Webinar
How to Create Maintenance KPI Dashboards to Improve Performance
Duration: 36 minutes
Published on: June 04, 2024
In this webinar, Ricky Smith, CRMP will discuss KPI dashboards. Join the session to learn about leading vs. lagging KPIs, maintenance dashboard requirements and steps to creating the right metrics.
Brought to you by The Maintenance Community. Join here for more exclusive events.
Transcript
0:00:00.0 Speaker 1: Thank you. So today's presentation, How to Create Maintenance KPI Dashboard to Improve Performance. It's gonna be short and sweet. If you have questions after that, you'll be able to contact me via my email, which is [email protected], but I'll give that to you at the end. So, how do you create a... Well, first, we gotta understand what's a KPI. So a key performance indicator is a quantifiable measure used to evaluate success of an organization, employee, etcetera, and meeting objectives for performance. That's why they got performance in there. So, here's a KPI dashboard that I added a few SMRP metrics in it. So, a dashboard is a graphical representation using leading and lagging KPIs to share information on how a process is functioning. So, this could be your proactive maintenance process. To the left, we got PM compliance, 100%...
0:00:56.0 Speaker 2: Sorry to interrupt you, but you're not screen sharing, would you mind screen sharing?
0:01:02.1 Speaker 1: What? [chuckle]
0:01:03.9 Speaker 2: I just hear things on the left and I'm very curious to see.
0:01:12.2 S1: Oh, man. My bad.
0:01:16.7 S2: We got it. Perfect.
0:01:19.8 S1: Alright, I'll see what I gotta do here.
0:01:30.4 S2: It's showing the PDF now, if you wanted to go back to the PowerPoint for presentation mode, feel free.
0:01:40.5 S1: That will be helpful, wouldn't it? Okay.
0:01:48.3 S2: Thank you all for bearing with us. A whole new world of Zoom webinars and presentations, you will always see one thing.
0:01:55.4 S1: It's based in timing, they call it. So, KPI is a key performance indicator, is just a quantifiable measure used to evaluate success of any organization, employee, employees or any process to meet the objectives and performance. That's why performance indicator. So, a KPI dashboard, just a graphical illustration of using the leading and lagging KPIs to share information on how a process is functioning. And here on this one, I've got the PM compliance, 100%. Say SMRP metric, got breaks to the PM schedule. Important to know PDM, PM, yield, what's coming out of the PMs and PDMs. And that's SMRP metric. PM, PDM overdue, number of PMs evaluated. I wanna know that, I think it's important to have PMs evaluated, at least have some kind of target. I'm gonna target at least two PMs a week to be evaluated, it should be planned and scheduled for certain people to do that. Number of PMs optimized, emergency urgent labor hours, PM labor hours, PM costs, and then OEE.
0:03:08.4 S1: I think it's important to have a score card, otherwise you don't know the score in your game, and the game is proactive maintenance. Some famous quotes on measurements "If you cannot measure it, you cannot improve it." That was Lord Kelvin many, many, long years ago. Well, way before any of us were born. And, "A measurement is like laundry, it piles up the longer you wait to do it." I love this by Amber Nathan. And then, "You cannot manage what you do not measure." By Dr. Deming, and he is definitely truly a leader in that. So some other famous quotes, "Just because you can measure it doesn't mean you should." And that's a good point, that's a good point. "Without data, we're just another person with an opinion." Yeah, how true that is. So, requirements of good data, data must come from the same source consistently, data must be accurate. So, when we talk about data, how accurate is our data in maintenance and it's critical, it's critical to us. Data must be understood. Keep it simple. Data should tell a story. So, if our PM compliance is 100%, but emergency, urgent labor hours are going up and down, maybe it's telling us something. Metrics dashboards are critical to empowering people to do the right thing consistently.
0:04:39.6 S1: When I was a maintenance manager, I always had this... I had a dashboard out, it wasn't this one, but it was one similar, and I always had it out what the score in the game was, so my people knew how we're doing. Always successful, it's like if you play football or soccer or whatever, we all look, yeah, we watch the game, but we like to see the score in the game too. And this is what we gotta do in maintenance and reliability, you have to know the score in the game. So, what is a maintenance KPI dashboard? A maintenance KPI dashboard shows how the processes of maintenance of function in an organization, the example below is from the rules of thumb from maintenance and reliability engineers. So we have leading indicators, come from work identification, work planning, work scheduling, work execution, follow-up and performance analysis.
0:05:36.6 S1: So, all of these impact the lagging indicator. Okay, the lagging indicator is the number of functional failures total and then subtotal by fair consequence, hidden, safety, environmental, operational and so on. And then maintenance related to downtown, unscheduled and scheduled and shut down overrun and a maintenance cost. And there's other ones too. Our benchmarks, we look at our benchmarks, maintenance cost per unit output, maintenance costs as a percentage of replacement asset value, total maintenance cost as a percentage of total maintenance cost, and total maintenance cost as a percent of total sales. These are probably at a very high level, that's why I like the ones at the bottom first, 'cause these are the ones we manage, we can't manage these other ones, we can manage these, but what influenced the other ones.
0:06:29.9 S1: Leading KPIs lead to the results, and lagging KPIs are the results. And if you look at this one, this graphic I have here, you got leading KPIs like PM effectiveness versus emergency versus PM labor hours, PDM compliant route adherence or compliance, percent of planned work, and then rework percent. What percent of our work is rework. And then our lagging KPI here is MTBF. Ron Thomas, great guy, he had one of the Tabasco Steel on Hamilton, Ontario many years ago, was the leader in the world in maintenance and reliability. He made this statement, "A proactive reliability process is the supply chain, if a step in the process is skipped or performed at a substandard level, the process creates defect known as failures. The output of healthy reliability process is optimal asset reliability at optimal costs." I love it. That's exactly, exactly what it is. So KPI dashboards provide alignment and allows everyone to focus on the right things in order to achieve a desired outcome.
0:07:48.6 S1: You notice I got these rollers here, they all look in the same way, they're all focused on the same objective. And that's what we're trying to do. We're trying to get alignment with everyone. And sometimes that's very difficult. But if you have the right dashboards, people will fall in place, they will follow you. It's like watching any game soccer, football, rugby, whatever you'd like to watch, the score in a game is important for success. The fans get fired up, but also the people that are participating get fired up. There are a lot of times I've seen games played, different type functions and like a football game and in the last minute, one team that's down all of a sudden now beats the other team and wins, that can happen. That's why we gotta know our score in the game. So, let's talk about one type of measurement performance metric. Performance measurement is a fundamental principle of management. The measurement of performance is important because it identifies current performance gaps between current and desired performance and provides an indication of progress as we move towards closing that gap. It's important.
0:09:01.2 S1: We must carefully select key performance indicators that identify precisely where to take action to improve performance. And let's get... I'll give you an example. So, if one of our KPIs was our emergency labor hours, let's just say I like to know what that is, it's just a thing to me. 'Cause it tells me a lot. But, so what would I... Action would I take there, if I got emergency labor hour, maybe I need to look at my preventive maintenance program, maybe my PM program is not effective. So, now I can improve my PM program, I can improve performance overall. So, PM compliance but also my emergency labor hours are important to me. Requirements of a dashboard identified a need or desire to measure maintenance processes in order to optimize asset reliability at optimal cost. Identify the steps in the maintenance process from PM, PDM, all the way through the fracas.
0:10:00.9 S1: So, you see here steps in this process, PM, PDM, work identification, planning, scheduling, work execution, work order close out, and failure reporting. So here are our metrics that we use with this, we get PM, PDM compliance, we get number of tasks identified by PM and PDM, we get percentage of planned work, schedule compliance, number of reworks. So, how often we have to go back to previously maintain equipment that we did something to and then number of work orders closed accurately. And how do you do that one? Typically, is the planner that goes back in and randomly just pulls X amount of work orders and looks out, are they closed accurately or not. And then the last one, lagging indicator, rework and costs. So, identify the metric they use in each step and post the maintenance dashboard for specific audiences. You wanna give people the score that they need to know for who they are.
0:10:56.5 S1: Because if we talk to SSA plant leadership, about PM compliance or planning the scheduling, that doesn't impact them as much as when we talk about costs, that's what they care about is cost. And that's why we need to have a dashboard just specifically for them. Are we using their money or the company's money, organization's money effectively. So, specific audiences, technicians, planners, whoever they are, we need to focus on those dashboards for those types of individuals, even store managers. So, earlier requirements, number five, maintenance dashboard should be posted where everybody can see it. I like to have them up front, like the plant dashboard should be when you come to the plant, walk into the plant, there ought to be a scorecard right there, everybody can see it. Don't put it outside to play it, 'cause your competition may see it, but put it in the plant where everybody can see it. When I go in the maintenance shop I wanna see a maintenance dashboard like this. What's our score in the game.
0:12:01.3 S1: Maintenance score dashboards should tell a story good or bad, people want to know their score in the game, absolutely. Data must be accurate and come from a reliable source example, close out work orders. Now, who closes out a work order? I've been asked this many times. Well, because the data is so important, I want the maintenance supervisor to review the work orders before they close. But the last person to close them I want is the maintenance planner. Why? Because they're sitting calm in an office. They're not out with what I call it, their hair's on fire, they're out there running around trying to solve problems, "Hey, we gotta get this machine going. We gotta get this going." I don't want them to have to do that and sit there and say "Okay, these workloads gotta be closed but I don't have time to do it." That's okay. Review them and let the planner handle it. Because once it goes into the CMMS you can't extract it and change it. It's there. It will tell, it will give you metrics good or bad.
0:13:01.6 S1: So, establishing some goals, these are important. So, store room service level, 95%. That means 95% of the time that someone goes to the store room to check the part out, the system says it's in there but 95% of the time it is there, okay? Vendor performance, I like this one a lot. On-time delivery, I wanna measure my vendors, probably none of you have problems with vendors delivering on time. I did, that's why this one is important to me. Material part performance is the next one on there, you see that, and then materials delivered to the job site. I want also the stores turns, how often does this part turn. If it's not an insurance spare, I need to know that, and I think most of people agree with that. We need to know how often that part's turning, 'cause if it's not turning, why is it not turning? Why is it sitting on the shelf? Why do I have 47 of these items on the shelf and we haven't checked one out in three years, something's wrong. So, steps to creating the right metrics; assemble a team of stakeholders, influential stakeholders like two maintenance techs, one with the worst attitude and one with the best attitude. That's what I like. Okay?
0:14:17.4 S1: Maintenance supervisor, stores manager, maintenance reliability engineer, notice the maintenance manager is not in there because he should have confidence that these people could make those decisions. Create a vision and mission statement for metrics. An example, vision statement to provide visibility score cards for the maintenance process, that's what I wanna know. Mission statement example, we will manage our maintenance department with accurate leading and lagging KPIs or metrics. Leading KPI leads to the lagging KPIs, so leads to results, lagging KPIs are the result. Establish goals and targets, you're not gonna go from zero to hero overnight, that's why we have to have targets to help us gradually move up to our goal. Identify leading and lagging KPIs for all maintenance processes, from preventive maintenance to failure reporting, we need to identify for each one. And then what we wanna do is we wanna create consistent definitions and measurements for metrics. You should have... That's why I like SMRP. Okay, SMRP has a metrics manual. What's nice about it is, it has a definition, it has how to measure it and has the other things in there, and it really helps when you give your maintenance people when they say, "How do we measure PM compliance? How do we get that number?" "Here look in the book" Or, "Look it up on our software here, you can find it."
0:15:49.0 S1: People need to know that. So examples of a proactive maintenance process, we have PM and PDM, we have plans, so what metrics do we use there? Could be PM, PDM compliance, planning for center plan work, scheduling, schedule compliance, work execution. So work execution, what percentage was done? When you think about work execution, if you think about how do I measure work execution? Maybe there's a metric called re-work, meaning we have to go back to that equipment again. Maybe we didn't troubleshoot it right, or maybe we didn't install a part right, something there, re-work is important to know. Work order close out, very critical, 'cause without good data, we don't have good metrics. And I mentioned that earlier, and then there's failure reporting, analysis and corrective action system. If you have reliability engineers, they gotta have good data, they have to have accurate data, and this is just a continuous improvement loop. So, as we have failures, we can improve our PM and PDM Program, and Dr. Deming said, "Your system is perfectly designed to give you the results you're getting." And it's absolutely true. Look at this electric motors, these are all electric motors in one plant, so this is the average, the mean time between failure.
0:17:10.6 S1: You notice it was kind of... The mean time between failure was low, and then something happened, an intervention happened, and then it started to get much better. And I'm not gonna get into what the intervention is but they made some serious impact on it. World class standards, just focused in on that. Where are you? PM execution should be 15% of labor hours, PM result should be 15% of labor hours. In other words, PM execution, we execute it and then the results from it should be 15% of labor hours. PDM execution, 15% of labor hours. Look at this, PDM results, 35% of labor hours. Now yours could be different, I just like to measure it, 'cause it tells me something. It tells me a story and that's what metrics should do, tell you a story. Total percent of plan work, 90%, reactive work, less than 2% of labor hours, stock counts less than 2%, and then schedule compliance by day by week, 85-90%. These are just world class standards that came from Alcoa Mt. Holly where I worked many years ago. Failure elimination is the key focus for all, we all focus on eliminating failures every day. That way, we're focused on it, we wanna mitigate failures, we wanna eliminate failures as much as we can.
0:18:34.0 S1: All work orders are closed out with all codes identified, we want all the information in CMMS to give us the right data. So, here we talk about measure what you manage, look at maintenance cost, world class is the dark color, then the medium brown, I guess you could call it that, is typical then worst in class. So, you got world class and worst class. So, in maintenance cost, world class maintenance cost is low, overtime is low, production delays are low, production output is high. Then we look at worst in class; maintenance cost is high, overtime cost is high, production delays are high, production output is low. It's a fact.
0:19:18.4 S1: Differences on measurements. How much does your maintenance and reliability process impact cost, output and quality? There are some differences there. Known best practice, financial data, best of the best, maintenance cost as a percentage of replacement asset value, 1.3%. Worst of the worst, 17.1% of the replacement asset value, I'm not mentioning any names, okay? So, if we look at this chart, this gives you not just the maintenance cost, but we also, we could look across at stores replacement asset value, this comes from allied reliability, stores as the percentage of replacement asset value. What percentage of assets are typically on vibration routes? Percentage of IR mechanical, percentage of IR electrical, percentage of all analysis and so on. And then percentage on PMs and then percent of bill of materials. I love this chart. So, defining the requirements to meet the end goal, first, we start with production. What's their requirement?
0:20:21.1 S1: Anything we do, it starts with the end game, the end game is production, okay? So equipment requires to be identified by management, we want rate, we're gonna measure rate, pressure, OEE, availability, throughput and cost. And as we move up reliability engineer ensure all asset reliability meets full functional requirements. And then, maintenance, we wanna maintain equipment to specifications with repeatable procedures. I've been teaching a class this week on maintenance technician, and one thing they said today was about the specifications. They had never really thought about it, and repeatable procedures, how critical they were to the success of an organization. Without it, you have everybody's opinion. Capacity assurance team, maintenance cost, there's replacement of asset value, production, you know what's their rate and we want the customers, our customer really is production, and we wanna satisfy them.
0:21:21.9 S1: And this capacity on demand, this was coined by John Day, who was the creator of World Class Maintenance in Alcoa Mt. Holly. And this is, we wanna satisfy the stockholders, who owns the company, we wanna make them as rich as we can and as happy as we can, 'cause now I get to keep my job. Okay? And then the requirements of the customer it goes all the way back, start over again, we gotta meet the requirements of it. Creating score cards that provide us with a score, I like having dashboards on a screen saver, you can have them up on a big screen in your maintenance shop, you need to get people to score in the game and people need to see it. So, here we got wrench time for the crane crew, this is one created a long time ago, know we're in an amber right there. A percentage of planned work by the crane crew at about 50, then schedule compliance was about 90%. Now it looked pretty good. Alright. So what are your questions?
0:22:26.6 S2: Alright, we have one. So, just a reminder for everyone, if you wanna use the chat function to add any questions you have, I'll read them out for you for Ricky.
0:22:37.2 S1: And by the way, this, my next class coming up is Maintenance Planning and Scheduling, and UpKeep will be hosting this on virtual on Zoom, if you're interested in it. I did not put my email address on there.
0:22:49.9 S2: Do we put it in the chat?
0:22:53.5 S1: Yes, I'll do that.
0:22:55.7 S2: Excellent, alright. We have a question, how do you use a matrix to implement and control leading and lagging indicators for processes, so that we are getting good results in a JPI dashboard?
0:23:11.1 S1: Read that again.
0:23:14.4 S2: Okay. How do you use a matrix to implement and control leading and lagging indicators... Oops, sorry, we're just getting a lot of notes... Leading and lagging indicators, so we can get good results in a JPI dashboard?
0:23:34.2 S1: The matrix. Hmm, I'm not sure what you're meaning by matrix unless you're talking about this here. Is this what you're talking about? Tell us.
0:23:44.9 S2: Sarah, let us know if this is what you're referring to and we'll be happy to answer your question. Ronald asks, what are the differences between the leading KPI and lagging KPI? What's an example of them?
0:24:00.2 S1: Okay, an example of it. Let's just think, what are your expectations of preventive maintenance, what do you expect to come out of preventive maintenance? So if we have PM compliance, what do you expect, if we got a 100% PM compliant, what metrics would it impact? My personal opinion, what it impact is cost. That's the big one. It impact OEE, and that types of thing. So, leading lagging. I'll give you a better one. Let's say schedule compliance is low, so what do you expect if schedule compliance is low, what do you think the impact is? It impacts OEE, because you're not... Evidently, the equipment is breaking down and you can't get to it, or they're not allowing you to get the schedule, it's important.
0:25:00.0 S2: Excellent. And so, the initial question asker was referring to the slide you were on.
0:25:05.7 S1: Say that again?
0:25:09.5 S2: The first question that I asked you when we were wondering which slide he was referring to, it was the slide you guessed.
0:25:17.5 S1: Okay, this one?
0:25:22.9 S2: It was like a matrix.
0:25:25.2 S1: This one, yeah. Yeah, so this slide here, they come from different organizations trying to compile this information, but maintenance cost we know in a proactive organization is low. Over time, it's typically low. People have life outside of work and I know, hey, I used to be a maintenance technician, I loved over-time, I made a lot of money, so how I bought a few cars okay? And maybe even a nice house one time, okay? The over-time is low, production delays are low, production output is high, this is what you see every time. That makes sense? 'Cause if the maintenance cost is high, overtime cost is high, production delays are high and production output is low. Alright, what else?
0:26:16.8 S2: Do we have any more questions from the group? I think you were so thorough no one had any follow-up questions.
0:26:24.5 S1: Wow. [chuckle] Let me ask a question.
0:26:32.0 S2: Great.
0:26:34.9 S1: So, is it... Let me ask the group. Does anybody complain about maintenance costs as far as management that you work for?
0:26:50.3 S2: Darren says, "No," but Sahar says, "Yes." And Duncan says, "Our management loves costs."
0:26:58.5 S1: Duncan says, "Our management loves costs." [chuckle] No one arguing. Okay. Yeah, I'll tell you costs... We gotta think about who owns the organization, who owns the company. Whether stockholders or some very wealthy person, whatever, it doesn't matter to me. I always say when you go to work for a company, you try to leave your flag at that company and you do the best you can, 'cause you wanna make as much money as they can, so I keep my job and hopefully I get a good raise every year because the company is doing well. The difference between first place and last place, you know, as far as cost is about that much. We can make a very serious impact if we all focused on the right metrics. Alright, what else? "Bottom line is, fix it right, it'll last longer." Yeah. "Do most companies work with hour-based PMs or calendar-based PMs?" Most of them are calendar-based, my personal... Maintenance supervisor, maintenance manager, I like doing it by hour by day, so the PMs were done on time. But most of the time... But I'd say 98% of the company or 99% of the companies that I've worked with over the years, it's based on day, not based on hours, so it's calendar-based. Monthly, yes. A lot of them are monthly, some are yearly, some of them quarterly, it all depends on the failure mode we're focused on. Anybody else?
0:28:32.5 S1: "Has any KPIs... Any different KPIs that we're doing predictive compared to the proactive strategy... Compared with proactive strategy?" It's the work... I mean... If we look at the work that comes from PM or PDM, more work should come from predictive maintenance than preventive maintenance. Preventive maintenance is to prevent failure but the predictive maintenance should be identifying defects far enough in advance so we can plan it and schedule it before it impacts production. To Ricky, "Measure paragraph world class is not showing 100% or around 90%, only 20% plus, please explain." Okay. Okay, that's the one you're talking about. So, if we look at world class maintenance, maintenance cost is low, if you see that dark line, the most dark line, maintenance cost is low. Okay, that's world class. The world-class is a dark color. If we look at production output, output is high. So, when we look at over time cost, we got maintenance cost is low, but now you can't get... You can't drive down your cost of maintenance without investing into it. A lot of companies try to cut their way to maintenance cost. Maintenance cost is a cost, you can hide it where you wanna hide it, but maintenance cost is maintenance cost. And I think you're in agreement, labor, materials, those type things, that has to do with our cost. Okay, did I answer your question? Yes.
0:30:26.3 S1: Okay. "Any metrics that can feed maintenance problems back to design engineers?" That's a good question. That's a tough one, that's a tough one. Because when you're looking at metrics that feed back problems to design engineers, if they don't measure things the right way, that's the critical part for design or even reliability, maintenance engineers, having good data. You gotta have good information, you gotta have good matrix that feeds back and tells what those problems are. I think that's critical. "What are some good KPIs to track regarding a network, not just a local facility?" When you talk about regarding a network, you gotta think of the processes, I'll go back to my slides. So, you have some type of process to managing a network, it may not be this process, but you have a step-by-step in that process on how you manage it. You need to find that, and in each part of those steps and that process, you need to know... You could either identify, how am I gonna measure it, the impact of it? How am I gonna measure, is it performing what I want it to do, and what should be my goal on that metric? Okay. And that makes it... It makes it much simpler. It's not complicated once you break it out that way. "Is there a Certificate of attendance?"
0:32:02.4 S2: Yes, there is. It will be DM'ed to you in the maintenance community if you are a Slack member.
0:32:09.1 S1: Are you gonna send me one too?
0:32:11.8 S2: Yeah, for every webinar you host, I send you one for attending.
0:32:15.6 S1: I know, I know.
0:32:16.6 S2: I think I have the most Ricky's webinar attending certificates out of everyone. [chuckle]
0:32:24.0 S1: Anybody else have any questions? If you'd like to email me, my email address... I'll go to the last page. Yeah, that's not on there, [email protected]. I'll type it in really quick.
0:32:42.2 S2: You did, it's in the chat.
0:32:44.6 S1: Oh, you got it in the chat, that's right.
0:32:45.8 S2: Yes. He's also a member of the maintenance community Slack.
0:32:49.1 S1: Okay. So, Maintenance Planning and Scheduling. My workshop coming up, it'll be mainly virtual, January 19th to 21, 9:00 AM in the morning to 4:00 PM in the afternoon. So anyway, I hope you have a great evening. Thank you very much for attending. We got more chat?
0:33:08.6 S2: One more question. Do pre-PMs work?
0:33:11.7 S1: Pre-PMs?
0:33:14.3 S2: Pre-PMs.
0:33:16.6 S1: I don't know. Define what a pre-PM is.
0:33:20.1 S2: Andre, what would you say a pre-PM is?
0:33:26.7 S1: I think I know what he's talking about.
0:33:28.4 S2: While he's typing, we have one more question that snuck in. Which can be one thing you say is the most important factor for these dashboards?
0:33:38.3 S1: For dashboard, having the right data, and that means when work orders are closed, someone verifies the data is accurate before it goes into the CMMS. 'Cause bad data in gives you bad information out.
0:34:00.6 S2: Okay, Andre clarified. For a pre-PM, a runner will go check the machine over before it actually comes in for a PM.
0:34:10.2 S1: Yeah, yeah. Yeah, that's a pre-check, if you like it's best if you've got mobile equipment, you do pre-checks, but I used to have what I call a line... I'm glad you brought it up Andre, but I actually had a line running PMs. So, if two days from now we have a PM due, my maintenance techs were assigned to go out and do a line running PM of all the lines. So, they walk down the lines and typically it's done first thing in the morning just to give checks. Is everything okay, any problems that you see or anything else, and then they go do their other jobs. So, it was just a line running PM, so I like that idea, and it does work, it worked for me very well. Especially if you have problems, and I had a lot of problems. "Which metrics are important to measure if you're in full reactive environment?" [chuckle] Well, I think you look at labor hours, labor hours along with people.
0:35:11.8 S1: The thing is, even if you're reactive to labor hours, make sure you get your work orders are coded the right way. So what is emergency? And you may wanna say, what's urgent? 'Cause there's a different between emergency and urgent. You can break those into two categories and make that a category and others. How much am I putting at preventive maintenance? How much am I planning? How much am I scheduling? Even though the numbers don't look good, let's start measuring the right things in a reactive environment, and that way as we move forward, we can see the changes that are occurring. But you won't do that without having processes in place, and without having someone to make sure the data is going in and those work orders are closed out, are going in the right fields. And that's the maintenance plan, have to do that. Alright, is that all? Alright.
0:36:05.7 S2: Thank you all so much.
0:36:07.8 S1: Join me on Maintenance Planning and Scheduling, next month. Alright, and then this week, what have we got coming up again, Caitlyn this week?
0:36:18.2 S2: For your next webinar?
0:36:19.5 S1: No, I'm talking about UpKeep, what have we got? With Ramesh Galati and me, what's it gonna be?
0:36:29.5 S2: That's right. It's gonna be on Saturday, December 12th, at 12:30 PM Eastern, Ricky and Ramesh will be doing Predictions and Reflections on Maintenance. Please join us.
0:36:45.3 S1: Alright, thank you very much. Goodbye.
Explore More Events
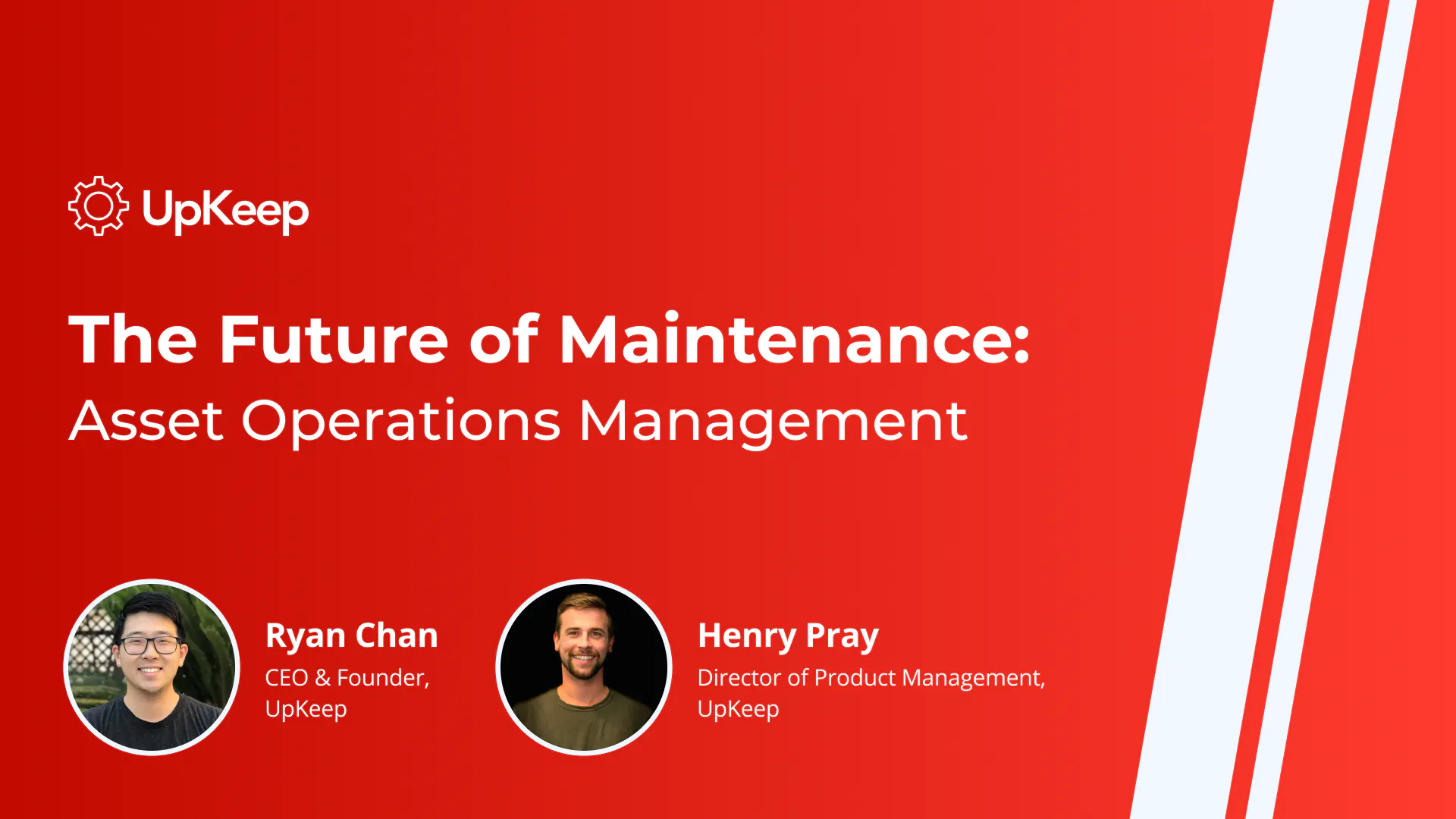
Event
The Future of Maintenance: Asset Operations Management
Watch UpKeep CEO and Founder, Ryan Chan and Henry Pray, Director of Product Management, for “The Future of Maintenance: Asset Operations Management''
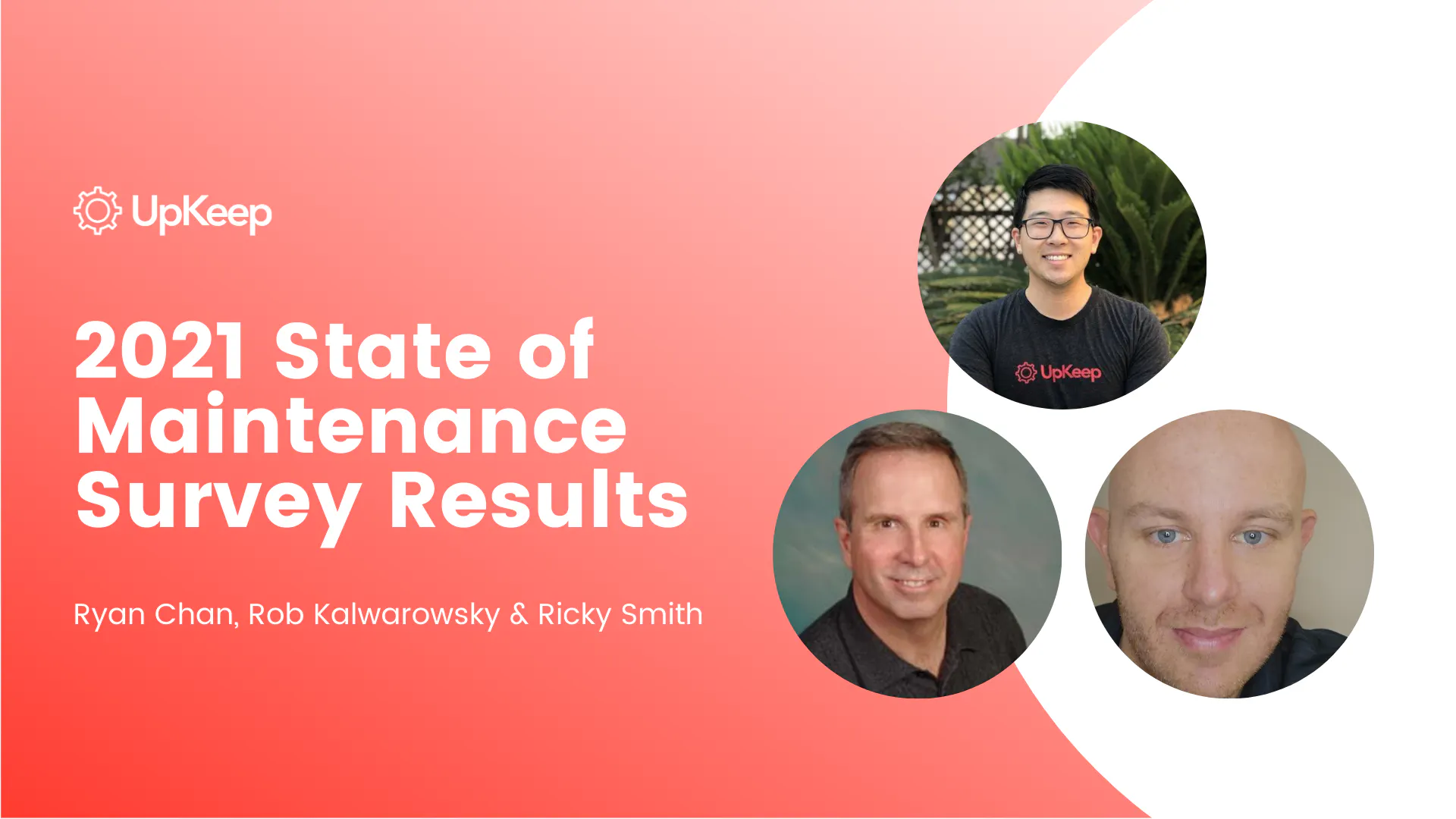
Event
2021 State of Maintenance Survey Results
Watch the panel discussion between experts from the maintenance and facilities industries on the top trends from the State of Maintenance 2021 report.
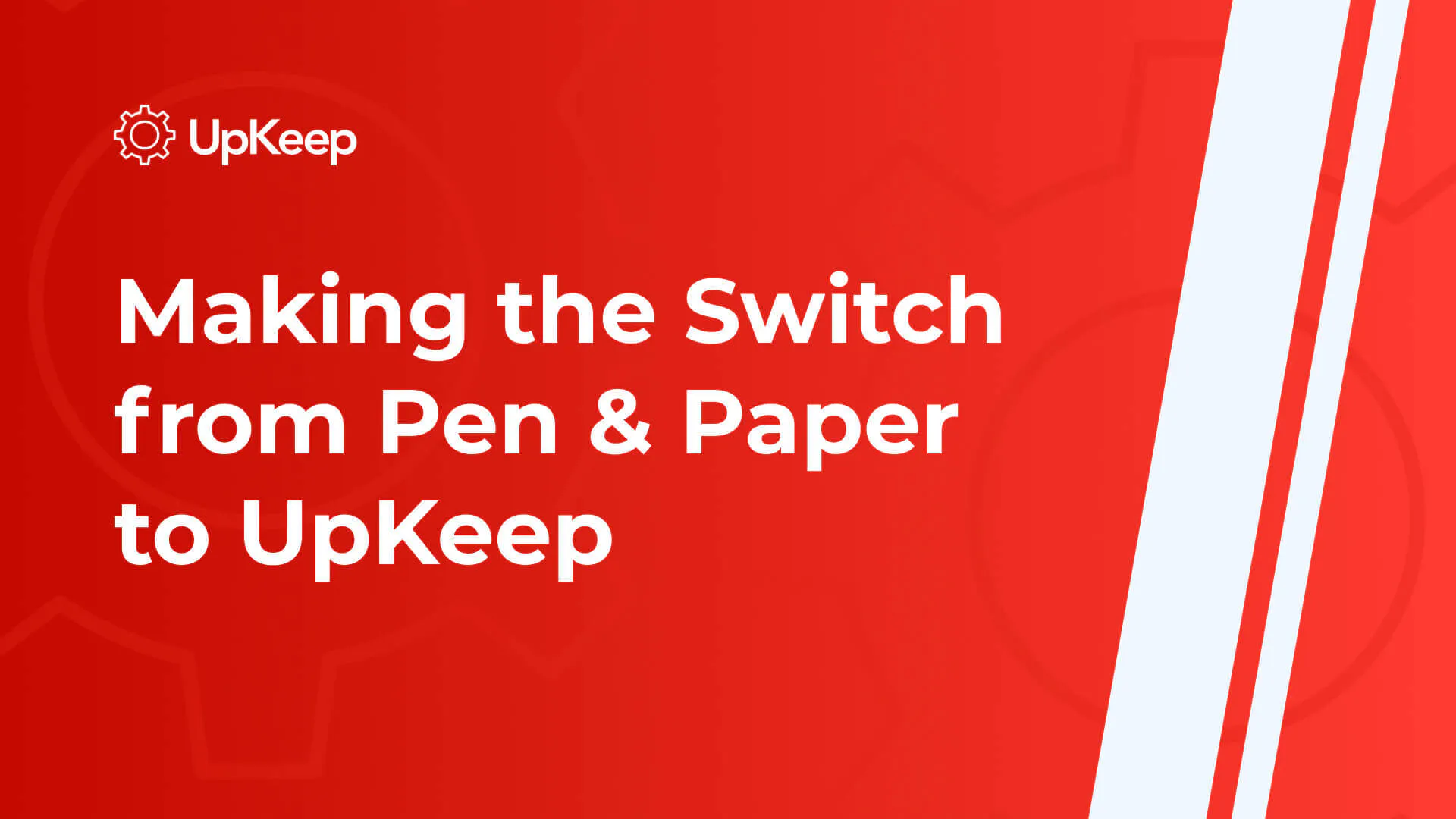
Event
Making the Switch from Pen and Paper to UpKeep
For most organizations, managing maintenance with pen and paper or spreadsheets works until it doesn't. Fortunately, there’s a better way.