Raceway Car Wash
Raceway Car Wash, a rapidly growing chain with 44 locations across Arizona, California, Nevada, and Texas, faced significant challenges in managing maintenance, inventory, and technician coordination. With aggressive expansion goals to reach 200 locations, Raceway needed a solution that could scale with them. Their reliance on spreadsheets and manual tracking was causing inefficiencies, delays, and unexpected downtime.
By implementing UpKeep, Raceway transitioned from reactive to proactive maintenance, optimizing their operations, improving technician performance, and reducing costs.
Overview
Raceway Car Wash, a rapidly growing chain with 44 locations across Arizona, California, Nevada, and Texas, faced significant challenges in managing maintenance, inventory, and technician coordination. With aggressive expansion goals to reach 200 locations, Raceway needed a solution that could scale with them. Their reliance on spreadsheets and manual tracking was causing inefficiencies, delays, and unexpected downtime.
By implementing UpKeep, Raceway transitioned from reactive to proactive maintenance, optimizing their operations, improving technician performance, and reducing costs.
The Challenge: Managing Maintenance at Scale
Managing maintenance at a tunnel car wash is unlike any other industry. Raceway Car Wash operates 44 locations across four states, each requiring the constant upkeep of high-use, water-exposed machinery. Their maintenance challenges stemmed from several industry-specific pain points:
1. Tracking Thousands of Parts Across Locations
Each Raceway location houses hundreds of critical components, including nozzles, pumps, belts, brushes, and motors—all of which experience high wear in a moisture-heavy environment. Without a centralized inventory system, parts were often misplaced, leading to:
- Delays in repairs due to missing or unavailable parts.
- Over-ordering of parts at certain locations, while others ran out of stock.
- Unnecessary emergency orders, increasing operational costs.
2. Heavy Reliance on Equipment Uptime
The success of a tunnel car wash depends on keeping equipment running at peak performance. Unlike other industries, a single equipment failure can halt operations entirely, leading to customer dissatisfaction. Raceway’s existing system lacked real-time visibility into which assets were underperforming, making it impossible to:
- Predict failures before they caused downtime.
- Ensure that preventative maintenance schedules were followed across all locations.
- Monitor asset health trends across multiple regions.
3. Transitioning from Reactive to Preventative Maintenance
Without a structured maintenance program, Raceway’s technicians were often in constant firefighting mode. Reactive repairs dominated their work orders, leading to:
- Unplanned shutdowns, especially during peak hours.
- Higher costs from emergency repairs and last-minute contractor hires.
- Decreased equipment lifespan, with core machinery failing well before its expected 10-year depreciation schedule.
4. Operational Inefficiencies and Technician Management
Raceway’s maintenance teams were spread across multiple states, relying on manual tracking via Google Sheets, emails, and texts. This lack of standardization led to:
- Inconsistent maintenance records, making it difficult to track equipment history.
- Missed or delayed work orders, as communication was scattered across different channels.
- No standardized technician workflows, creating discrepancies in maintenance execution from one location to another.
The Solution: Implementing UpKeep for Centralized Maintenance Management
To address these challenges, Raceway Car Wash turned to UpKeep, a mobile-first CMMS (Computerized Maintenance Management System) designed to streamline maintenance and inventory operations.
1. Centralized Work Order Management
With UpKeep, Raceway eliminated spreadsheets and manual tracking. All work orders are now digitally created, assigned, and tracked in real time, ensuring that maintenance requests are efficiently prioritized and completed.
- Technicians receive clear instructions and necessary parts for each work order.
- Managers can track work order completion rates, identify bottlenecks, and adjust labor allocation accordingly.
- The backlog of reactive maintenance is gradually being replaced by a structured preventive maintenance plan.
"The work order analytics alone provided incredible value, showing us exactly where we could improve efficiency and reduce costs."
2. Proactive Maintenance and Asset Tracking
By leveraging UpKeep’s preventive maintenance scheduling, Raceway reduced equipment failures and extended the life of high-cost assets like vacuums, hydraulic motors, and drying systems.
- Preventive maintenance (PM) work orders now exceed reactive maintenance work, improving uptime and customer satisfaction.
- Equipment reliability is closely monitored, and recurring failures are addressed proactively.
3. Improved Technician Performance and Accountability
UpKeep provided Raceway with detailed insights into technician productivity, helping them optimize performance:
- Work order completion rates per technician are now tracked, with a target of 80% compliance.
- PM compliance is set at 100%, with incentives for technicians who meet this requirement.
- Work order hours documented vs. total hours worked is monitored to ensure strong adoption of UpKeep among technicians.
4. Smarter Parts and Inventory Management
With 1.5 years of data on parts consumption, Raceway can now optimize inventory levels, reduce cash flow waste, and negotiate better volume discounts with vendors.
- Parts usage trends are analyzed to ensure the right stock levels at each location.
- Overstocking and emergency orders have decreased, improving cash flow efficiency.
The Results: A Scalable Maintenance Operation
The implementation of UpKeep delivered tangible results, transforming Raceway’s maintenance and inventory management processes.
- Increased technician adoption: By incentivizing proper use of UpKeep, Raceway ensured widespread adoption, making maintenance workflows more efficient.
- Improved work order tracking: Managers now have visibility into maintenance trends, helping them deploy labor resources where they’re needed most.
- Optimized inventory management: Raceway reduced unnecessary spending on spare parts while ensuring critical components were always available.
- Operational efficiency gains: Work order analytics provided insights that led to improved training and optimized processes across all locations.
- Support for future growth: With a solid maintenance framework in place, Raceway is well-positioned to scale to its goal of 200 locations without sacrificing reliability.
"UpKeep helped us build a common language across all locations, from asset names to parts management, which has been crucial for training and scaling."
What’s Next for Raceway?
With UpKeep’s foundation in place, Raceway Car Wash is looking to expand its use of predictive maintenance and analytics. Their next steps include:
- Exploring predictive maintenance: Leveraging UpKeep’s data to anticipate failures before they occur.
- Enhancing reporting and analytics: Using work order trends and labor statistics to refine maintenance strategies further.
- Scaling to 200 locations: Continuing to build on the success of UpKeep as Raceway expands into new markets.
By embracing UpKeep’s technology, Raceway Car Wash has turned maintenance from a challenge into a competitive advantage, ensuring reliable operations, satisfied customers, and a clear path for future growth.
Conclusion
Raceway Car Wash’s journey with UpKeep highlights the power of a modern, data-driven maintenance strategy. By replacing manual tracking with a scalable, centralized system, they have improved efficiency, reduced downtime, and set the stage for continued expansion.
For other car wash businesses facing similar challenges, Raceway’s success story demonstrates how investing in the right maintenance software can drive operational excellence and long-term growth.
Want to see how UpKeep can help your car wash streamline maintenance and inventory?
Request a demo today!
Want to keep reading?
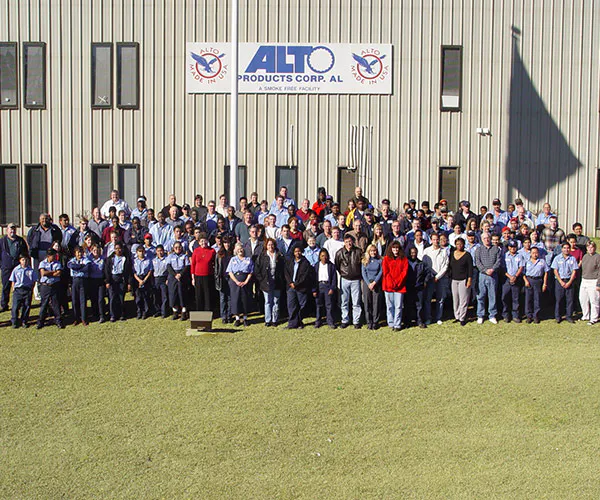
Equipment / Manufacturing
Alto Products moves from reactive to preventive maintenance
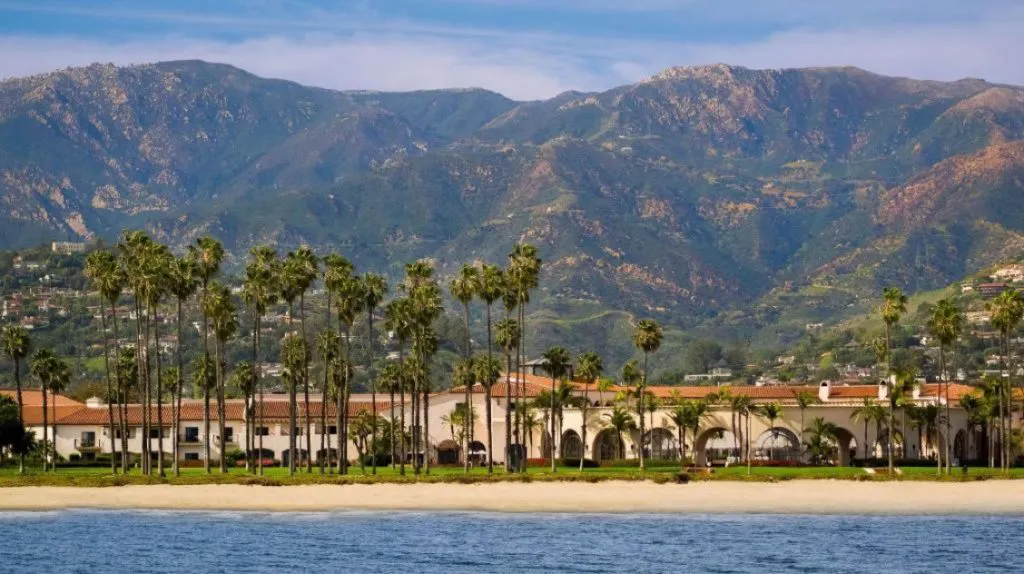
Equipment / Manufacturing
Innovative Micro Technology creates a safety-focused culture
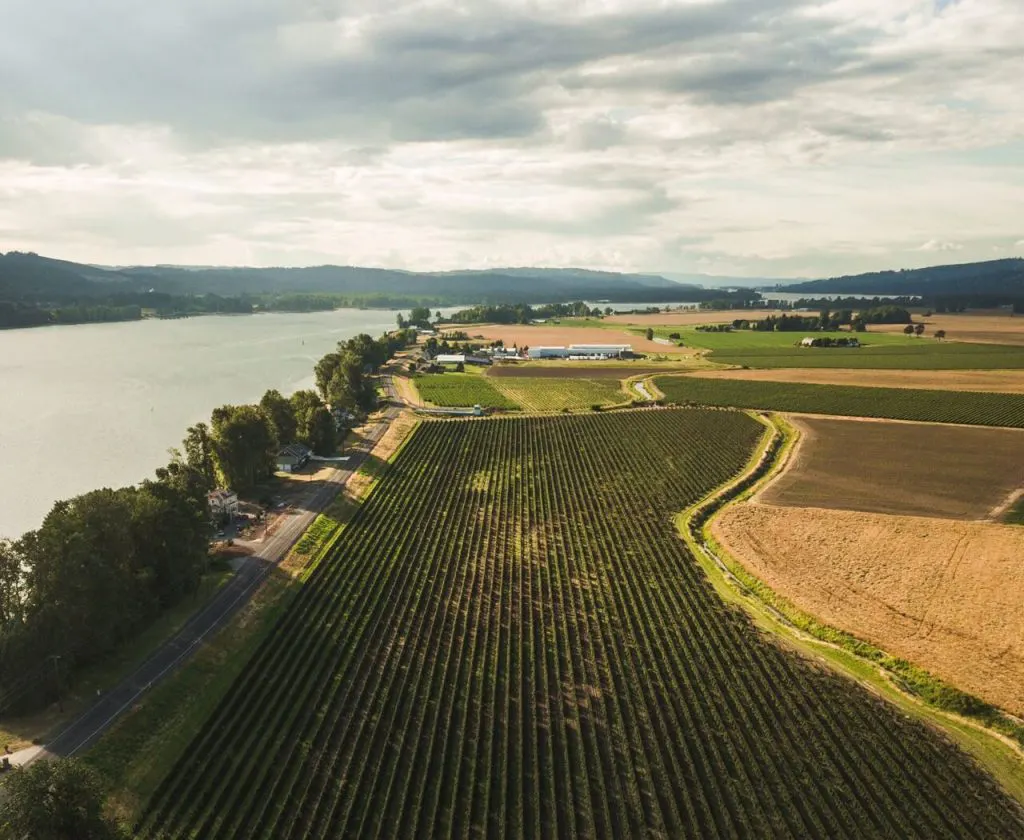
Equipment / Manufacturing
Columbia Fruit saves money with organized inventory
4,000+ COMPANIES RELY ON ASSET OPERATIONS MANAGEMENT
Leading the Way to a Better Future for Maintenance and Reliability
Your asset and equipment data doesn't belong in a silo. UpKeep makes it simple to see where everything stands, all in one place. That means less guesswork and more time to focus on what matters.
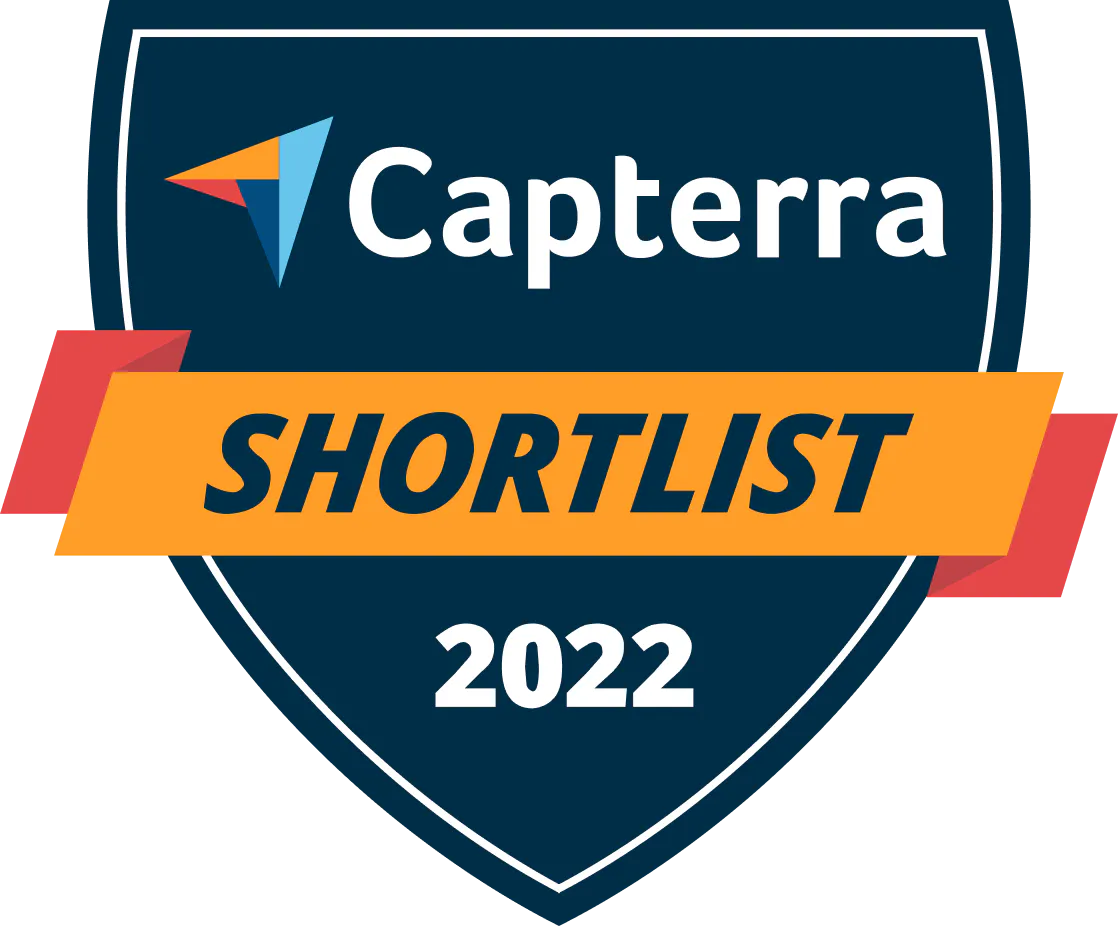

![[Review Badge] GetApp CMMS 2022 (Dark)](https://www.datocms-assets.com/38028/1673900459-get-app-logo-dark.png?auto=compress&fm=webp&w=347)
![[Review Badge] Gartner Peer Insights (Dark)](https://www.datocms-assets.com/38028/1673900494-gartner-logo-dark.png?auto=compress&fm=webp&w=336)
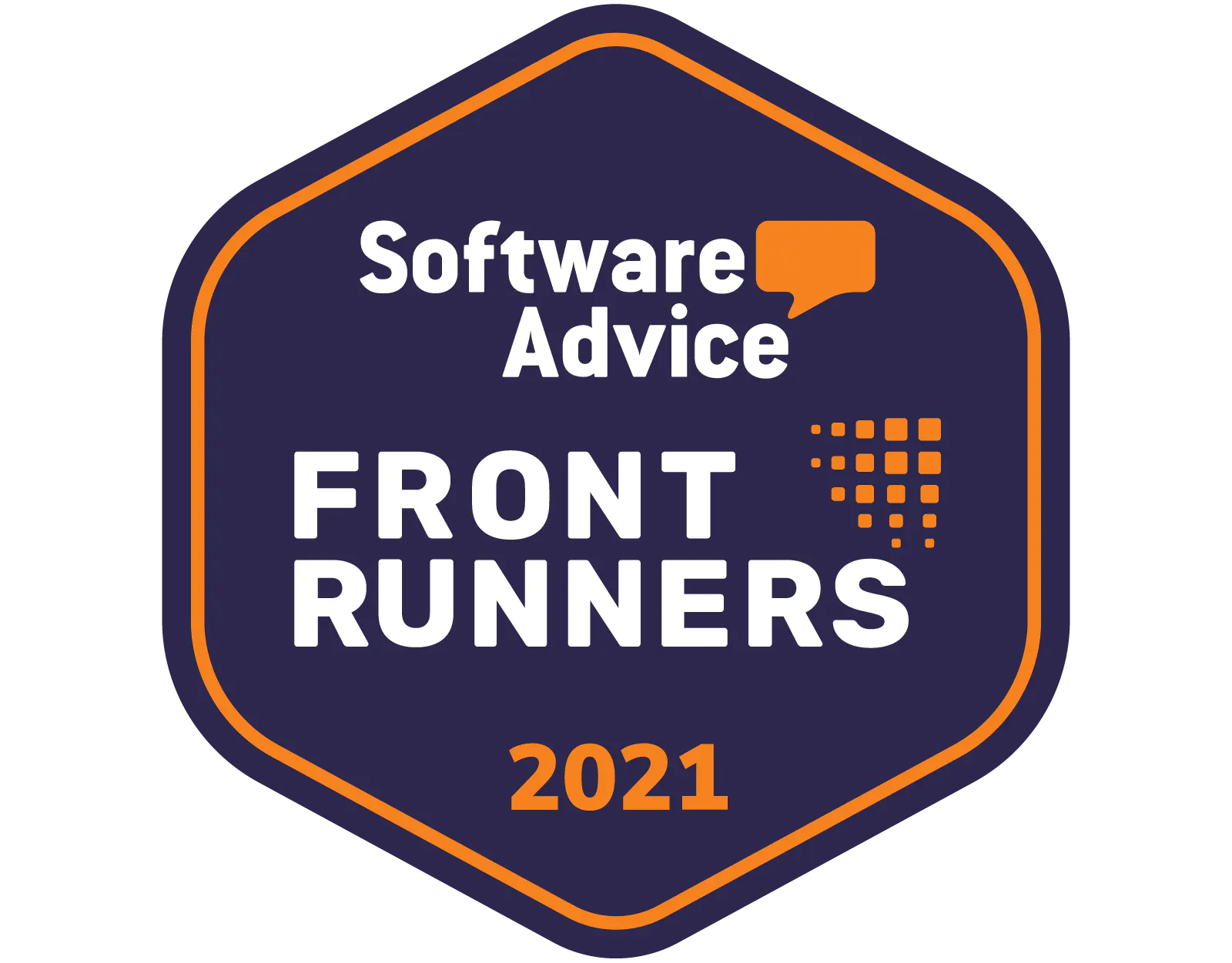