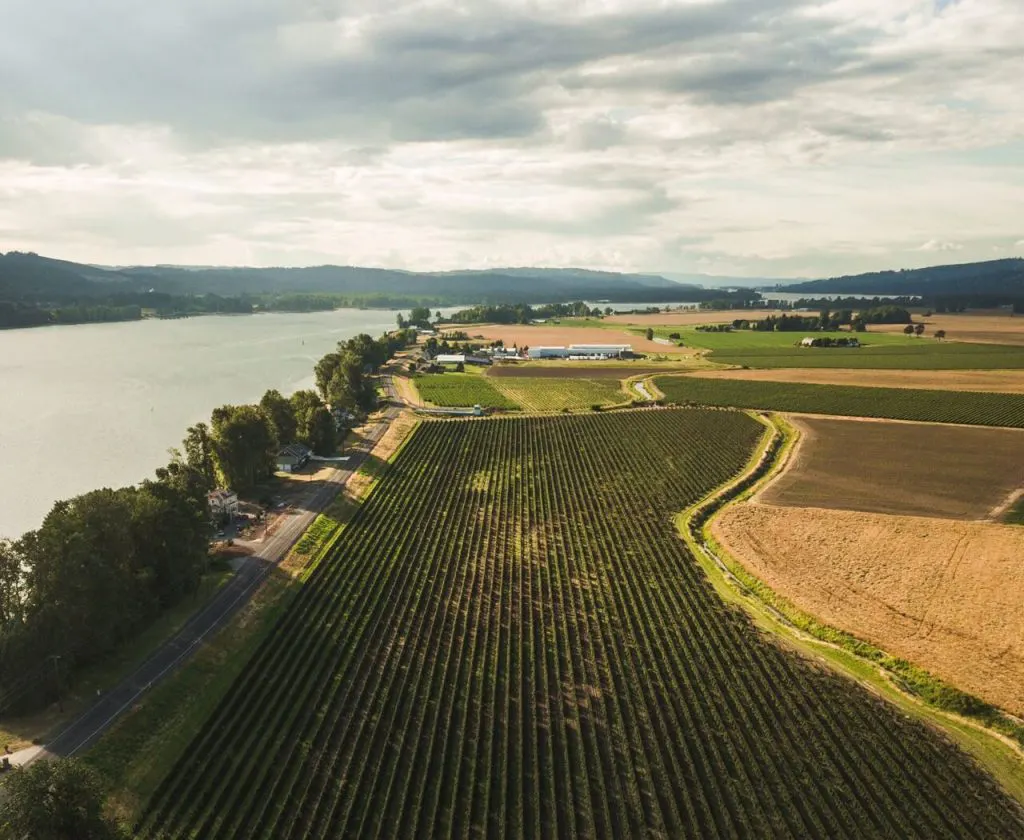
Equipment / Manufacturing
Columbia Fruit saves money with organized inventory
4,000+ COMPANIES RELY ON ASSET OPERATIONS MANAGEMENT
Leading the Way to a Better Future for Maintenance and Reliability
Your asset and equipment data doesn't belong in a silo. UpKeep makes it simple to see where everything stands, all in one place. That means less guesswork and more time to focus on what matters.
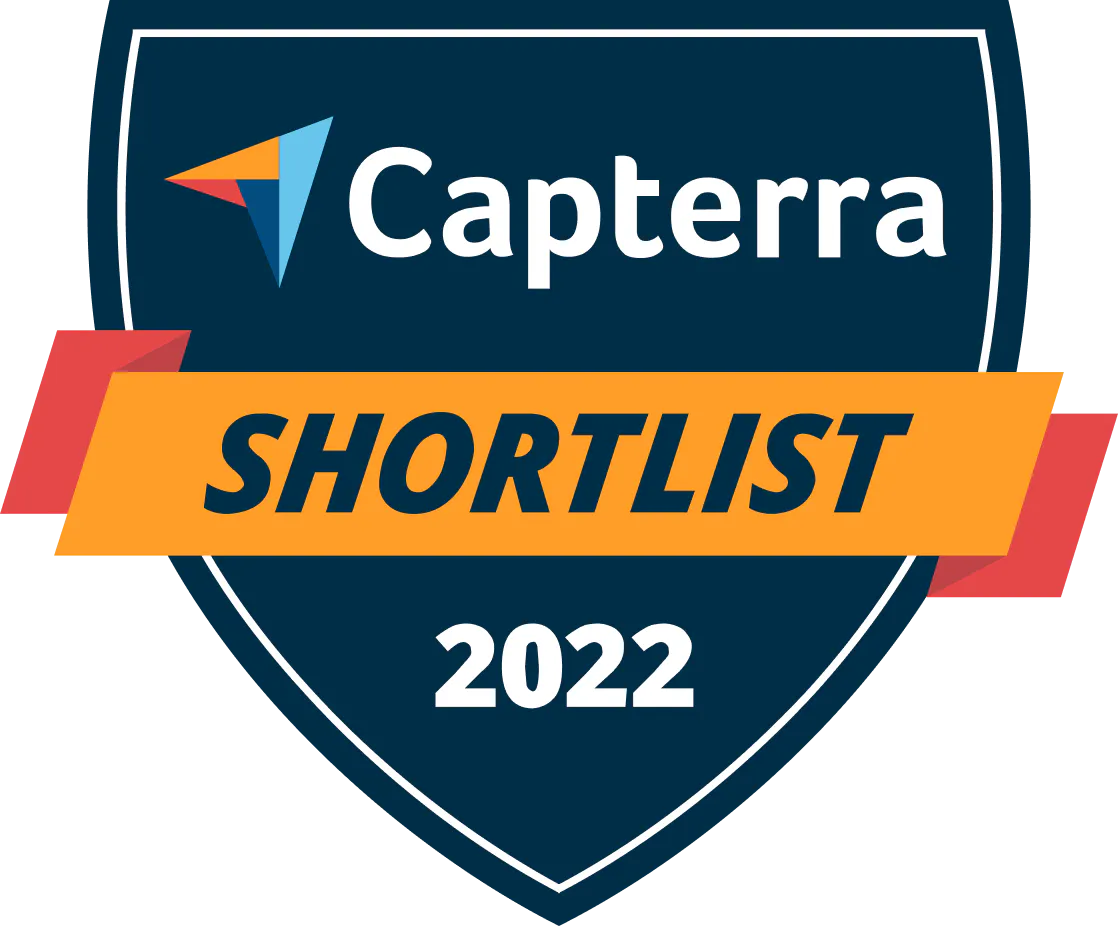

![[Review Badge] GetApp CMMS 2022 (Dark)](https://www.datocms-assets.com/38028/1673900459-get-app-logo-dark.png?auto=compress&fm=webp&w=347)
![[Review Badge] Gartner Peer Insights (Dark)](https://www.datocms-assets.com/38028/1673900494-gartner-logo-dark.png?auto=compress&fm=webp&w=336)
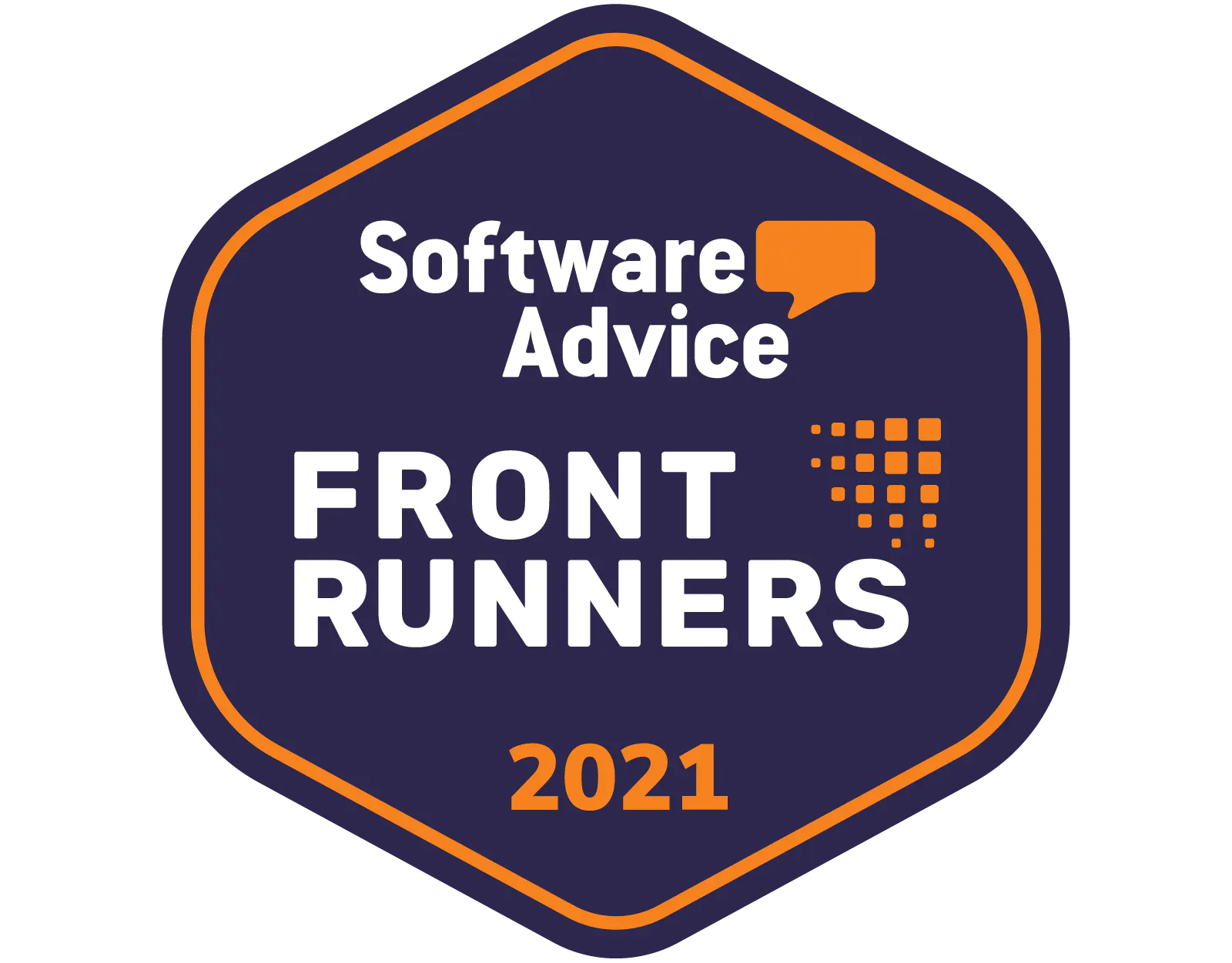