Distribution company streamlines communication and reduces vendor expenses
A distribution company ships a wide variety of products including compressors, centrifugal dryers, filters, lubricants, and other industrial items to its customers. As a medium-sized distribution center, the company has a variety of equipment. Though the team isn’t at an Amazon level, they are striving to be with the help of UpKeep’s asset operations management solution.
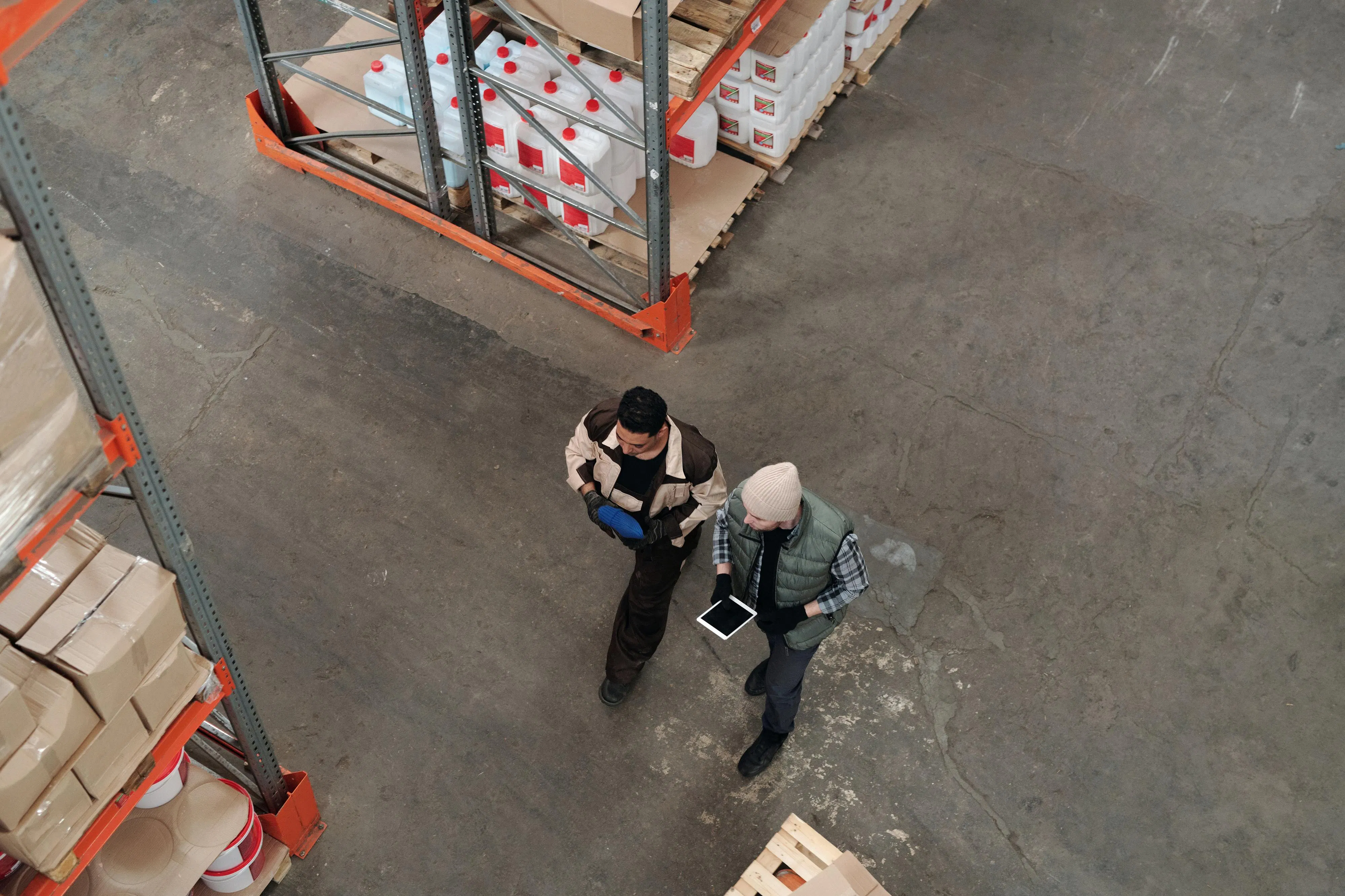
Problem
Prior to implementing UpKeep’s asset operations management solution the company had no computerized maintenance system. Instead, when maintenance or repairs were needed, a supervisor might send an email, call, or simply catch the manager passing by. It was a very manual process and requests were easily lost or forgotten.
In addition, the company had no way to track and document that it was meeting various EHS and OSHA requirements for different processes.
Solution
After checking out a handful of computerized maintenance management systems (CMMS), the manager and his newly hired maintenance technician selected UpKeep. They were looking for a system that was user-friendly and not complicated. UpKeep checked all the boxes.
The company implemented UpKeep in early 2021 and has been pleased with its ability to streamline work order requests and communication between the maintenance team and the distribution center floor. The team leads and supervisors who have direct access to UpKeep work on 10 to 12 different assets in the distribution center.
Besides being able to easily collect, track and provide status updates on work orders, the system has allowed the maintenance team to shift more repairs from third-party vendors to in-house, which means faster resolution and lower costs.
Results
One priority for the distribution company was to tighten up its EHS processes and tasks. The team members put reoccurring safety tasks like checking fire-related equipment and emergency lights into UpKeep. They now have a tool that automates the process, and they don’t have to try to remember whether a certain task was completed last month. As a result, when the manager goes through the EHS audits, he can show the documentation on their preventative and reactive maintenance tasks.
In addition, the company has been able to reduce its downtime by between 20 percent and 30 percent, primarily by taking more of the work in-house. In the past, if a machine went down, it was down for eight to 12 hours. Now, downtime is more like two or three hours.
Easy Onboarding, Reliable Access
When choosing a maintenance solution, the manager had to make sure that it not only fit his skill set, but the skill sets of other team members as well. Since UpKeep is a very user-friendly solution, onboarding was relatively easy for the team. Learning about UpKeep and its different modules went well.
The maintenance technician loves UpKeep; it's simple for him to navigate to get the information he needs. Since it’s web-based, IT support wasn’t needed to figure out how to get UpKeep on the company’s server or to determine who should have access. Instead, team members just go to the web to access it.
In addition, the team has been impressed with UpKeep’s reliability. One thing the manager appreciates especially is the up-time of UpKeep. Oftentimes, websites aren’t working because they’re down for maintenance or other problems. The team has found that UpKeep rarely goes down when technicians need to access it.
A Change in Culture
Prior to UpKeep, the manager was always concerned that too much information resided with the individual technician. Since everything was communicated by voice or email, it was easy to lose requests when the manager was away. Now, there’s a system that holds all that information.
The manager doesn’t accept work requests while on the floor anymore. Instead, he lets them know that, unless it’s a real emergency, they have to put it in UpKeep. He is trying to change the culture and create some accountability and responsibility for operations.
Seamless Communications
Once the work orders are entered in UpKeep, the maintenance team meets every Monday to set priorities. If there are tasks that require purchasing supplies, parts, or tools, they categorize them and respond back to the requesters to let them know what's going on and what they’re waiting on.
The company has found that UpKeep is very easy for team leads and supervisors to enter and check on work orders to get a quick status update. It makes communication seamless for them – they’re able to communicate with those who are entering the work order.
This is a big change from the past when maintenance requests frequently received no response. Then, it seemed to take forever to get anything done and communication was poor. Solving these two issues has been the biggest win for the company.
Validating the Need for Maintenance
Besides helping to streamline communications between the operators and maintenance staff, UpKeep holds the maintenance history and tracking of assets and completed work. They put in their hours and log everything they’ve done. This helps them see what has been worked on and helps validate the need for maintenance technicians.
Capturing Data for the Long Run
The team is now working on building comprehensive historical records for each of its assets. The goal is to capture information as they repair things. Because pictures say so much more than words, they take pictures of how to fix something to build a historical record. They are also working to collect serial numbers, who they bought parts from, and other data. That information will help them, in the long run, to build some sustainability in their maintenance program.
The manager wants to make sure that if he were to leave, the maintenance system wouldn’t fall apart. The system should be able to take care of itself – it shouldn’t be person-dependent to get things done.
For example, the company was having trouble with a dock that required a special method to lock it out. The manager took some pictures to show how to properly lock it out. He’s trying to utilize UpKeep for similar situations to make references for different types of unique situations. It helps the team better capture certain processes.
A second example occurred when a part needed to be ordered. The vendor could go right to the website and see where the parts were ordered from. By having the information and the data in the system, the vendor could go ahead and move forward in getting that machine fixed as opposed to always waiting on the manager.
A Safer Work Environment
Since UpKeep tracks maintenance history, the company can more easily adhere to EHS and OSHA regulations. They can see and schedule regular reactive tasks or proactive tasks that need to take place. When audits take place, it’s easy to show the monthly inspection records in UpKeep and let them know that the team is in control of maintenance.
The team is continuing to add to its reoccurring PMs, including manufacturer-recommended service. From a documentation standpoint, the manager can tell them that they have a maintenance system, which says wonders to those entities that come on-site and ask for documentation.
Bringing Repairs In-House
Prior to UpKeep, the distribution company frequently brought in third-party vendors to handle and manage repairs and maintenance. When the manager came on board, he didn’t hire a maintenance technician for months. They had to call vendors to fix things, especially when it came to safety.
When the maintenance technician was hired, the first thing that they did was find a system for him to better support operations. The goal was to have them run effectively 16 hours a day. UpKeep gives the technician a place where he can keep records, go back and look at particular work orders that were placed, and do much of the work internally.
Now, the company has greatly reduced the number of vendors it uses. UpKeep has allowed them to learn how to perform PMs on certain pieces of equipment. It has also begun to help them know which spare parts they need to have on-site. As a result, repairs can be completed quickly and the center is able to reduce equipment downtime.
When assets go down, the maintenance team is able to respond quickly. UpKeep allows employees to communicate it very quickly, and then to be able to respond. It reduces every type of downtime. For example, the company’s small parcel line alone processes a couple of thousand boxes per day. As a very fast-paced distribution center, a conveyor going down means money is lost and shipments are delayed.
According to the manager, when you’re working with vendors, you’re at the mercy of when they can make the call. Most of the time, it’s the next day before they can get vendors to come in for critical issues. There’s a 20 percent to 30 percent reduction in downtime when they can react quickly.
Future Plans
As the company enters 2022, the company is going to measure the effectiveness of work orders, response time, downtime, and utilization. The team also wants to identify which machines go down most frequently. They want to start driving corrective action and identifying the root causes, as well as being more proactive on their highly technical assets.
In addition, the company hopes to use UpKeep to share and drive continuous improvement. The manager wants his operators and team leads to share ideas on how to make things better. He doesn’t want his operators and team leads to be complacent or think that something can’t be fixed. Instead, he wants to hear their ideas so that they can create improvements.
Want to keep reading?
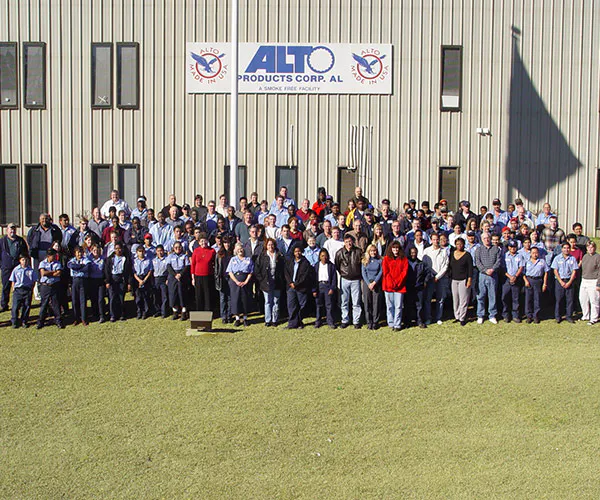
Equipment / Manufacturing
Alto Products moves from reactive to preventive maintenance
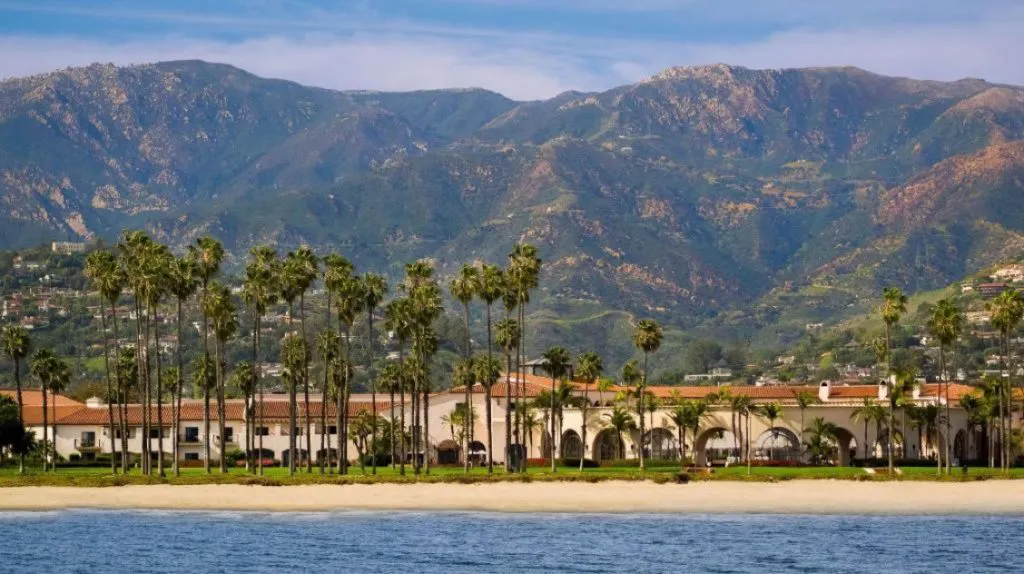
Equipment / Manufacturing
Innovative Micro Technology creates a safety-focused culture
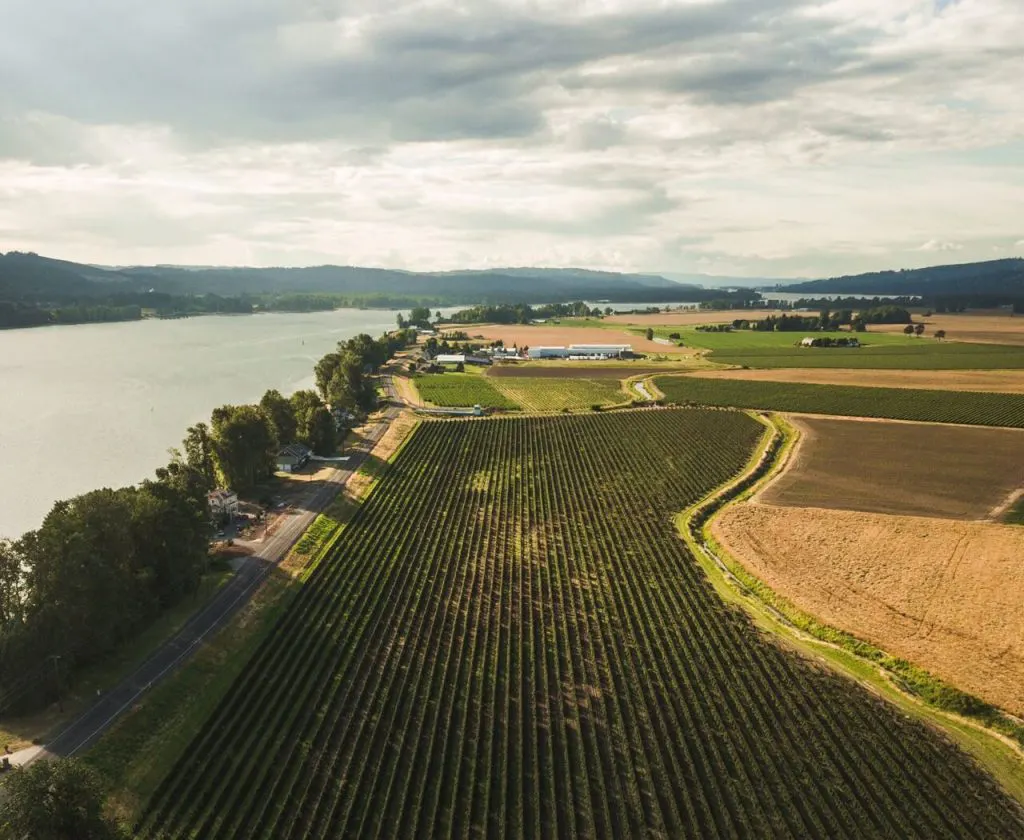
Equipment / Manufacturing
Columbia Fruit saves money with organized inventory
4,000+ COMPANIES RELY ON ASSET OPERATIONS MANAGEMENT
Leading the Way to a Better Future for Maintenance and Reliability
Your asset and equipment data doesn't belong in a silo. UpKeep makes it simple to see where everything stands, all in one place. That means less guesswork and more time to focus on what matters.
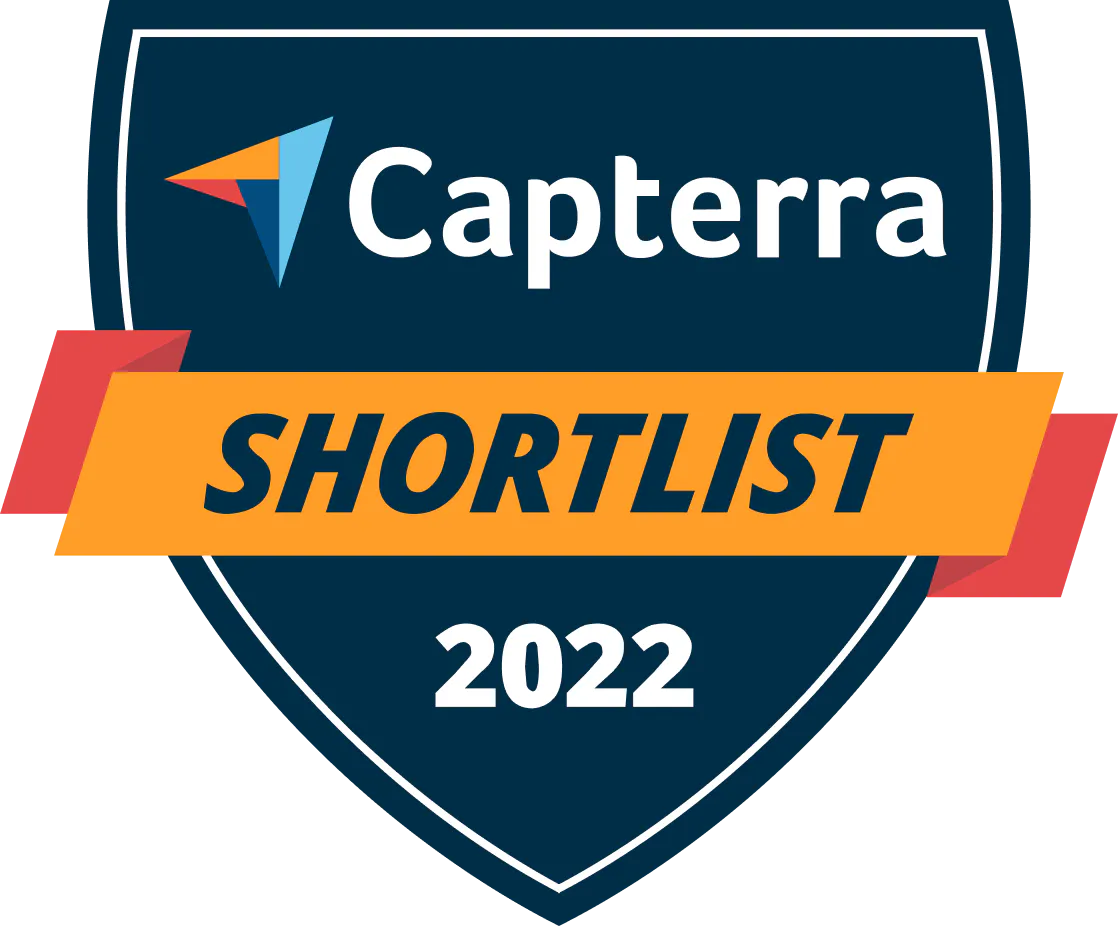

![[Review Badge] GetApp CMMS 2022 (Dark)](https://www.datocms-assets.com/38028/1673900459-get-app-logo-dark.png?auto=compress&fm=webp&w=347)
![[Review Badge] Gartner Peer Insights (Dark)](https://www.datocms-assets.com/38028/1673900494-gartner-logo-dark.png?auto=compress&fm=webp&w=336)
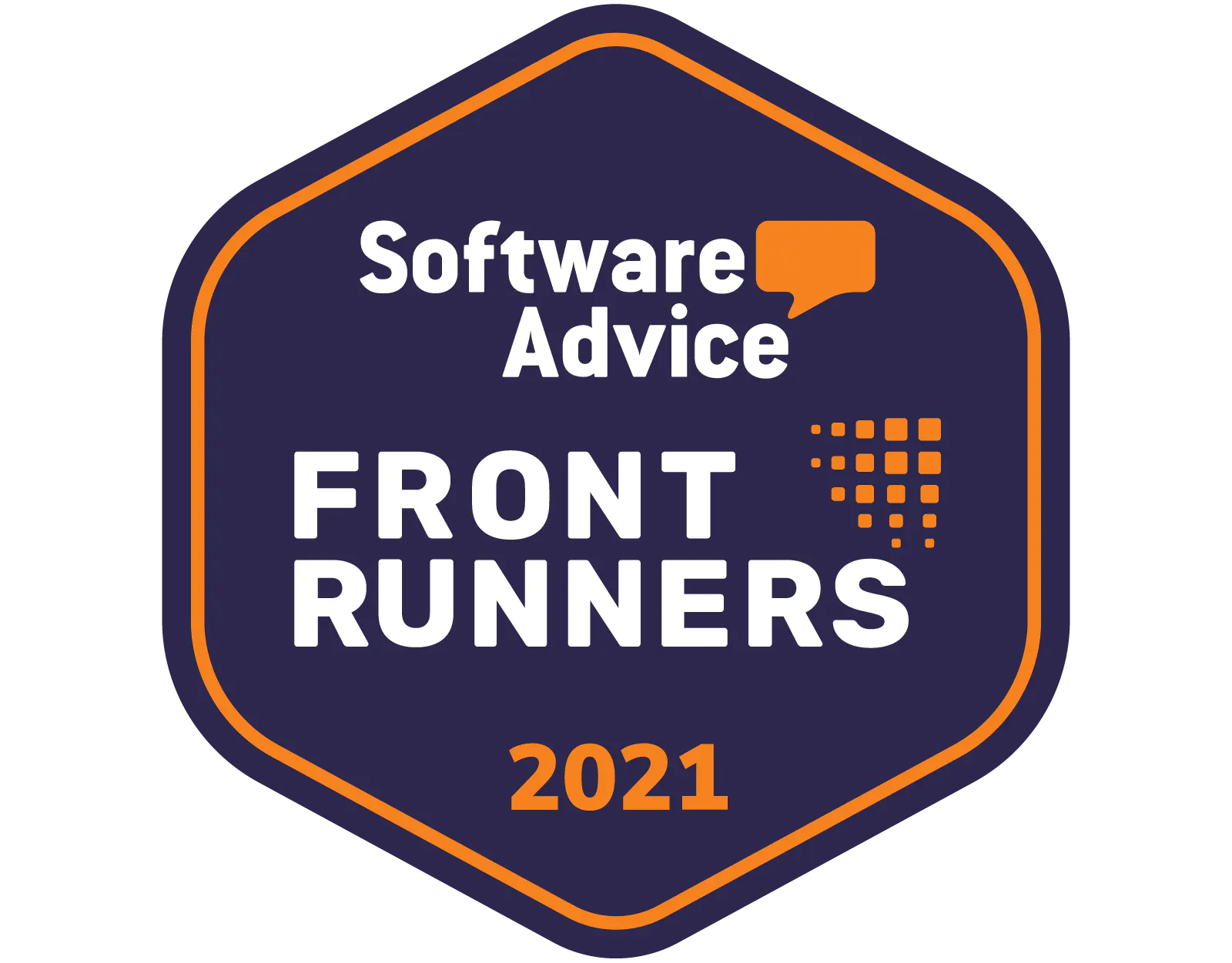