Webinar
How to Conduct a Preventive Maintenance Optimization, Step by Step
Duration: 67 minutes
Published on: June 03, 2024
In this webinar, Ricky Smith, CRMP will discuss how to optimize your organizations' preventive maintenance. Join the session to learn preventive maintenance best practices, how to choose the right KPIs, and a step-by-step guide to optimizing preventive maintenance.
Brought to you by The Maintenance Community. Join here for more exclusive events.
Transcript
0:00:55.3 Heather Grant: Hi, Ricky.
0:00:55.4 Ricky Smith: How are you?
0:01:00.0 HG: Good. How are you doing?
0:01:00.6 RS: Good.
0:01:01.1 HG: Good. I can see your screen, all set.
0:01:06.4 RS: That's good.
0:01:07.6 HG: Yeah. How's your week going so far?
0:01:11.9 RS: Going good.
0:01:12.4 HG: Good.
0:01:14.6 RS: How about you? Crazy?
0:01:16.4 HG: Yeah. You know. [chuckle]
0:01:19.4 RS: I'm trying to do two jobs. Yeah.
0:01:22.0 HG: Yeah, exactly. Definitely pretty crazy around here. But we're getting the hang of it, we're getting back into a routine, all of that.
0:01:30.0 RS: Yeah.
0:01:30.4 HG: Yeah. Seems like we got a lot of momentum for next week, huh?
0:01:37.0 RS: Yeah.
0:01:38.0 HG: Good.
0:01:38.3 RS: Got one person wanting me do some training that want my bank information and all that, I gotta take care of that. That's another class, that's a private class.
0:01:49.3 HG: Oh, cool. Well, let me know if I can help.
0:01:51.8 RS: I will. You know I will.
0:01:54.2 HG: I know you will. I also just sent you another form that someone was asking for, it's a little bit confusing, but if you could take a look at that today as well.
0:02:02.8 RS: Okay.
0:02:03.6 HG: We'll figure that one out. Hello, and welcome to everyone listening to me and Ricky chat. We have a couple of people joining us already, we'll get started with our webinar in just about five minutes. Cool. Did you do anything exciting over the weekend?
0:02:26.7 HG: Awesome. We have a couple more people joining in now. Ricky, I see you never go anywhere without your virtual background these days.
0:03:28.7 RS: Yeah.
0:03:32.5 HG: Love it. Alright. Hello, and welcome everyone. Alright. Everyone just joining, we'll get started in just about three or four more minutes. Just hanging out until then.
0:06:01.6 HG: Alright, welcome to everyone just joining. Hope you're having a great Tuesday. We will get started in just a few more minutes, again, just hanging out for a few more minutes while people trickle in. Glad to have all of you here so far and we'll get started soon.
0:06:19.7 RS: I wanna say before we get started, Jeff, hey buddy. Congratulations on the new position. Proud of you man. I knew you'd bounce right in there. You did great.
0:06:30.8 S3: Awesome.
0:06:35.0 HG: Congratulations.
0:06:36.3 S3: Yeah, it's on. [chuckle]
0:06:38.0 HG: Love that.
0:06:41.7 S3: Yeah.
0:06:41.9 HG: Awesome.
[pause]
0:07:20.8 HG: Alright. Hello, and welcome everyone. It is 3:00 PM here in Los Angeles. I'll give us just about one more minute for those last few stragglers as we just are making our final announcements that we're getting started, so bear with us just a few more moments and then we will begin our webinar for today.
[pause]
0:08:04.9 HG: Alright. Hello and welcome everyone. It's 3:01 here in Los Angeles. We'll go ahead and get started with our presentation for today. I am Heather Grant, one of the community admins here at the maintenance community Slack group.
0:08:22.6 HG: Thank you again for joining. If you're not already a member of the maintenance community Slack group, we would absolutely love to have you join. We will share the link in the chat shortly on how to sign up. Today we have Ricky Smith joining us. Ricky is our maintenance expert in residence at the maintenance community. And what that means is that he puts on about one webinar every single week, just like this one, for all of our members, totally free to you. He's also available in Slack to answer questions directly. So if there is anything else you're wondering about after this presentation, I believe he'll share his contact information, but he's also available in our Slack where you can message him directly. If you know anyone else who would benefit from hearing some of Ricky's expertise, please feel free to send them the invitation, the recording of this webinar as well.
0:09:13.4 HG: Like I just said, the recording of today's webinar, we will post in the community Slack as well as all the slides that you see here today. So make sure you go in there, join the Slack and then you'll be able to see all of this material. One last piece of housekeeping before we get started, you'll notice that your cameras and microphones are not turned on, so what you'll do if you have any questions or if you wanna answer any of Ricky's questions, you'll go ahead and hover your mouse over the tool bar where you're seeing my face as well as where you're seeing Ricky's face and then you will see a chat button pop up. You can go ahead and just enter your questions in there, let me know if you can't see or hear or anything else comes up throughout the presentation. You can submit questions any time throughout that presentation, and then we'll reserve about 10 or 15 minutes at the end just to answer any of those questions. Again, thank you so much for joining, and I will turn it over to you, Ricky, to talk about PM optimization.
0:10:09.9 RS: Alright. Thank you, Heather. Welcome, everyone. This webinar is how to conduct a PM evaluation step-by-step. It's gonna be real simple and to the point. You could download these slides at my website, worldclassmaintenance.org any time. And there's other information too, somebody is asking about the CMRP, there's information on the website there. It doesn't require your email address or anything. I don't care who goes there, as long as I can help you that's all that matters.
0:10:38.1 RS: Alright, buckle up. So, let's talk about insanity, perform and prevent, and I've said this for years, Jeff, I know you've heard this many times. Performing preventive maintenance on equipment that continues to break down, it doesn't make sense. It just doesn't make sense. What do we expect out of preventive maintenance?
0:10:58.0 RS: We expect to preserve the asset, that's what we hope to do, to be able to keep it running and functioning to the specification. So here's a poll. Alright, so, I'm gonna ask you to text in your answers. Okay? So you know how to use the text now. So, go ahead and text us on in how effective is your maintenance planning and scheduling process, so how, currently, is your maintenance planning and scheduling process, how effective is it?
0:11:34.4 HG: We have some answers coming in, most people are saying B, there's a C and a D, as well as somewhat...
0:11:40.5 RS: D, B, C...
0:11:41.2 HG: Got another C.
0:11:42.5 RS: D, somewhat.
0:11:45.0 HG: A, we got an A. [chuckle]
0:11:49.2 RS: Standing it up right now. Hey, good timing then, Jeff, good. Alright. Next one, do you have process maps for all your maintenance processes?
0:12:12.0 HG: I think you're reading the chat, but we have, "Yes", "Yes", "No". We have a B and an A meaning a "No" and a "Yes", a "Yes" and a "No" rather.
0:12:24.9 RS: Okay, next question. What are your expectations for preventive maintenance? Equipment functioning, functions to specification, equipment just runs and operates, no expectations, never thought of it or not sure?
0:12:47.5 HG: We have A, A, A, all A coming in so far. There's a B in there as well. Another A.
0:12:57.9 RS: Alright. Let's go to the next one. What percentage of total maintenance labour hours are focused on preventive maintenance? Not sure, 10%, 30%, none of the above.
0:13:12.4 HG: A couple of Cs, we have an A, an A and a C again. So it sounds like people are either not sure or are spending 30%.
0:13:20.9 RS: Yeah, 30% is about what normally you'll see. Most people don't even know what percentage of labour hours are focused on preventive maintenance, so you need to track that information. It's very helpful to know how well you're doing and if things are getting better or if things are out of control. So, do you have a metric that measures PM effectiveness, if the PMs are effective or not? Yes or no. Last question, okay? At least for now.
0:13:53.3 HG: We have a mix of A and B coming in, so about half saying "Yes", about half saying "No".
0:13:57.6 RS: I always... One of the things I talk about, insanity, performing preventive maintenance on equipment that continues to fail, so the metric to me should be PM labour hours versus emergency urgent labour hours. 'Cause if a PM's effective, your emergency and urgent labour hours should be impacted. We should see the difference. Alright, we do have one more. So do operators perform operative care?
0:14:27.5 HG: A few nos coming in, one A, one yes in there, mostly nos so far. Not yet. Good answer, sometimes.
0:14:38.0 RS: Yeah, sometimes, that's what I see most places. Depends on how they feel for the day, feel like doing it. Alright, let's move on. So this is Alcoa Mount Holly. Jeff, I know you've seen this before, probably see the screen saver behind me, that's a pot line one, you know, at Mount Holly. So we talk about best practice benchmarks, 'cause I think that's important to understand, where do we benchmark our information from? So Alumax Mount Holly is where I started my... Well, I started my career at Exxon but then went to work for Alumax Mount Holly. Alumax at the time ultimately was bought by Alcoa and they've spread their message and their whole process worldwide. So here's some of the data from their certification report. So you see Alumax where they were back when I was there and then World Class Maintenance when they made the next step change. So typical, what we see from World Class, maintenance spending, you know?
0:15:39.2 RS: So maintenance spending, the replacement asset value is 3.4, World Class 2.0-2.5, really World Class is really 3.4%, but most of it what I've seen is 6.3%-12%. Budget compliance, it's out of control. John was very adamant about being on target with the money. Overtime, I have to say Alumax, they got 1%. Now I have to tell you, I had a lot of overtime, I worked... 'Cause I was the guy everybody said, "Hey we need somebody to work overtime", said, "Well, Ricky, are you gonna do it?" "Heck yeah, I'll take it." So typical is typically high, World Class is going to be somewhere between 6% and 8%. Number of craft, that's... When we talk about number of craft, we're talking about number of craft that are focused on proactive maintenance. So you got Alumax four, so on the craft you're talking about people that are working on PMs four or less, so they didn't need as many.
0:16:44.7 RS: A lot of times we've got a lot of people working on PM, but we're not getting anything done. Planners per tradesman, one to 20, that's typically what you see in a mature organisation. Typical, you got one planner to 40 people. Absenteeism, out of this world. Backlog in weeks, unknown. And backlog is... Total backlog, numbers of work orders, the ready backlog is two to four weeks, you got World Class Maintenance two to three weeks. Schedule compliance, 95% Alumax. World Class Maintenance, between 90% and 100%. Urgent and emergency work orders, it said urgent, but maybe it was emergency work orders, so less than 10%, typical 30% to 45%. PM, so percent of PMs, PDMs to all work orders, unknown, see 30% on there. PM accomplishment, in other words PM compliance is what this is, 95% to 100%. Inventory accuracy, you see most of the time 30% to 45%, but inventory accuracy that's your inventory. When we do a check, we have the parts according to what it says on the CMMS. Inventory turns, it's high, a lot of times people don't measure it. World Class was two to four. Okay, maintenance training dollars, a lot of people don't even have maintenance training dollars, unfortunately. It's sad, but I tell you, all world class companies, all best of the best companies in the world have a training budget for their maintenance.
0:18:19.1 RS: So let's look at what proactive maintenance and continuous improvement looks like. So we start out, we start out with work identification. Work identification comes from PM/PdM and operator care. So 95% plus of maintenance work orders come from PM/PdM and operator care. Maintenance planning, 95% of maintenance work orders from PM/PdM, operator care metric, metric is percent of plan work. And then schedule, maintenance schedule, 100% of maintenance, labor hours are scheduled by day, by hour. The metric is schedule compliance. Work execution, work... Maintenance work is executed to specification following repeatable procedures. The metric is re-work. All work orders are closed out with all codes and information in the CMMS, the metric is number of work orders closed out accurately. How do you know that? You just... Typically, a planner just pulls a certain sample of them out and they just go through the work orders. So they may pull five a day or something just to check on them to see if the codes were right.
0:19:21.0 RS: Breakdown functional failure, work orders reviewed on a monthly basis for corrective action. And with breakdowns, it's all about the money. It's all about the money. [0:19:31.5] ____ many years ago, he was a great maintenance and reliability leader, said if a step in a process is skipped or performed at a substandard level, it creates defects known as failures. The output of healthy reliability process is optimal reliability at optimal cost. That's a great statement. I like it.
0:19:55.5 RS: So what is preventive maintenance? Good questions. You know, a lot of definitions, if you look on the internet, there are plenty of them. So actions taken to keep, preserve, protect capacity through a disciplined process, which always reaps the same result. If preventive maintenance is a controlled experiment, we put equipment in a controlled state and we do things to it, we should reap the same results. Or close to it. Operator checks, yeah. Do these checks currently meet the objective of the above statement? Yeah, maybe, maybe not. They should.
0:20:30.5 RS: Your ideas of how to achieve this goal. There are many ways of doing it, there's many ways of doing it, but operator operators have to be engaged. They have to be engaged. What frustrates me, I was at a plant recently and they got operators all around the plant doing their things and they're supposed to be doing operator checks, they say they're doing it, but they're doing operator care, they're not doing any checks. And I asked the maintenance manager, "What's going on?" He said, "Well, I have to put a maintenance technician to go and look at certain things every day on every line just to make sure everything is okay."
0:21:01.9 RS: I said, "Why don't we turn this over to production, to operators and let them do that inspection, because they're on the line anyway?" I mean, it can't be something they have to have a tool in their hand, but something they just look at, say, yeah, if I look at that deflection of that B-belt, if it's between the two yellow points, I've got... If it's bouncing between it, then it's good, if it's outside of that, bad. So I want good-bad. Make it easy. The maintenance PM, do these checks currently meet the objective of the above statement? Yeah, I think checks, they should be. If not, why not? So PM checks, not just check the chain drive or not just check the pump. I've seen that many times. Jeff, I know you've seen it too. Your ideas of how to achieve this goal?
0:21:49.3 RS: First thing you gotta do is start, you gotta crawl, walk, run, okay, you gotta crawl, get the equipment running the way it should. I like to start with one asset. And whatever you think is the worst performing asset, that's probably the best one to start at. But what you have to do to it, it's like the old '67 Chevelle sitting in the junk yard. If you buy it and you pull it out and it just sputters alone, if you don't restore it, you can't put preventive maintenance on it. It's just not logical. That's what we gotta do.
0:22:20.3 RS: What measurements do you use to ensure you're currently... The intent of PM is met? Somebody tell me, what is your current measurement that you measure the intent is met? So if the intent is to stop failures, how do you measure that? Somebody text it in.
0:22:49.2 HG: We have MTBF.
0:22:51.4 RS: MTBF? Yeah, that's a good one. It's a little difficult to measure sometimes, but mature companies know how to do it. Alright. So definitions of everything. So I tell you, if you're not a member of SMRP, highly recommend you do, because I use their definitions a lot, the metrics they have, that way someone says, "Where did you get the definition from? Did you create it?" No, I didn't create it. No. It came from SMRP Metrics. So it's internationally known and accepted definitions.
0:23:24.0 RS: They weren't just created by one person. One person may start the definition in the metric in the system for SMRP, but then the review goes out to many people in the society for maintenance and reliability professionals. And then once when it comes back, then they decide whether it's good or not. So preventive maintenance, it's an equipment maintenance strategy based on replacing or restoring an asset at a fixed interval regardless of its condition, scheduled restoration replacement tasks are examples of preventing maintenance. PM effectiveness. A measure of the effectiveness of the corrective work that results directly from... So it's the work that comes from PMs, from preventing maintenance and predictive maintenance. You measure the amount of corrective work identified, yeah. Okay, got it. PM compliance. This metric is a review of completed preventive maintenance and predictive maintenance work orders wherein the evaluations are against pre-set criteria for executing and completing the work.
0:24:21.9 RS: In other words they didn't just check the chain drive in preventive maintenance, it's more... Gonna gotta have more information. PM Yield, this metric measures the volume of corrective work that results directly from preventive maintenance and predictive maintenance work orders. If we keep performing preventive maintenance on equipment and we're not finding anything, something may be wrong. But also if everything we go... Every time we go out and inspect the piece of equipment, we find a problem every time, then probably the equipment condition has got a problem. So PM Yield is the measure... The measure is the amount of repair and replacement work that is identified when performing PM/PdM compared to the amount of PM/PdM being done.
0:25:11.0 RS: I was sitting there one day, I was trying to brainstorm, what does preventive maintenance, continuous improvement look like? So let's start out with, the PM's a plan, a schedule, they're executed and when they're executed we get the results from PM, the results from it, we write a corrective work order from the PM. The corrective work order is planned and scheduled, if the work's executed to specification, the work order's closed out and then it goes into metrics. So the results are reviewed. So now we can see how effective are we.
0:25:47.7 RS: So these are just some of the ones I threw in there, preventive maintenance costs, PM compliance with a 20% rule. Basically, what the 20% rule is is that if it's a monthly PM, you got six days of doing it and then you're out of compliance... I used to love the 10% preventive maintenance rule, but a lot of people don't like it, so I just had to go and I followed the crowd. PM labour hours versus emergency labour hours. Maintenance re-work, that's it's a big deal. Maintenance costs as a percentage of replacement asset value. Another one. But once we review these PMs, it goes back to the PMs being planned and scheduled again. So if we find something on the PM we need to change, we red line it and then once the planner gets it, the planner may review it with the supervisor and decide whether they need to make a change to it or not.
0:26:41.8 RS: Alright. So why best practices in preventive maintenance? To ensure equipment meets capacity, quality and cost requirements. No doubt. Keep equipment in a maintainable condition. To prevent equipment failure when run-to-failure is not your maintenance strategy... When you've been in as many plants as I've been into, it's amazing... Yeah, we're doing preventive maintenance on equipment, I said, "Does it fail?" "Oh man, it breaks down all the time." Something about logic, there's not logic to that. And then to meet production requirements through optimization of asset reliability. It's all about production, don't let anybody tell you the difference, a lot of people get wrapped around the axle about maintenance, but it is all about production but we gotta deliver to them the assets reliably. They have to be reliable assets.
0:27:32.6 RS: So we want to manage with the right KPIs, that way we can make the right decisions decision with data. You know Lord Kelvin, I think it was in 17 something, he was born, he said, "If you can't measure it, you cannot improve it." That's absolutely true, if we want to make the right decision. Everyone knows their score in maintenance, you know, putting a score board up is important for maintenance people to see. So if you play soccer, you play football, baseball, rugby, whatever it is, if you know the score in the game, then you're gonna play harder to try to get that score up. And then people are motivated by knowing their score in the game. Look at the scoreboard, "Wow, man we're doing good." Two types of KPIs, leading KPIs, which lead to the results. Lagging KPIs are the results. Okay?
0:28:27.6 RS: So here's a PM score card I created for you. The PM compliance showing 98%, PM labour hours was 234. Emergency labour hours was 14. We evaluated this week or this month, 9 PMs, we had six stock outs in the store. Stock out is if the computer says that the part is in the store and you go to pull it from the store and it's not there, that's a stock out. And then maintenance costs as a percentage of RAV, 5%. And then OE, 89%. So just trying to get people to score in the game is a big deal in my perspective. So here's a problem and solutions I created in preventive maintenance. Insanity, performing preventive maintenance on equipment that continues to break down. So we got PM activities, PM metrics, possible problem, possible solution. Okay? So PM effectiveness, so just say MTBF, someone had mentioned that. PMs not focused on failure modes. Failure modes is how something fails. And we say, Well...
0:29:34.4 RS: Let's just take a gearbox. How many ways can a gearbox fail? By bearing failure, right? The bearings, how would a bearing fail? Lack of lubrication, contamination, there's a lot of ways. Ineffective measurements, we're measuring the wrong thing. No step-by-step procedures. So we got a PM, check chain drive, yep it's there. No verification if PM is completed to specification. And then personnel not following procedure. Possible solution? Engage maintenance techs in evaluating PM. When I was a maintenance supervisor one of the things I did every week is I would just randomly pull, have my planner pull a few PMs out, and then I had... I would plan and schedule one technician for a day to go through those PMs, look at the failure history on that asset and determine what we need to do. Do we need to change something or not? And I like posting this graph, it says, "PM labour hours versus emergency urgent labour hours", I tell you what, it makes an impact.
0:30:34.2 RS: To lubrication, PM compliance using the 10% rule. Measurements, possible problem, measurements with high variation. Lack of training and best practices, no oversight by maintenance leadership. Determine type and grease, the solution, we need to have to determine not just the type of grease but how much grease is required. Two shots? What's two shots? You got a double pumper grease gun or you got a single pump? Or are you using an air pump? I don't know. You need to inspect the lubrication process. Time based change out, schedule compliance by day, by hour is the metric. Possible problem asset, unavailability. So you go to change it out, and production says, "You can't get it this week. We're gonna have to move it to next week." Next week comes, got to move it to the following... Machine's running well, what are we doing changing them out for? Maybe it's based on good data.
0:31:28.3 RS: Maybe planning and schedule not affected. So the solution on this one, planning and scheduling, training for planners and leadership. I think that any planning and scheduling training, I think leadership should go through the first day, and if they can't stay in the first day, at least the morning of the first day. Operator care. Sorry about the noise in the background, I got a Great Pyrenees and he must think there's something out there. Or he doesn't like the way I'm talking.
0:32:00.7 RS: Operator care, some PM activities, PM compliance by shift, PM effectiveness. Possible problem, no specifications on PM, lack of reporting for corrective action. Lack of management support. So measure effectiveness of PM compliance of operator care. Why not? Why not? We gotta know... If operator care, people don't... Believe it or not, you may be surprised, people have operator care but they don't measure it. They don't check it and see what's going on. Common traps to preventive maintenance as a strategy. Most PM tasks are not based on failure modes, how something fails. Not enough detail in PM tasks to be value added. It says check chain drive, check it's there, check v-belt, check it's there. Check bearing, check it's there.
0:32:47.6 RS: Too many wrong tasks specified resulted in PMs often not performed at all. You got a list of PMs, tasks, 100 of them and you've gotta complete them in a day, it doesn't make sense. Asset unavailability. I apologize, my dog. I got animals and I got coyotes, must be coming close to the animals, so sorry. I live on a farm.
0:33:12.7 RS: Asset unavailability during PMs can outweigh reliability gains. Lack of management, focus is a big one and PMs often view it as low priority. We can't do those PMs this week, push them off to next week, probably none of you have ever seen that before, I personally have experienced that. Widespread dependence on inappropriate vendor suggestions. Think about this, a vendor tells you, recommends how you should... How often you should replace something or inspect something and they're selling you the parts, what kind of suggestions do you think they're making? They sell parts.
0:33:52.1 RS: So PM procedure example, these procedures are so critical. In most places I go I don't see this, I don't see a good procedure. It may say something very simple, but it doesn't give me enough repeatability, enough information to make it repeatable. So on page one, what I've got is equipment block ID, equipment hierarchy, the project description performed, PM on SEP TEP process line. And under this, we gotta just get down to it, the job description. So on this one is, for this, it's to perform PM on the hydraulic system. Says two techs, three hours.
0:34:27.6 RS: So the allowance time is three hours. Estimated production down time, three hours. You see the originator and so on. What I like to do... I mean, if you're gonna have to have... If you're gonna do PM and you know you gotta change filters or zinc anodes, whatever, then why not have it on the work order so the planner, when the planner plans the PM he can go ahead and pull them from stock and kit them in a secure area so when the job is scheduled that day, maintenance technician goes in and pulls the kit and goes does the job.
0:35:02.9 RS: And you notice... If you don't pull 'em, there's a part number on there. But mainly that part number is on there for one reason, and that's on there for the planner. Okay? Any consumable, special tools, required shutdown, that's more for the planner. But here it's got the description. What I like is have step-by-step description on the PM. And you know if you go all the way over where it says step-one, go all the way to the right, it says craft initials. My maintenance techs, I wanted their initials on each step. Why? Because I thought it was important enough for them to make sure they did that, and not come back in the shop and initial it all the way down. 'Cause if I come up and check on my guys and they'd already initialled something they haven't done yet, then we got a problem.
0:35:44.5 RS: And you'll notice down there it says, inspect rod seal for leaks, number six. I've given you a... I've given my techs a way of saying, you know, for the rod seal, no leaks, weeping oil or oil streaming. So I just give them some kind of clarification, that way it gives me an idea as the maintenance supervisor but also the planner, how bad this thing is. Then I go down, condition as found, condition as left. Comments, any findings. So, we need to change the filter, we need to do this, or whatever. Craft feedback on procedures. I want the crafts to give feedback on the procedures on PMs. On any procedure, any maintenance procedure we should have it. Then I want craft signatures on there at the end of the day. Any craft, any person, technician that's on that job, that's on this PM should do that. They should sign it.
0:36:37.9 RS: Alright, so measure and preventive maintenance. If you can't measure it, you can't manage it, Peter Drucker. Absolutely. Alright, bear with me a minute. Come on. Bear with me a minute. Computer's messing up.
0:37:11.5 HG: Ricky, try hovering over the bar where it says you're sharing screen and see if you have something called annotate on.
0:37:23.2 RS: Yeah it's got everything and I clicked it, the draw.
0:37:29.2 HG: Yeah, you should be able to find a place... My toolbar looks a little bit different than I think yours will, so I'm not exactly sure where it'll be, but I think there should be something regarding annotate or draw on the screen in that tool bar where it says you're sharing your screen.
0:37:44.3 RS: There you go, I got it. Thank you.
0:37:47.3 HG: Yeah, of course.
0:37:47.8 RS: How does your company currently measure effectiveness of the PM? That's a question. So you guys texted text in. How does your company currently measure effectiveness of your PM program? Just text it in. Make it simple.
[pause]
0:38:11.9 HG: Somebody shared, they have audits at the end of each month, there is PM completion percentages. And someone says, "We don't." [chuckle]
0:38:20.7 RS: That's good. We learned something there, 'cause one says they do. That's important.
0:38:26.8 HG: Yeah. We have somebody saying, PM versus EM hours.
0:38:33.8 RS: Six to one.
0:38:35.6 HG: Six to one. There you go.
0:38:35.7 RS: Oh yeah, Jeff, make me proud buddy. Make me proud. Okay, let's move on. So, how do you know if your current PM program is effective or not? How do you know that? Hours spent doing a PM, spent on reactive work orders. Yeah. Absolutely. So definitions, Key Performance Indicators are metrics which help an organisation measure the process such as PM. Leading KPIs, leading results, lagging KPIs are the results.
0:39:16.2 RS: So the fundamentals of effective PMs. All equipment PMs are focused on specific failure mode. Now, some people say, "Well, we got some that are based on environmental or whatever." They're still failure modes. If we got environmental spill, how did it fail? So it's still a failure mode. All PMs should have the following: Step-by-step instructions, just like I showed you, and I want my technician at initial each step, so they don't skip a step, need to have specifications if specifications are required, extra space available for extra information, condition it's found, condition it's left, recommendation to changes to procedure. So when a work order is given to a maintenance tech, the following should be attached. This is the way... This is just me. You can do it however you want. I used to attach the equipment failure history since the last PM, so they get the work order history with it. So when they're doing a PM, first, before they go out, they review that so it's in their head. When they're going out, they're doing a PM, is there something missing? We doing something wrong.
0:40:22.1 RS: If the equipment failed fails between PM cycles, an RCA should be initiated. And post the metric and the maintenance shop on a line graph. PM labour hours versus emergency urgent labour hours, I would put it in the shop, and they called it the Hawthorne effect. It was a gentleman that came up with this, the behavioural change, by showing something. So if you show somebody something different, they'll change behaviour, and that's what this whole metric's all about, this PM versus emergency urgent labour hours. So you notice on this chart I've got here, PM labour hours are fairly stable but emergency urgent is just all over the place. It's out of control.
0:41:00.4 RS: So just talking about some possible problems and solutions. So we've got this PM activity, so PM inspection, PM effectiveness, MTBF, possible problem. Just like we've been talking about. PM's not focused on failure mode, ineffective measurements, no step-by-step procedure, possible solution to gauge, maintenance techs and PMs. Lubrication, same thing. We got it. One thing big on this is if we've got... If lubrication is not working right, maybe we're putting too much grease in it or not enough.
0:41:37.8 RS: We have to know, if you have grease guns, all grease guns should have the same amount that they pump out. What I did with mine, when I found out we were over-lubricating, I went in our lab and we take one pump on the grease gun on their little scale... They freaked out over this, on their scale and then we'd measure it, so we knew what one pump was. And then we talked to the engineer with SKF, and he told us, "Based on that type of bearing and the rotation and the load it's under, it should be this many grams of grease," so we knew how many pumps of grease we had to put into it. Time-based change out, if you can maintain it, that'll work. It absolutely will work but that's a tough one, and I know some have it but it's not always worked so well. Alright, so operator care, PM compliance by shift and then PM effectiveness.
0:42:37.9 RS: So failure modes. We talked about that. So failure modes, how something fails. For so example, rolling element bearings, improper installation. There's not so many ways that a bearing's gonna fail, a rolling element bearing's gonna fail. Over lubrication, yeah, under lubrication, contamination and there's some other ways too. There's so many ways they fail, that's the whole point. And I'll tell you, a lot of times if we understand what caused the failure, then we can do something about it.
0:43:14.5 RS: I'll tell you, a good thing I've seen before in the past is that one organisation, what they would do is if they had a bearing failure that was unacceptable to 'em, what they would do is they'd send it to a machine shop and have it cut in half and they's send it back. And what they would do is actually they put a sheet of paper out there and whoever could come up with what the true root cause was of that bearing, then the maintenance manager would buy the technician, him and their spouse, a dinner at some restaurant downtown, which I thought was kind of unique, that it was kind of interesting how he got the people motivated that way. I think it was Cargill, where I saw this at.
0:43:54.1 RS: So what to do if preventive maintenance is not meeting expectations? Acknowledge you have a problem. Just like if you drink too much alcohol, you gotta admit you drink alcohol before you can say you got a problem. Assemble a PM optimization team, maintenance techs, maintenance supervisor, operators. The PM optimization team establishes their vision, their mission and the guiding principles that are approved by maintenance production plant leadership, and they meet weekly for 30 minutes max. I like to have a time keeper. "Five minutes, times up, let's leave." That way, you're not taking people's time. People can make their time if you keep a meeting scheduled the right way.
0:44:38.0 RS: Identify the equipment that has the most losses; OEE, production loss, emergency urgent labour hours. That's a big deal. Post a dashboard to meet progress and effectiveness of it, to measure it. Create a PM problem and solution board using the A3 approach to problem-solving. I like this one. So here we got a problem. Let's say I had a bearing on asset number 4001, bearing failure, seven times in the past 24 months; PM deferred 22 times due to production requirements; lost production, 2300 units of production; the loss and cost of production, $220,000; PM compliance, 90%. Woah, that didn't make sense. Medium labour cost for the breakdown was $2400, maintenance material cost was $4534, found similar assets having the same failure. That's interesting. So cause of the problem, over lubricating results in seal failure, then bearing seal failure. So the seal failed and the bearing failed. Contributing factors, lack of effective PM procedure, no PM frequency established, inefficient training or lack of knowledge of the maintenance techs.
0:46:06.5 RS: Then resolution, education with all techs on lubrication best practices, that's a great one. And then they measure sustainment. PM compliance need to be restructured, but they correlate maintenance costs to PM compliance and measure MTBF on this asset for 12 months and reassess. I'm sure all of you have seen the P-F curve before. Okay. So the P-F curve, over to the left, we've got a line goes up, conditional probability of failure, and as we go down the line, we start having a random failure. So that's... Where does the PM fit in this?
0:46:46.2 RS: So, we have a conditional probability of failure, failure starts at some point on the P-F curve, and then once it hits potential failure, is when it could fail any time within that P-F interval. Now, this is the graphical representation of how something fails, so it's not necessarily what you may think. So, today's definition of failure, equipment not performing intended function, so functionally fail, the old definition of failure is broke. So where does that PM fit? It fits on that P-F curve. What we wanna do is we want the PM to where we can do something to the equipment, whether it's we change something out, we find it on PM, we change it out before it fails or we get lubrication that's starting to degrade, the bearing's starting to degrade slightly, we put more lubrication into it.
0:47:34.2 RS: Alright. The attributes of a proactive maintenance technician ensures all maintenance work is executed to specification. Perform preventive maintenance as a controlled experiment, we put equipment in a controlled state and maintainable condition, and we do certain things to it, like inspect it, lubricate, adjust or so on, to have that... The results we desire. So preventive maintenance vision statement, preventive maintenance will meet the intent of the stockholders of our company through a disciplined approach and execution, management and measurements. So the mission statement, preventive maintenance will be conducted as a controlled experiment resulting in optimal asset reliability at optimal cost enabling optimal process reliability at optimal cost.
0:48:28.5 RS: Preventive maintenance on guiding principles. Preventive maintenance most important routine function, a maintenance personnel must accomplish this specification. Preventive maintenance must meet expectations of production, that's that optimal process reliability. Preventive maintenance must be measured with... Using the right leading and lagging KPIs. You think I've beaten this one into you enough? Leading and lagging KPIs. Yeah? So here's some leading KPIs of PM, PM compliance, using a 10% rule, in other words a monthly PM, we've got three days to do it or we're out of compliance. Percentage of PMs with step-by-step instructions. Percentage of PMs evaluated monthly.
0:49:04.1 RS: How many PMs have we evaluated monthly? You've gotta come up with that, but we have to be... Just pull randomly, you know, PMs randomly every month, you need to start evaluating them. Number of defects found. Lagging KPIs, OEE, maintenance material cost, maintenance over time and rework. PMs must be evaluated for effectiveness if equipment failures are occurring. Maintenance techs are involved in PM evaluation optimization. If you have reliability engineers, nothing wrong with them facilitating. I want maintenance technicians in the front seat. Okay, I want them on the front row, engaged, and doing that PM evaluation and optimization. Alright. So what are your questions?
0:49:55.4 HG: Thank you, Ricky. That was awesome. I did see one question come in a little bit earlier, but if there are any other questions now after Ricky's gone through all of the material for today, please send those in the chat now. The question from earlier that we saw, says, "If a company spends too much money on PMs compared to best-in-class, what are some quick actions to address the issue without impacting reliability?"
0:50:26.6 RS: So, something you can do right now to impact reliability, start measuring things the right way. Start measuring the right way. That's a big deal. PM optimization is not difficult, if you pull an example of PMs out, sample of PMs out in an area you're having problems. Give them to certain people, let them look at them and match it up, like I said before, with the metrics, what's going on, and then making sure that you have a SOP of on what a good PM looks like, should've have... Like in a PM, I don't need a lengthy sentence. I want a noun, adjective, and a verb, maximum. That's all I need. Check chain drive, okay, fine. Check, chain drive, what do I check? What is the specification for that? Which is important? Alright? What else?
0:51:25.9 HG: How do you convince management to implement the right PM rather than the lowest bidder?
[laughter]
0:51:32.0 RS: The lowest bidder. That's a good one. That's what most people do, right? They get the lowest bidder to do it. Yeah. Well, you gotta start somewhere. Best thing you do is you gotta prove it to somebody, whoever that is, you gotta prove it to him and prove it to management. So a lot of times you don't ask for permission, you can... What's in your sphere of influence, that's what you control. But if you wanna test it and the thing to do is maybe talk to your manager, say "Hey, this is what we need to do, I'm recommending this." And then we go and make it happen.
0:52:09.6 RS: So why do we conduct 'em? Why do we conduct PM evaluation? 'Cause we got problems, right? Reason number one, never thought about the impact a PM evaluation would make. So we got equipment problems failures, production's throughput and so on. Reason number two, free up maintenance staff to perform proactive maintenance. That's a big deal. 'Cause if wrench time is low, wrench time is hands-on tool time, if wrench time is low then we need to do something to increase it. Breakdowns take away time to conduct PM and correct the maintenance plan and schedule. Take operator care to the next level. Operators take pride in operating equipment. Stress goes down, everybody's happy. Minimize process and asset failure. And it goes back to this one, to reduce cost. We gotta reduce cost.
0:53:04.4 RS: Alignment. You gotta educate people in PM best practices. Now these are toolbox talks that I've created. And I gave you... You see at the bottom, where you can go to to download these, I got a lot of them on this single point... I'm transferring from toolbox talks to single-point lessons. Okay? But a lot of this... I've got the one on PM optimization in there, you see it over to the right. Great things for you to use, and you could steal the ideas, make it your own and that's what you gotta do. You gotta make it yours, okay?
0:53:39.4 HG: So let's talk about, how do we do PM optimization step-by-step? Well, we identify an area to evaluate PMs on. Notice to the right, I did this at a board plant recently. What we did was we talked about, where do we begin with a PM optimization in the board plant if it's a massive plant? So we said, "Okay." The few things we look at to identify that, which area we go to, on this one was which one do you have the biggest problems, the most concerns, where are the operators complaining the most?" And that's what we did. And so what we did was we put a block, like you see in this chart to the right, this little diagram, we blocked that area in.
0:54:21.6 RS: Say, "Okay, we wanna evaluate the PMs just on that equipment there." That's it. We don't wanna look at all the PMs, all we wanna do is focus on that area. This is the proof of concept. This is how you're gonna prove PM optimization works. Identify a cross-functional team. I want an operator in there. I don't care where he's at. The operator operates that machine in that area. I want them on the team. Maintenance technician, reliability engineer, if you have one. If not, maybe a maintenance supervisor. And I want the maintenance planner in there, 'cause they usually have access to the history, the information we're gonna need for this. Identify roles and responsibilities for the PM optimization process. Establish expectation of everyone engaged in this process.
0:55:04.5 RS: Like I say, so we asked Jose over here, "Jose, what's your expectation?" "Well, I just want things to run better." You ask Susan over here and she says, "Well, I want this machine to run all the time." Okay, so everybody has different expectations, but I want to get the people engaged by asking them the question to find the end goal of the process. "What's the end goal?" We want the equipment... We want OEE back up to summary, okay? Define how you would measure PM optimization as effective or not. You gotta define the metrics. What are the metrics we're gonna measure?
0:55:39.8 RS: And maybe, especially, if we're measuring already, but maybe we need to change it, like PM labour hours, emergency urgent labour hours. I mentioned that metric before. Present all copies of the PMs to each person, review history, have the equipment history for the past 30, 60, 180 days, number of breakdowns, I wanna know, causes of critical breakdowns based on a formal RCA. PM labour hours versus emergency urgent labour hours, you may have to scramble to get that information, but it's probably there somewhere, and if you're not, then we need to start measuring it after this class, okay? Review current PMs and PdMs to identify PMs may need to be rewritten. So it's good. It just, like it may have a... One statement should be, "Check Chain Drive," but it has a long two sentences that say, "Check Chain Drive." Make it simple.
0:56:38.5 RS: Training, which may be required. PM frequency may be inaccurate. It may need to be adjusted. Is the equipment in a maintainable condition? 'Cause if it's not in a maintainable condition, how can we do PM work? Rewrite PMs. Rewrite the PMs or write new PMs, and then monitor and measure if these new PMs are effective or not. Now I mentioned before, roles and responsibilities, number three there. Okay. So defining roles and responsibilities... If you're gonna do a PM optimization process, people have to know their stake in the game. Okay? So it's fairly simple.
0:57:16.7 RS: So, first thing we do, identify the PM optimization process. So task... Do you see the first task? Create the PM optimization process, identify cross-functional stakeholders, stakeholders' expectation is identified, define end goal, define how to measure PM effectiveness and efficiency, review equipment history for the past 30, 60, 90 days. Sound like what we just talked about before, right? The PM optimization process. Review PMs by task steps, create and measure PM effectiveness and efficiency with a score card, and then modify and rewrite the PMs. Now, number two, identify the cross-functional stakeholders. Here, I got a plant manager. That doesn't mean the plant manager is gonna be in the room, he's just a stakeholder. Production manager, maintenance manager, storage store manager, maintenance tech, maintenance supervisors, maintenance planner, CMMS administrator.
0:58:06.7 RS: If you go down to the very bottom where it says "Responsibility, accountable, consultant consult, and inform," the way this works is, when we talk about responsibility, so responsibility is the doer. Okay, that's who does it. So on the stakeholder expectation who is identified a doer is the production manager and the maintenance manager. Accountable, on that one line, you could only have one. This one doesn't have one on it. That's okay. But I would say on something like this, maybe the plant manager would be accountable for. Consultant, two-way communication.
0:58:43.4 RS: And then inform, one way communication. You notice nobody's name up there, it's just their positions, 'cause that's what we work on. It isn't about the people. It's about, what are they doing in their position, okay? Define the end goal. Define how to measure PM effectiveness and efficiency. Review equipment history, we talked about that, for the last 30, 60 days. Review PM tasks, steps, none-value-added, reassign operator care, reassign the lube route, replace with PdM, re-engineer, new modifications required, and then create, again, your metrics; we wanna know efficiency and effectiveness of our PMs. So what do you guys think about defining the roles and responsibilities when we set up the PM optimization on one specific asset or area? What do you think about that? Do you think it'll work?
[pause]
0:59:46.6 RS: Alright, text it in.
0:59:57.2 HG: We have yes, I think that would work. Yes. Yes, but you have to follow through. Yes.
1:00:07.8 RS: Modified, step number nine, the last one. Modify, write PMs or new PMs and measure the results. So here's the results from a PM evaluation. Okay, so the PM task, there's only a few of them, none value added, delete, in other words, they add no value, get rid of them. Reassign to operator care, reassign the Lube route, replace with PdM. And a lot of times with PdM, when people are doing PdM, we may have an inspection, that's a visual inspection, but we have a contractor or we got a PdM tech that's looking at the same thing we're looking at, it doesn't make sense.
1:00:45.4 RS: We don't need both people looking at it. If the PdM technicians are gonna be there, why can't they do the visual inspection on it? Re-engineered, that means we need to modify the PM, no modifications required, okay. We identified a number of tasks and then the percentage of those tasks under each class, task action recommendation, and then we wanna put the labour hours that represented. Notice here, this is actually a PM evaluation that was done, I'm not gonna mention the company, 87,297 labour hours or man hours, okay.
1:01:22.9 RS: So here I've taken these PM tasks, so here's the evaluation actions, okay. So on one of them, it says none value added, we delete the task from PM. Reassign to operator care, what that means, move PM task to operator care, it's that simple, move it from the maintenance to operator care. Reassign to Lube route. If you start getting your equipment in a controlled state, why can't I take one of my technicians, send them to training, get them qualified, and maybe even get them certified in lubrication.
1:01:33.2 RS: And all their job is lubrication. But when they do lubrication it's like the PdM Tech, they're also gonna do visual inspections while they're there as well. Replace with PdM, move PM task to PdM, why not? Maybe it's not looking for the right failure mode. Maybe we need to have PdM on it. Re-engineer, all that means is it... It's just rewrite the PM, that's all it is, that's all that means. No modifications, tasks as good as fail. That's all. Alright, so text in your questions. This is preventive maintenance best practices workshop plus PM optimization. I know you're drinking from a fire hose here, but this is gonna be virtually on Zoom, it's not gonna be at Southwestern University, 'cause very few people are traveling now. So text in your questions.
1:02:12.6 HG: Alright, we have a few questions already in here. We have about five minutes left, so we'll try and get through as many as we can and then we'll have to have the rest of them kind of answered afterwards. But one of the first questions here is, "How do you measure the value of preventive maintenance in terms of financial terms?"
1:02:17.3 RS: Well, if you think about it, emergency labour hours... Emergency labour hours, is there a cost to that? What do you think?
1:03:24.1 HG: Yes.
1:03:25.6 RS: Yes, absolutely there is a cost to that. So if we're doing PM right, there's a cost to it. Big time. You have time, parts and tools, absolutely, Duncan great point. Alright, yeah, it's all about the money.
1:03:40.5 HG: Yeah.
1:03:41.3 RS: It's all about money. No doubt about it.
1:03:44.9 HG: Another question here is, "What's the most effective way to address the PM schedule with operators? Currently, they're getting a lot of push back from the managers on shutting equipment down for however long, no matter how much they explain the importance of it, they're hard-headed and only give us a quarter of the time to complete the activities."
1:04:02.3 RS: An operator care round shouldn't be something they have to go out of the way to do, they're already standing by the machine. Like one plant, we just put targets on the machines for them to look at things, and it was either yes or no, good or bad. That's it. So the operators, it was very simple, is there a problem there or not? No.
1:04:18.7 RS: Okay, move on. Don't wanna make it complex where they got a piece of paper or something like that, or a PDA, sometimes that makes it too difficult for them to try and operate the machine. So you gotta think out of the box, what's an answer for that? But the way I've seen it, we did it in one plant, was we actually put targets up for them and they only had... We kept it very simple. And certain things they had to look at, say what they saw. Temperature on hydraulic system, okay, what's the temperature on it? Write it down. Okay. Is there any vibration, abnormal vibration to the floor? That's always a good one. I've seen that many times. You have colour code gauges, that meter red, yellow, green. Absolutely. Alright, what else, what's your the other question?
1:05:06.9 HG: I'm looking in there now. What is best-in-class number for a percentage of maintenance spend on preventive maintenance/predictive maintenance?
1:05:18.2 RS: Wow, that's a good question. A lot of times, PM right now in most companies, is too high. So to say, where should I be, it's gonna be a natural occurrence where it goes to. If you were to measure in PM right now, what you're measured in is the PM labour and then the parts or maybe something they use in it. Now, hopefully in PM, if you're doing... If you're replacing something on PM, then that should actually be a time base change out, not that, "Oh my gosh, I go to it and I gotta change it out." But it doesn't hurt, so if you wanna measure PM, to me the best thing to do overall is just measure PM labour hours verses emergency urgent labour hours universally.
1:06:01.5 RS: Don't focus in on a machine, focus it much, much higher. Most of the time, training's required for all involved. Keep it simple. I used to like to do it with my guys, I did them 15 minutes every week. First, we started with 30 minutes, we ultimately got to 15 minutes, did these toolbox talks, trying to educate people. The big deal. Hey, Hank, I like that colour code gauges, meters red? Yeah. Yellow, green? Yeah. So it's just check. What do you see? Is it in yellow, red, or green? Great point.
1:06:31.6 HG: Alright. Well, that is just about our time for today. There are a few more questions in here, but I've noted them down. When we post the replay tomorrow, Ricky, I'll tag you in it, and I'll add these questions maybe in the thread there so that we can get some answers, kind of right next to the replay of this as well as the slides.
1:06:49.4 RS: Alright, sounds good.
1:06:50.8 HG: Awesome. Well, thank you so much again for joining today. We are back Thursday with our next webinar, so be sure to tune in then. Until next week, I'll see you then, Ricky, and have a great rest of your day, everyone.
1:07:05.8 RS: Thank you.
1:07:06.7 HG: Awesome, thanks so much.
1:07:07.7 RS: Bye.
1:07:07.9 HG: Bye-bye.
Want to keep watching?
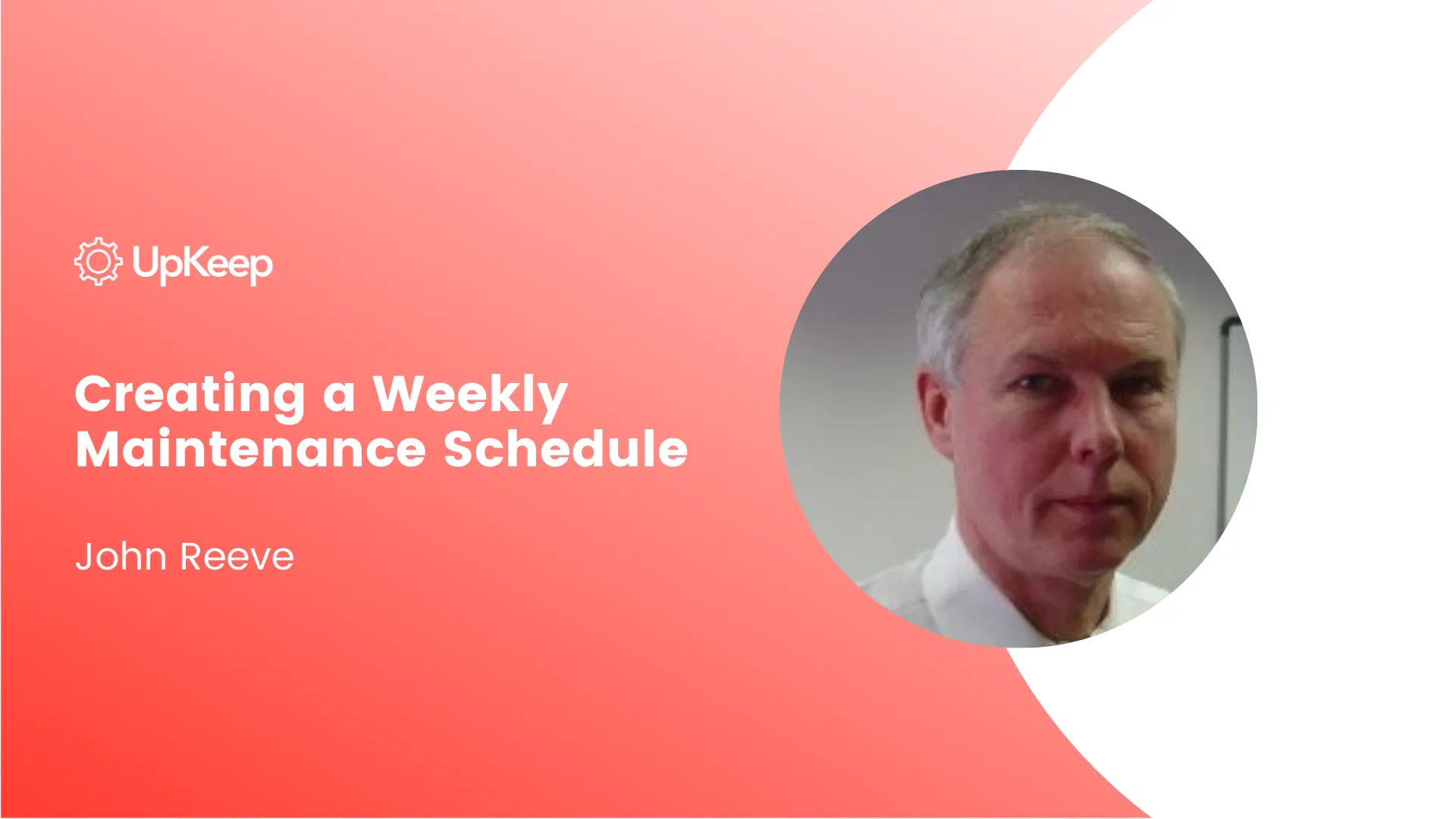
Event
Creating a Weekly Maintenance Schedule
Join John Reeve as he discusses best practices for creating a weekly maintenance schedule.
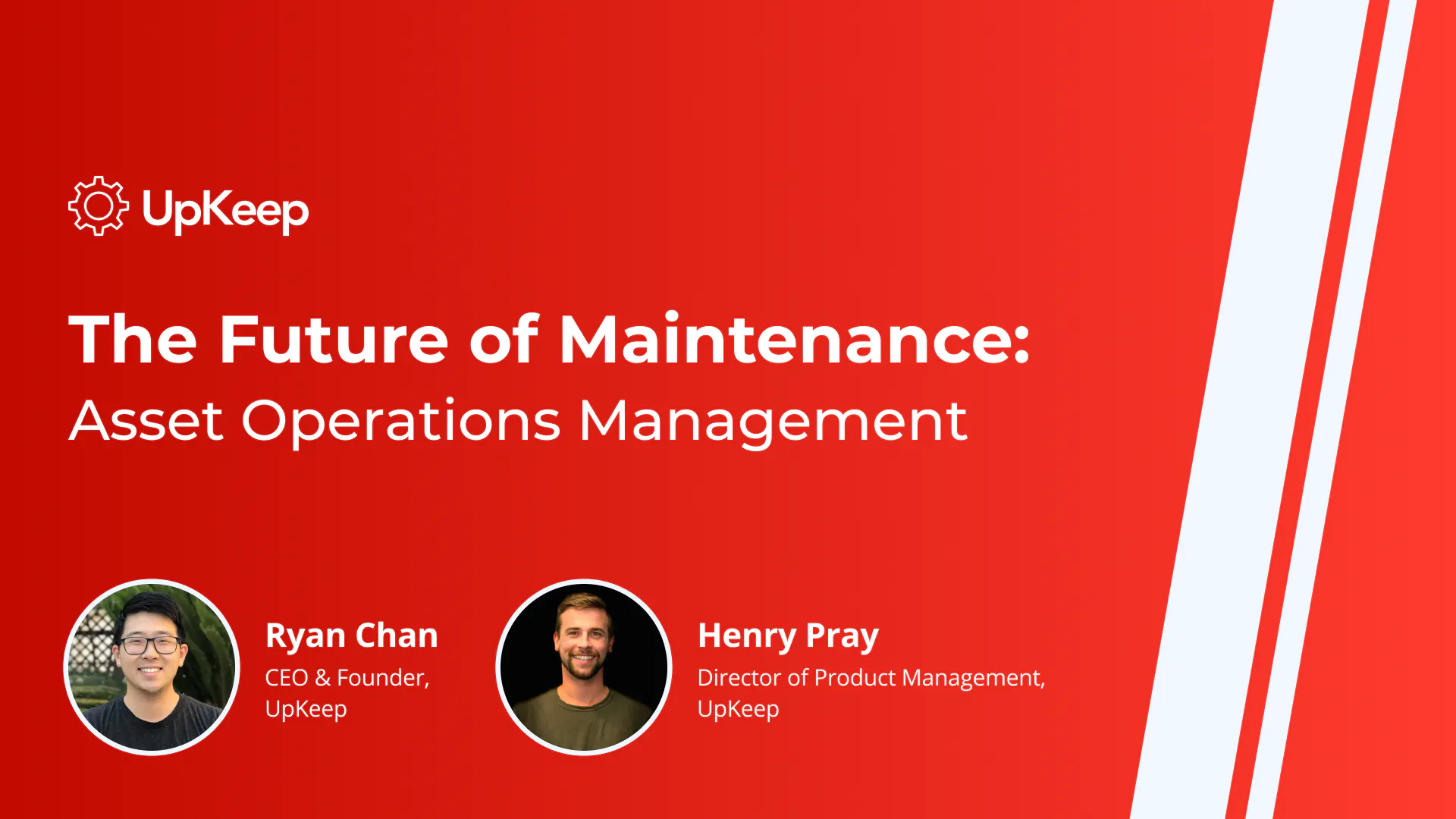
Event
The Future of Maintenance: Asset Operations Management
Watch UpKeep CEO and Founder, Ryan Chan and Henry Pray, Director of Product Management, for “The Future of Maintenance: Asset Operations Management''
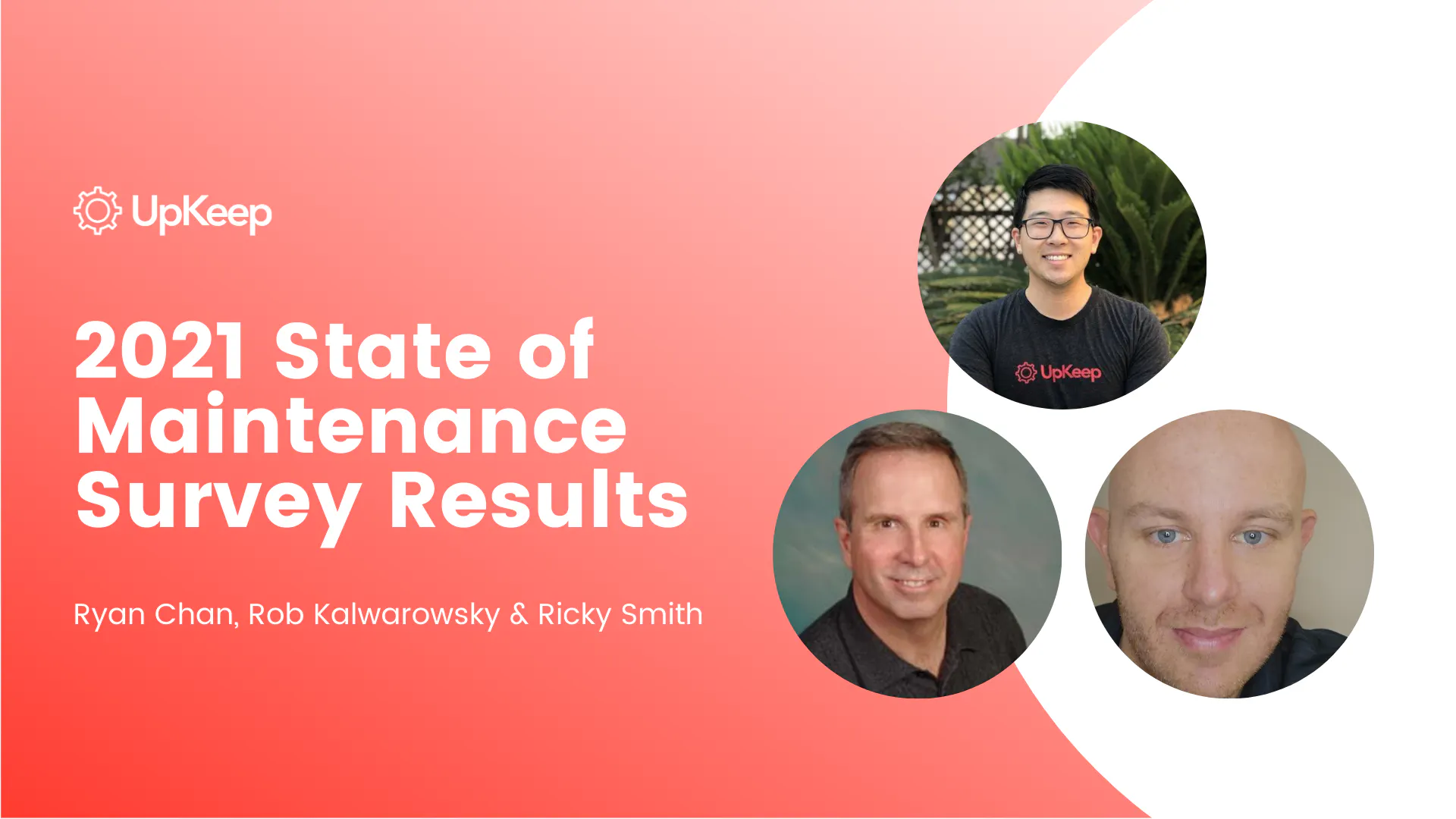
Event
2021 State of Maintenance Survey Results
Watch the panel discussion between experts from the maintenance and facilities industries on the top trends from the State of Maintenance 2021 report.