Success Story
Unilever & Hellman's Mayonnaise Adopt UpKeep CMMS to Track KPIs and Inventory
Before implementing UpKeep, the Unilever Team responsible for Hellman’s Mayonnaise, located in Rexdale, Canada, used SAP for Work Orders and Inventory management. After a successful migration, Unilever now has real-time KPIs and improved Inventory management, making finding and re-ordering Parts much easier.
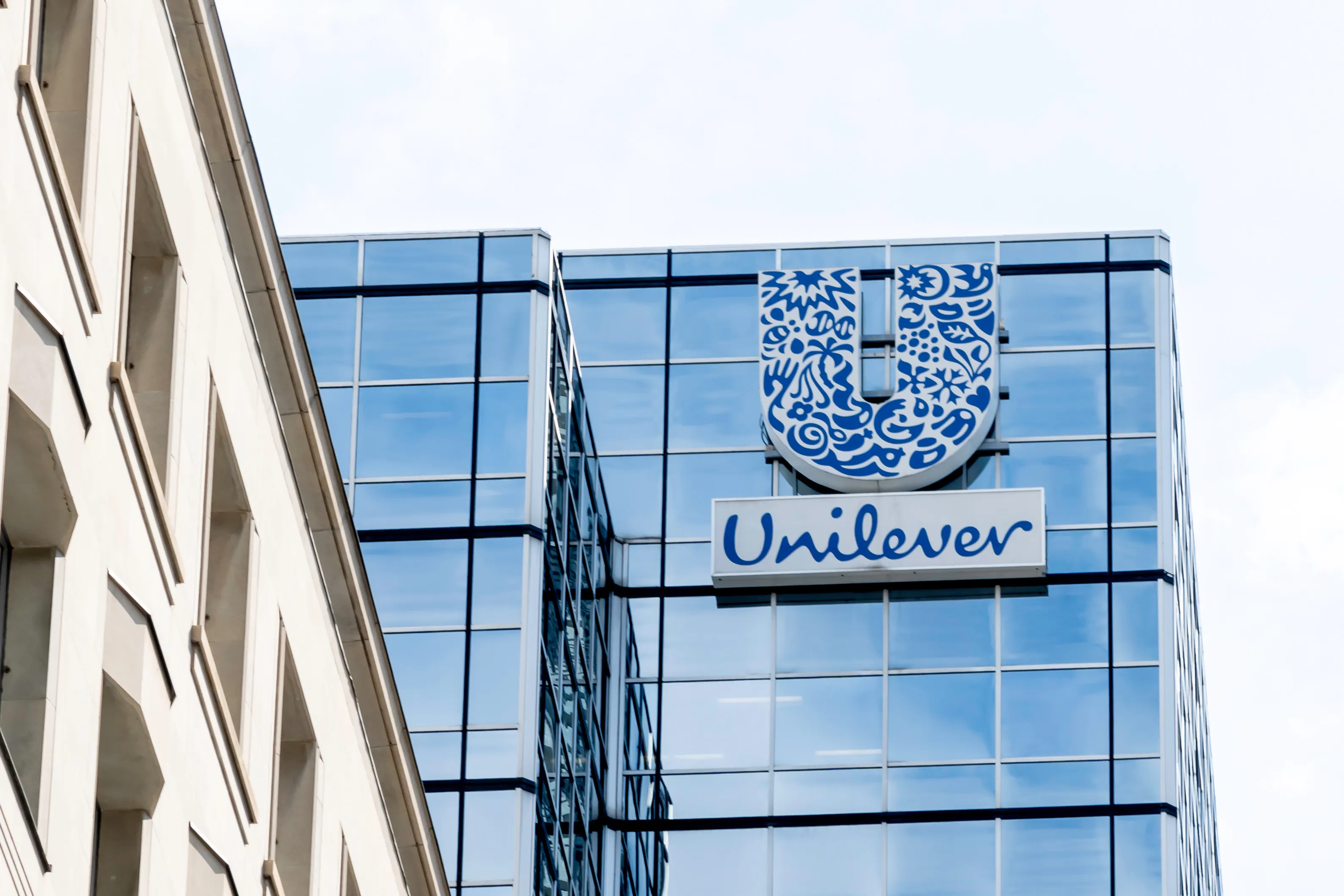
Unilever is a multinational manufacturing conglomerate specializing in Consumer Goods, Food, Home Care, Personal Care, Refreshments, Marketing & Advertising, Retail, Purpose, and FMCG. We had the opportunity to sit down with Hammad Qadeer, Maintenance and Planning Scheduler, at their Rexdale, Canada facility, which is responsible for manufacturing the beloved Hellman’s Mayonnaise brand.
Challenge
When Hammad joined Unilever six months ago, they were transitioning off of SAP and onto UpKeep. SAP had only provided a desktop experience that proved too cumbersome for their Technicians.
Moreover, the biggest challenges the Unilever Team faced were related to Parts and Inventory. Finding Parts, not having enough Parts in the current inventory, tracking Parts that should have been ordered but hadn’t, and knowing which assets used which Parts were only some of the challenges the team encountered daily.
Solution
As the Planner managing the work schedule of 10 Technicians and incoming requests, the new solution needed comprehensive administrative and scheduling capabilities and a mobile solution, something their Technicians could easily use while away from a computer.
Hammad makes approximately 90% of all Work Orders and spends about 80% of his time using UpKeep’s web application. When he’s out on the floor, it’s usually for emergency Work Orders, and he particularly likes the ability to take pictures to start a draft of a Work Order and then use the web application back in his office to finalize the details and assign them out.
Most importantly, UpKeep’s Parts and Inventory Management provides easy-to-find pictures and details about Inventory, quantities, and minimum quantities. The pictures, in particular, are key because previously in SAP; one had to try and remember a code or Parts number to identify the particular item. With pictures, the Technicians find Parts much more quickly.
Additionally, Hammad has successfully migrated from SAP to UpKeep easily and without additional help. He identified specific migration areas, starting with Operator PMs, and migrated off SAP over time.
Results
Unilever now has real-time KPIs that they use to track, understand, and improve performance. Before UpKeep, KPIs had been a goal but not one that had fully materialized. The Unilever Team combines UpKeep’s out-of-the-box reporting and dashboards, along with some custom reports and dashboards to track KPIs like Work Order Completion Status, Work Order Completion Rates and Approval Request Time. Hammad has also created custom reports and dashboards which took him less than a day and he now has all the data his management needs in real-time.
What's Next?
The Unilever Team is excited about UpKeep’s new offline mobile capabilities, especially because their storeroom where Parts are kept has spotty wifi coverage. Searching for Parts to attach to Work Orders in real-time will help the Team continue working without interruption, furthering their ability to focus on their daily maintenance activities.
Want to keep reading?
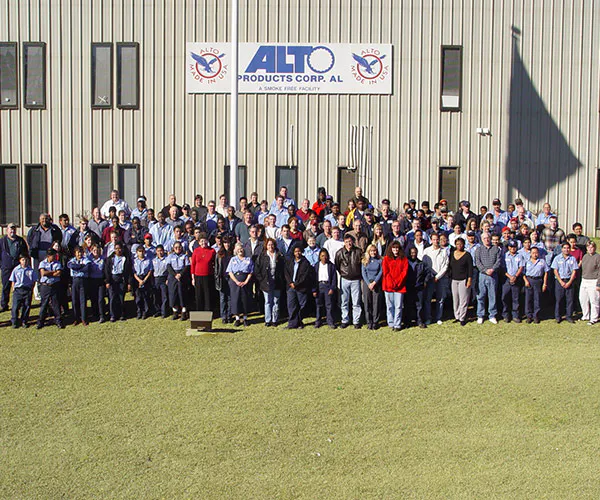
Equipment / Manufacturing
Alto Products moves from reactive to preventive maintenance
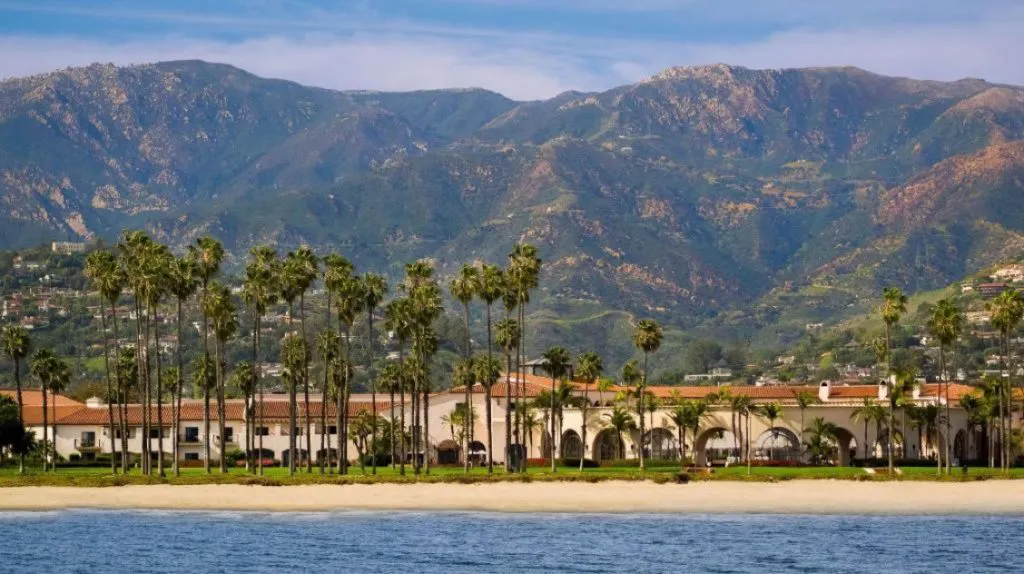
Equipment / Manufacturing
Innovative Micro Technology creates a safety-focused culture
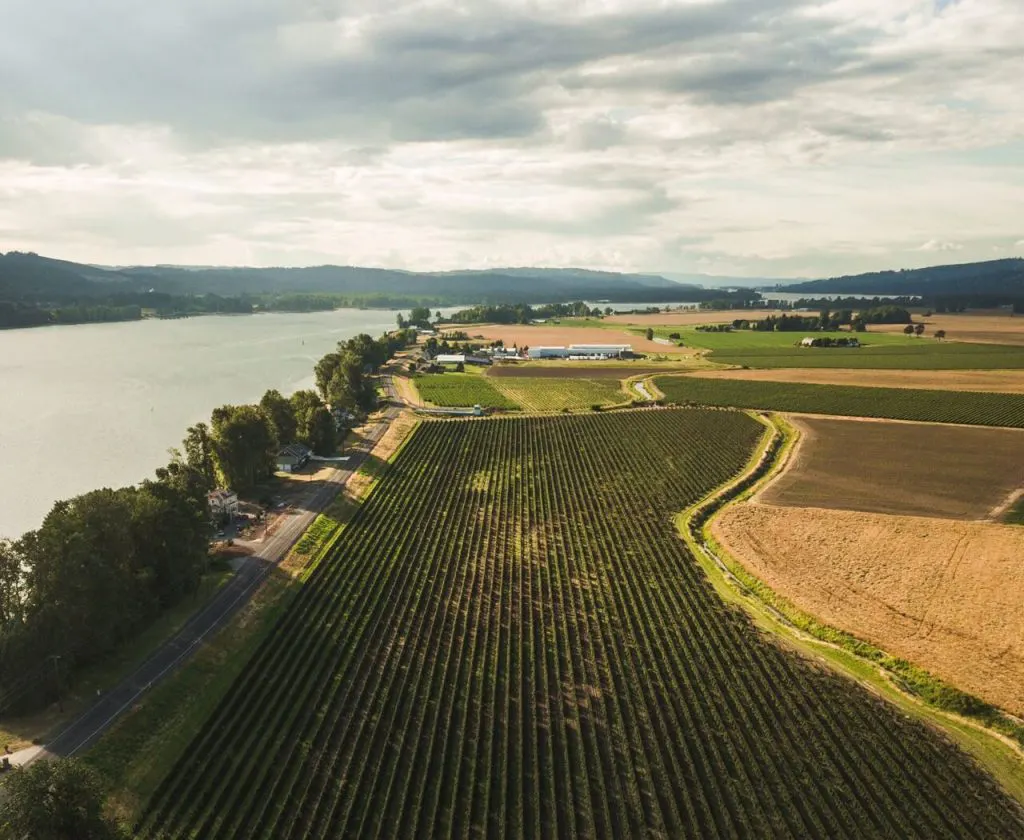
Equipment / Manufacturing
Columbia Fruit saves money with organized inventory
4,000+ COMPANIES RELY ON ASSET OPERATIONS MANAGEMENT
Leading the Way to a Better Future for Maintenance and Reliability
Your asset and equipment data doesn't belong in a silo. UpKeep makes it simple to see where everything stands, all in one place. That means less guesswork and more time to focus on what matters.
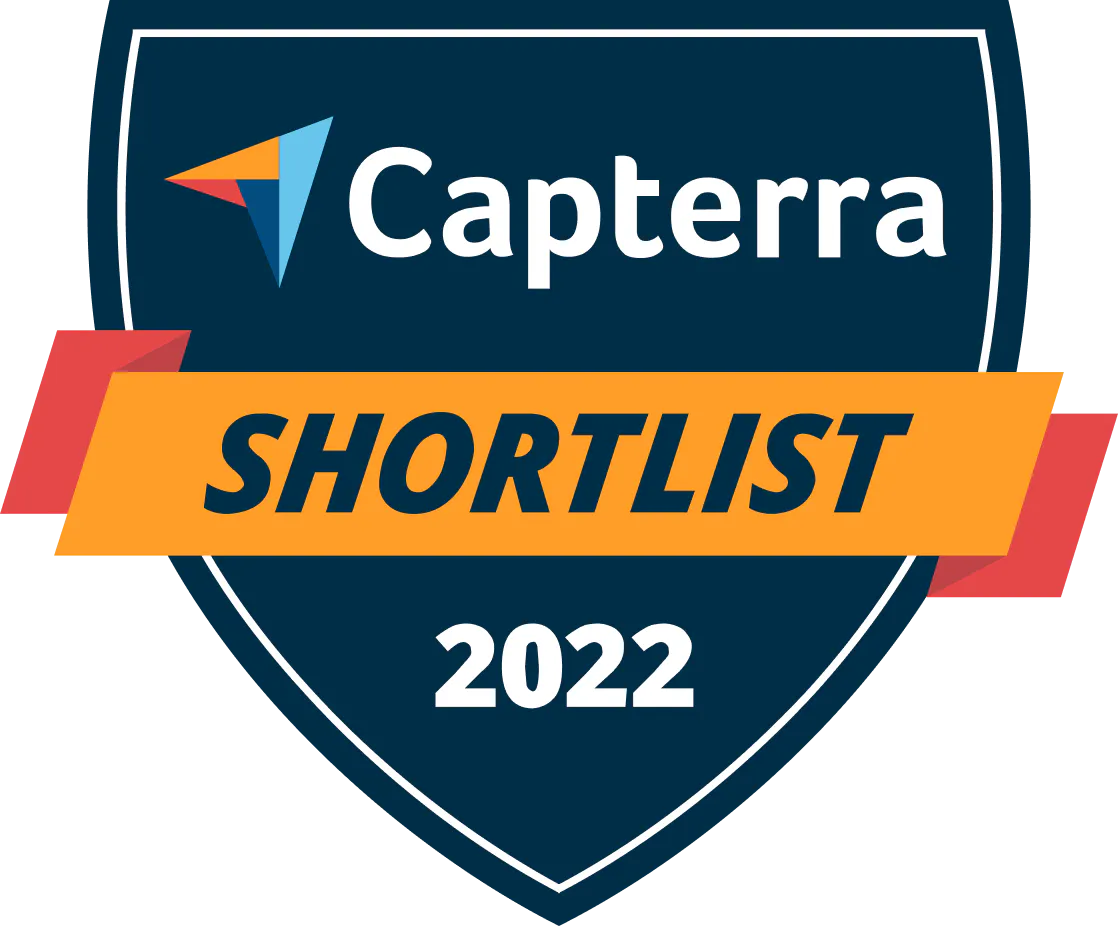

![[Review Badge] GetApp CMMS 2022 (Dark)](https://www.datocms-assets.com/38028/1673900459-get-app-logo-dark.png?auto=compress&fm=webp&w=347)
![[Review Badge] Gartner Peer Insights (Dark)](https://www.datocms-assets.com/38028/1673900494-gartner-logo-dark.png?auto=compress&fm=webp&w=336)
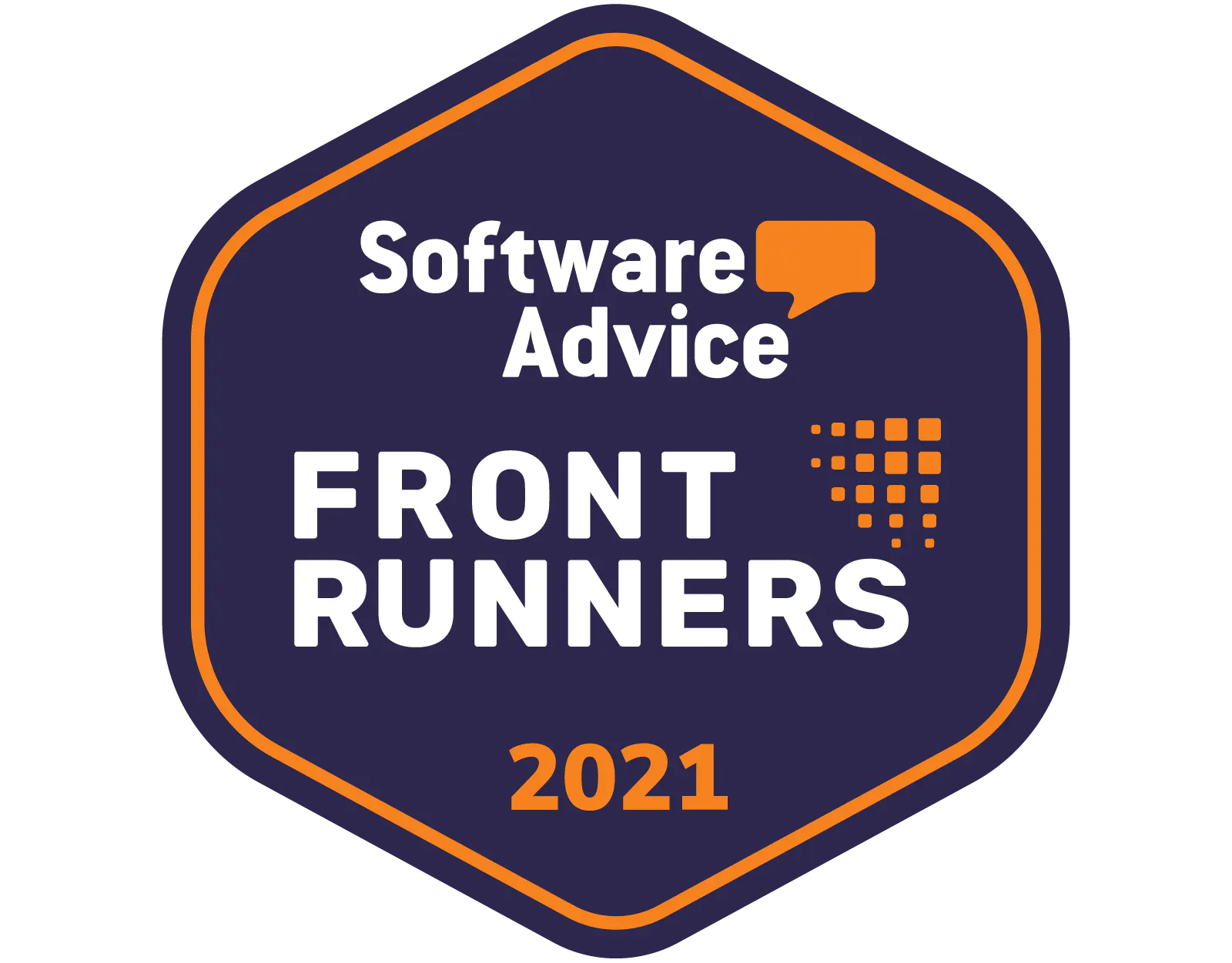