Assay testing company increases uptime to around 90%
A metal and mineral company performs assay testing on silver, gold, platinum, copper, and other types of ore from around the world. Companies send ore samples to be analyzed for precise material levels so that they can value and sell the ore. When the previous maintenance system needed to be renewed, the director researched other options and discovered UpKeep’s Operations Asset Management Platform.
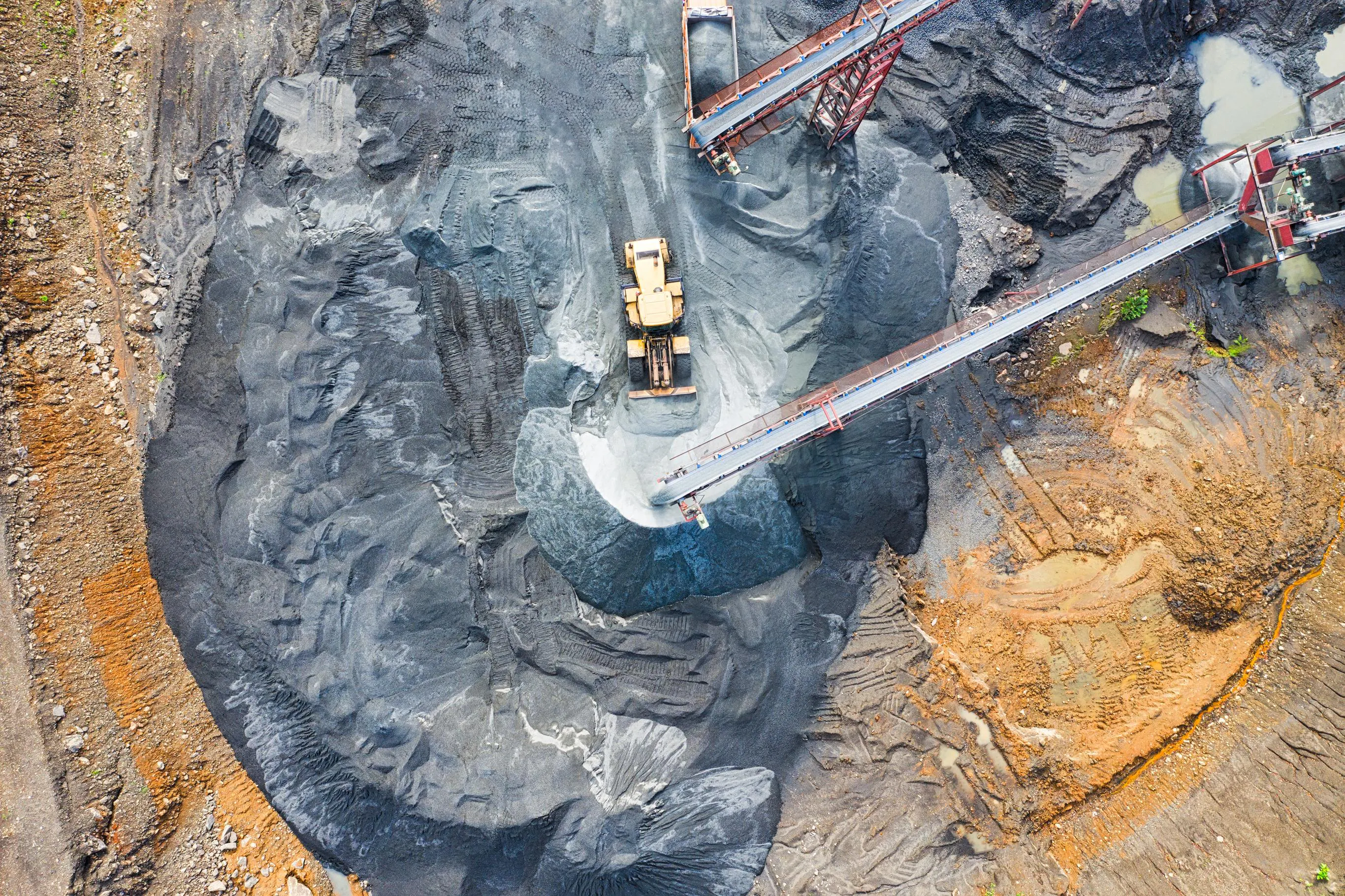
Challenge
The company used a CAFM system for years prior to UpKeep. It was expensive, and it was unable to analyze data, track work orders effectively, or store accessible data. The system had a mobile option, but the added expense meant it wasn’t worth it for the team.
Additionally, a completely separate system was used for tracking and purchasing inventory. Though the system effectively tracked inventory, the technician team had ongoing problems with stockouts. As a temporary solution, the team turned to offline spreadsheets and whiteboards to handle its work orders and inventory.
Solution
When a new director joined the company, he reviewed the maintenance situation. When the time came to renew the old maintenance package, he decided to research other maintenance solutions and found UpKeep. Although the director had little experience with software, he had no problem installing UpKeep, transferring data from the old system, and training his team.
Results
The team uses UpKeep for work orders, inventory, data storage, and tracking KPIs. For example, uptime had dropped as low as 60% in one area in the past; now, asset uptime is around 90% on average.
In addition, since implementing UpKeep, the team has been able to make more informed decisions about future needs based on growth expectations and current asset capacity. The team continues to notice interesting trends that may help increase overall efficiency. For instance, during COVID, the company added a third shift to implement social distancing. They realized that this solution eliminated bottlenecks and improved asset utilization efficiency by analyzing UpKeep data.
Ongoing Struggles With CAFM System
Before UpKeep, the team relied on a well-known CAFM system for its maintenance needs.
The company management renewed the licenses every year and kept using it, but the team got no real value out of it. For example, it wasn’t helping analyze data to help determine more cost-effective methods. As a result, it was costing money without reducing other costs.
Work orders often bypassed the system entirely. Since the system just couldn’t do an adequate job, the team ended up handwriting work orders on a whiteboard.
Data storage was also not up to par. The team wasn’t using the data in the system since it was difficult to even access the information. As a result, the technicians had to use offline spreadsheets to supplement the CAFM system. This spreadsheet system had its own problems, particularly data inaccuracy.
The team knew that a mobile option would solve many workflow inefficiencies. While the old system did have a mobile option, enabling it was expensive and it was clunky and old-fashioned.
Though the CAFM system was used widely, it wasn’t suited to the company’s production environment.
Looking For a New Option
The team has never felt supported by the previous software. Shortly after the strategy director started working with the company, the license had to be renewed. When he looked at the capability of the current license – the cost, renewal costs, mobile option, etc. – he decided that it was a good time to look at what else was on the market.
Early in 2019, the company began looking for a new software solution. The clock was ticking – the license for the old software had to be renewed in August. Some kind of system had to be implemented, whether it was UpKeep or the old system.
The team looked at three or four packages, and UpKeep seemed to be the most suitable.
Onboarding Process
The company started using UpKeep around June.
Though the team wasn’t completely sold on UpKeep at that point, the strategy director did a trial. Though he was not experienced with software, he found that UpKeep was easy to use. He was able to implement it, create workflows, and use all the functions.
The next step was management presentations to persuade the rest of the team that it was the way to go. The director took care of most of the implementation process as his division of the company is relatively small.
After downloading the relevant data out of the old system, the team filtered out much unnecessary data. The director also trained everyone on site – his colleagues, the lab people, and the maintenance people – with help from UpKeep people and YouTube videos.
Positive Team Response
Since extra training was needed in some areas, it was about six months before the team was using the system effectively and benefiting from it.
However, now that everyone is on board, the team is happy with UpKeep. Complaints are few and the team meets each morning to look at production assets and assign and sort tasks by priority.
All of the company’s maintenance is managed through UpKeep at this point. The rest of the faculty understand that if tasks aren’t put in UpKeep, they aren’t going to get done.
Personalizing Workflows
Though UpKeep has the capacity for complicated workflows and processes, the team chose to opt for simplicity as it’s what’s most beneficial for their particular location.
The director created the workflow they wanted using the tools UpKeep provides. The production people were able to provide input and make a few modifications, but the workflow is still very simple and functional.
Using UpKeep For Different Facets of Production
The plant uses UpKeep not only for production equipment, but also for air conditioning, effluent treatment, and maintenance.
Production equipment does the analyses and produces the results. The company stores and maintains hundreds of beakers, hot plates, bunsen burners, etc. But because those chemicals are in the facilities, air conditioning is also necessary to keep the temperature and humidity of processes in control.
When disposing of those chemicals at the end of the process, they have to be treated first by the team. Chemicals have to be removed from the water before it goes down into the local sewage plant. Another plant filters air before it’s released.
The majority of recurring tasks in UpKeep are related to these filtering processes and making sure that they’re performed properly. The technicians need to ensure that key things like air conditioning are properly taken care of. There are daily, weekly, monthly, quarterly, and annual lists in UpKeep and the analytics help the team know if they’re staying on track.
The team differentiates between production assets and unrelated maintenance jobs by creating a few generic assets in addition to the production assets. These generic assets contain small tasks that are clarified in the description. That way, if a light bulb goes out, the technicians don’t have to create an asset called “light bulb,” making the system much simpler.
Using Custom Analytics
To utilize custom analytics, the director decided to examine certain critical machines that perform nearly half of the business. Though the technicians run reports on these machines every month, they wanted to look at the whole. It revealed some interesting data.
Though the machines are performing the same job, the team found that machines in certain locations are doing much better than others. This observation has led to an interesting investigation.
UpKeep analytics has allowed the team to find this long-term trend that’s hard to notice day-to-day but could help improve processes drastically.
Tracking KPIs
With the old system, the team was unable to track KPIs. At this point, it doesn’t make sense for the team to use UpKeep’s full capacity. As a result, the technicians only use simple day-to-day KPIs, such as tracking asset uptime and downtime, comparing assets to others, and tracking costs and parts. They look at how the assets are performing over time and how much is spent on those assets. They also compare reactive to preventive work orders and look at whether they’re completing work orders on time. Finally, the team tracks monthly costs for parts in the furnace area.
They run monthly reports with that information. It works well for what they’re doing and helps highlight what they need to improve.
Predicting Future Needs
Before UpKeep, the team made purchase decisions based on an inaccurate offline spreadsheet. Now they’re basing their purchases on real data.
The team is using UpKeep to determine how much more equipment they need. As they worked on production planning for the next year, they realized that the business has been growing for about 10 years without fail, even during COVID.
With regular growth, the team has to continue to look forward. The company plans to grow by 10% each year. In five years, it should be 50% bigger, which drives many considerations.
UpKeep provides the director with the information he needs to determine the current capacity of current machines. He looks at the data, calculates how many assets they need based on their growth expectations, and buys what they actually need. UpKeep has helped him justify more capital equipment.
Spreading Work Shifts
Especially during the pandemic, the team was able to use UpKeep to understand machine availability. They used to have two work shifts that overlapped, but with the pandemic, they had to stretch their shift pattern to social distance.
When the team analyzed output using UpKeep, they realized that output improved during COVID. Nothing changed during that time apart from the shifts spreading out. They realized that they actually didn’t need the assets they were about to buy.
In another production area, a similar situation occurred. Two particular assets were a bottleneck point – many people needed them for different production labs. Simple observation made it clear that people were queuing up to use them.
However, the team wasn’t sophisticated enough to track when each production area needed those assets. Then COVID forced the faculty to spread shifts over a longer time period, and that effectively solved the bottleneck problems.
The company plans to grow by another 10% next year. They’re using that data to look at whether or not they actually need more assets, as a night shift might be a better alternative to purchasing more equipment.
Tracking Inventory Within UpKeep
The company uses a completely separate system to track and purchase parts. However, it wasn’t working well for this particular production unit. Though the tracking system was functional, it was letting them down regularly with stockouts.
For certain production lines, it doesn’t matter too much if something has been out of stock for a while. But for this area it’s critical that the team has parts when they need them – availability is key.
The team obtained permission from the company to use UpKeep for their division. It took some time for the team to transition to UpKeep, but it’s working well. They only track parts for critical equipment. The team also implements a second check to ensure that parts are arriving on time. Unless there’s a supplier issue, the team now rarely runs out of parts.
To solve the stock out problem, the team agreed on buffer times for different inventory items. For example, they keep two weeks of inventory onsite at all times for running parts and chemicals. Other items need a longer buffer time for different reasons. However, they’ve found a good medium at this point.
The team also tracks costs within UpKeep. Every month they can see how much they’re spending, how many parts they’ve bought, how many each lab needed, and how much they cost. The director summarizes that information each month.
All the inventory information is available on the dashboard for the entire team. At meetings, they look at order and inventory status. They can see if items are late coming in and whether or not they need to reorder parts.
Increasing Uptime
The team summarizes uptime on monthly reports. Over the past year, they’ve had periods when it was worse, but overall for the assets, it’s been in the high 80%, low 90%.
Before UpKeep the team didn’t track uptime. However, in one particular area, they were sometimes down to about 60% uptime. Now they can identify what is causing that, whether it’s stockouts, illness among technicians, or holidays. UpKeep gives the team answers.
Want to keep reading?
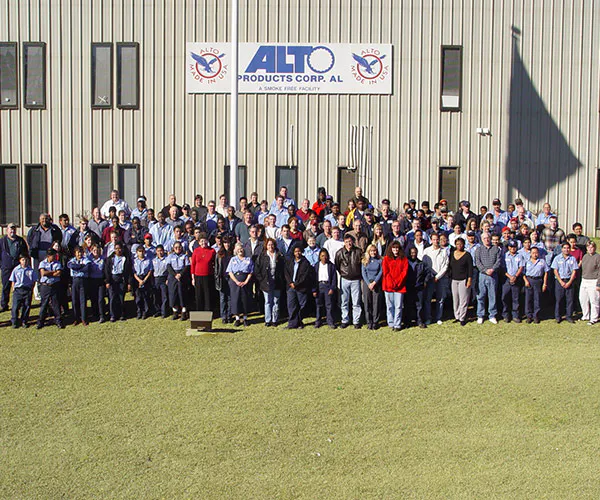
Equipment / Manufacturing
Alto Products moves from reactive to preventive maintenance
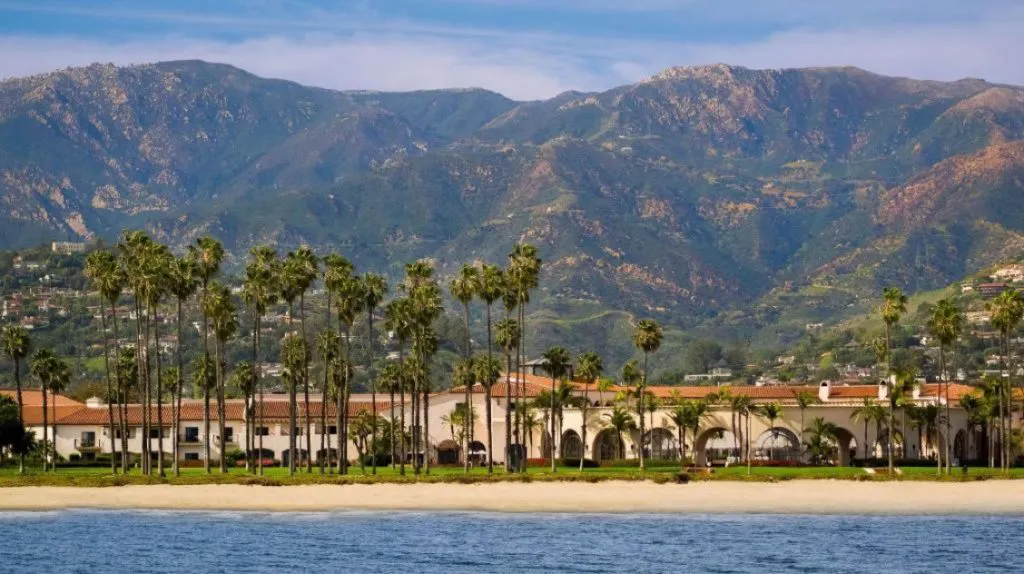
Equipment / Manufacturing
Innovative Micro Technology creates a safety-focused culture
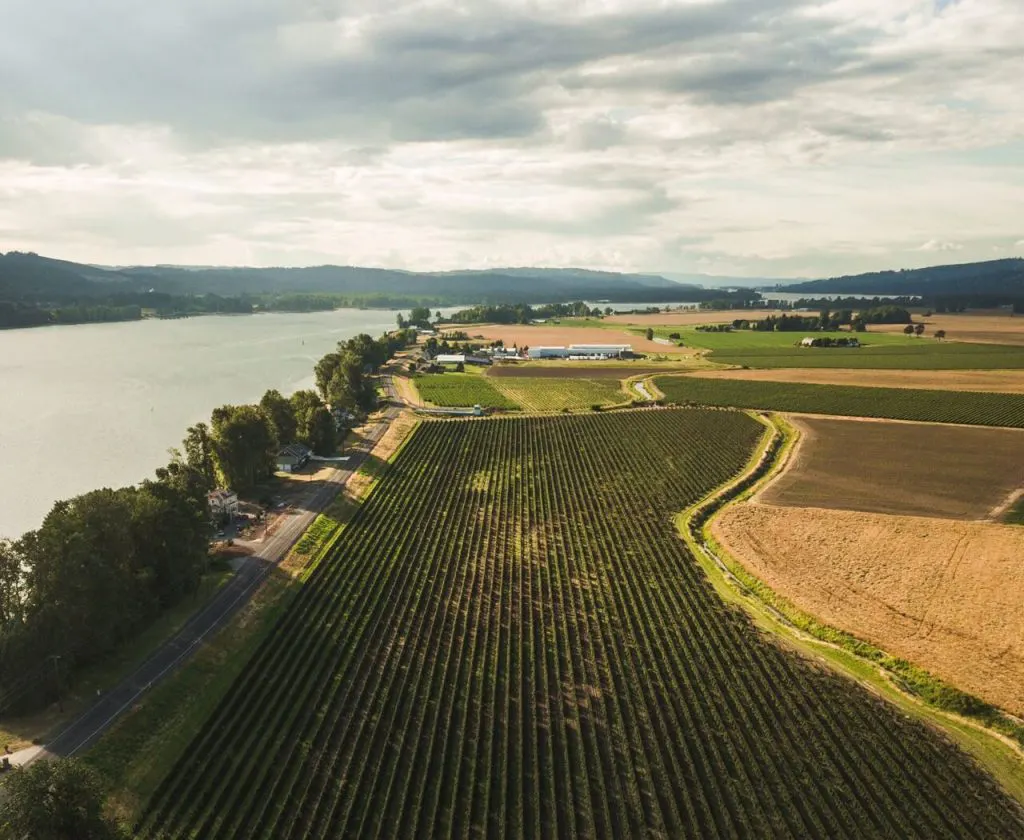
Equipment / Manufacturing
Columbia Fruit saves money with organized inventory
4,000+ COMPANIES RELY ON ASSET OPERATIONS MANAGEMENT
Leading the Way to a Better Future for Maintenance and Reliability
Your asset and equipment data doesn't belong in a silo. UpKeep makes it simple to see where everything stands, all in one place. That means less guesswork and more time to focus on what matters.
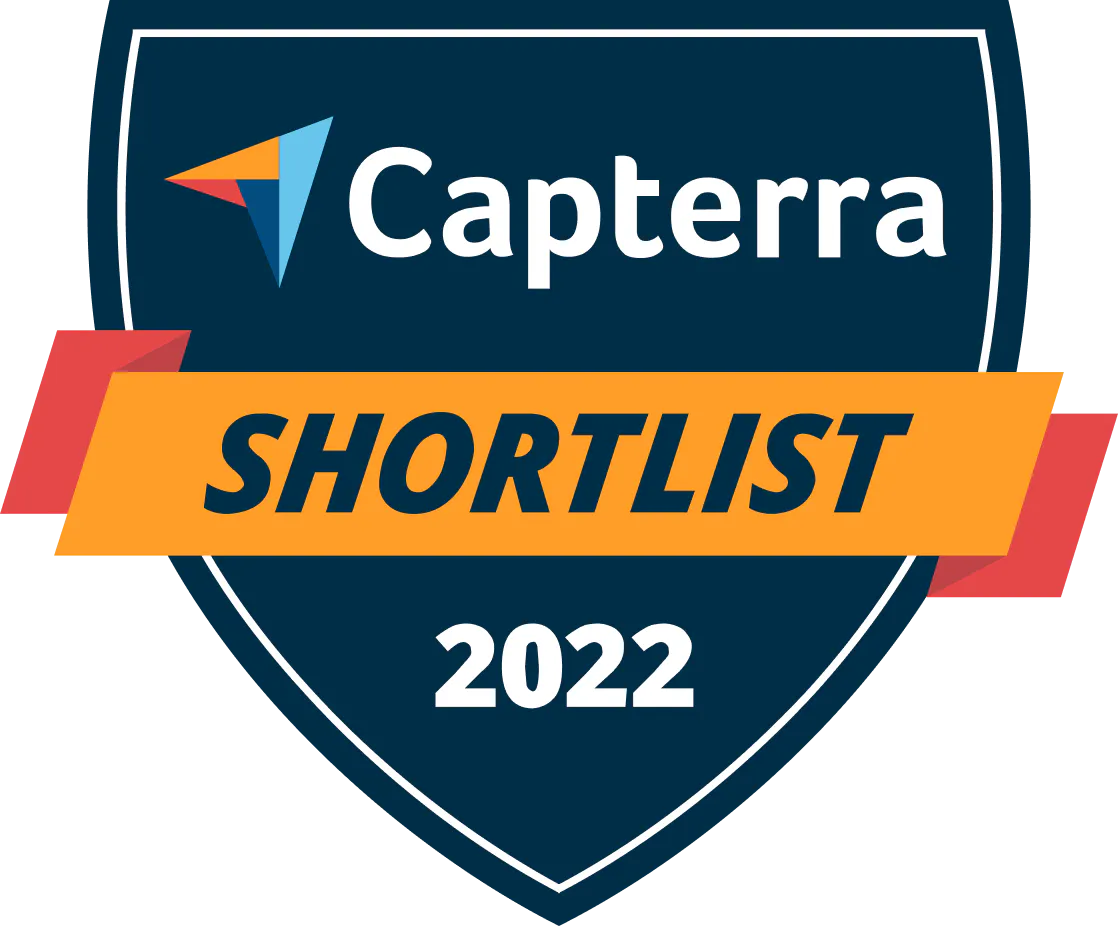

![[Review Badge] GetApp CMMS 2022 (Dark)](https://www.datocms-assets.com/38028/1673900459-get-app-logo-dark.png?auto=compress&fm=webp&w=347)
![[Review Badge] Gartner Peer Insights (Dark)](https://www.datocms-assets.com/38028/1673900494-gartner-logo-dark.png?auto=compress&fm=webp&w=336)
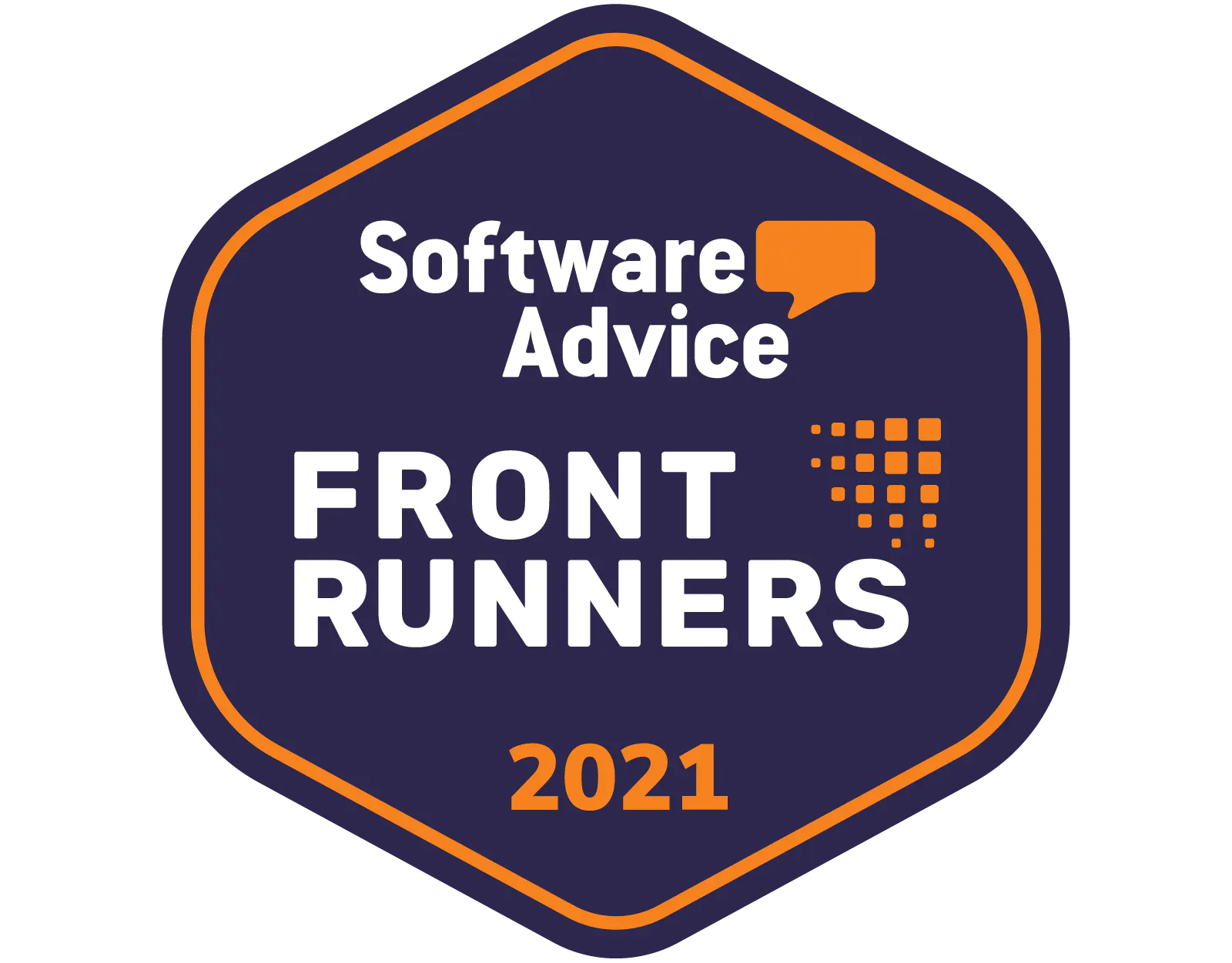