Energy Company saves time by automating and streamlining processes
A global renewable energy company was on a path to rapid growth. As the company secured more clients, it needed a maintenance system that would allow it to more easily and efficiently track, report, and bill clients for labor and parts. They selected UpKeep’s mobile-first solution.

Challenge
The energy company worked with a wide variety of clients throughout Europe. Its mostly manual system used to track labor and spare parts was manageable with a smaller number of clients. However, the company was positioned to grow rapidly if it could scale up tracking and reporting maintenance activities more efficiently.
Solution
The management team at the company selected UpKeep about three years ago. It was clear to the management that UpKeep’s leadership had the same struggles in finding programs to specifically suit engineering teams and maintenance. As UpKeep was designed specifically for maintenance requirements, it actually did everything the company needed it to do. Today, the maintenance and operations team uses UpKeep to service nine offices throughout Europe.
Results
With UpKeep embedded into 90% of this energy company’s business, the solution generates significant cost savings and efficiency improvement. For instance, if each engineer saved only 10 minutes of time over the course of one year due to increased efficiency, the company would save approximately £150,000. Shifting that extra time to revenue generation results in an even greater impact. The management team believes that Upkeep has helped facilitate the organization’s rapid growth--five times over the course of four months due to earning a large contract. The company is expected to double again in size within the next year.
Quick and Easy Onboarding
Once the company selected UpKeep, the team found the onboarding process very simple. They were able to set one site up and then mimic every other site within seconds. Teaching employees how to use the templates was fairly straightforward; onboarding a new engineer took them less than two hours. The team found the product self-explanatory.
In many companies, maintenance teams often have technicians who are not technology-savvy, and they can be a challenge for organizations trying to implement automated solutions. This energy company, however, found that these individuals were the perfect technicians to start with. One such engineer was asked to test UpKeep with no instructions; he was able to use it without any issues or problems and gave it a sterling review.
More Efficient KPI Tracking Reduces Time, Costs
Although the energy company has always had to track key performance indicators (KPIs) such as response time, availability, mean time to failure and repair times as part of client contracts, the process used to be very cumbersome.
Now, UpKeep is embedded into 90% of what the energy group does as a business. For example, engineers complete a weekly timesheet and all hours are allocated to different project codes. As they complete work orders, their times are banked to certain projects, and at the end of the week, they can easily see how much of their time was spent on each project to complete their timesheets accurately.
Before UpKeep, all that information was managed on a spreadsheet, which involved manually manipulating data, formulas and information. In UpKeep, they simply use the reporting tool, and with a click of a button, a report is generated. Everything has become far more automated and streamlined, which saves a lot of time. The company calculated that if every engineer could save 10 minutes of time over the course of one year, the company would save approximately £150,000. If that extra time was used to generate revenue, there would be an even greater impact.
The energy group, as a whole, has grown five times over the course of four months due to the acquisition of a large contract and expects to double in size again over the next six to 12 months. The management team believes if they were still using their old reporting system, they would not have been able to expand at the rate they did, nor would they have so much growth potential.
Better Spare Parts Tracking Reduces Damage Fees
In addition to managing technician hours, UpKeep also helped the company track spare parts and develop accurate client reports.
After the company signs a contract with a client, they agree to hold a level of spare parts inventory. If that spare part is needed and unavailable, the company must pay damages to the customer. Prior to UpKeep, they would use email and a spreadsheet to track that spare parts inventory, which was a very manual process that often missed things. Now the company populates UpKeep with a contractual spares list, which allows them to maintain the agreed-upon minimum stock levels. Since then, they haven’t had to pay damages.
The energy company provides spare part tracking and updates to its customers on a monthly basis as well. They estimate that roughly half of all the company’s reports are now populated using data from UpKeep.
Growing Together
When the energy company began using UpKeep, the team primarily employed it as a maintenance platform alone. However, the more they used the system, the more they used APIs and recognized even greater potential. Now, the company takes advantage of the new features, metrics, and measurables that UpKeep continues to add. As the solution has developed over the last three years, they have jumped on the bandwagon and benefited from it.
They expect the relationship to continue to be a mutually beneficial one. UpKeep has allowed them to save time, which in turn, saves money. As a result, their costs to provide service decreases. In the end, that means a good market value price and a better ability to compete and continue to grow.
Want to keep reading?
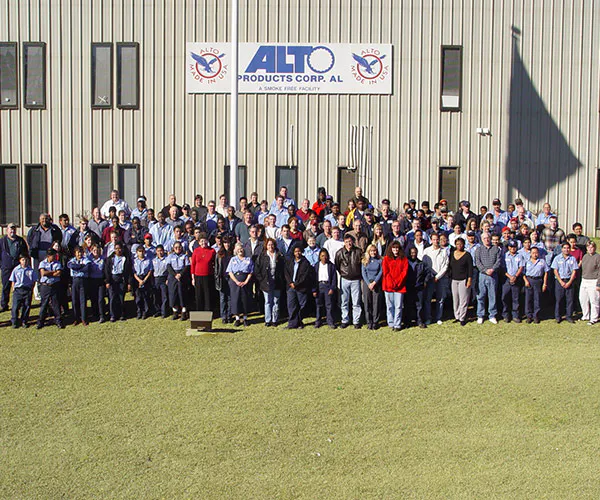
Equipment / Manufacturing
Alto Products moves from reactive to preventive maintenance
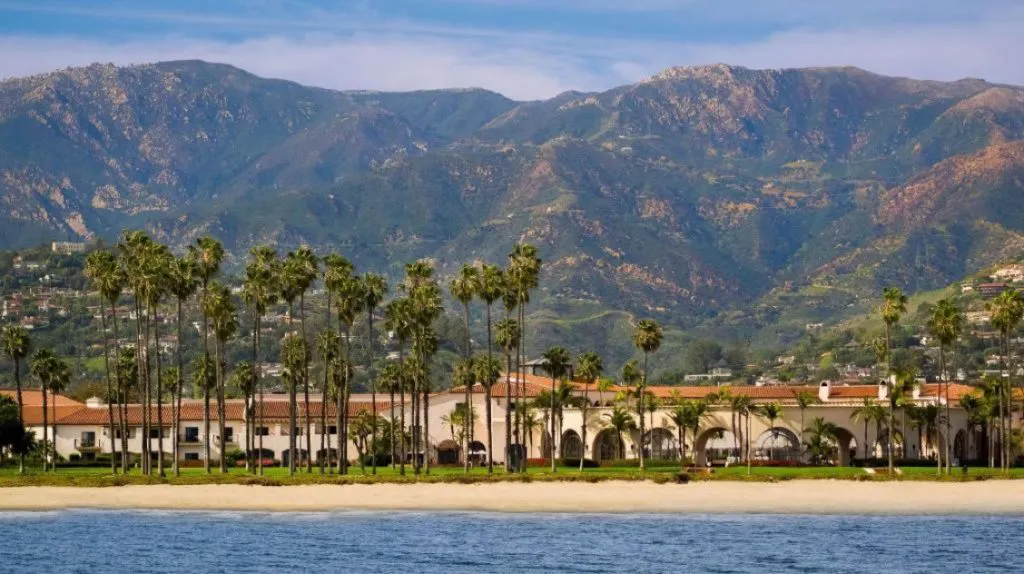
Equipment / Manufacturing
Innovative Micro Technology creates a safety-focused culture
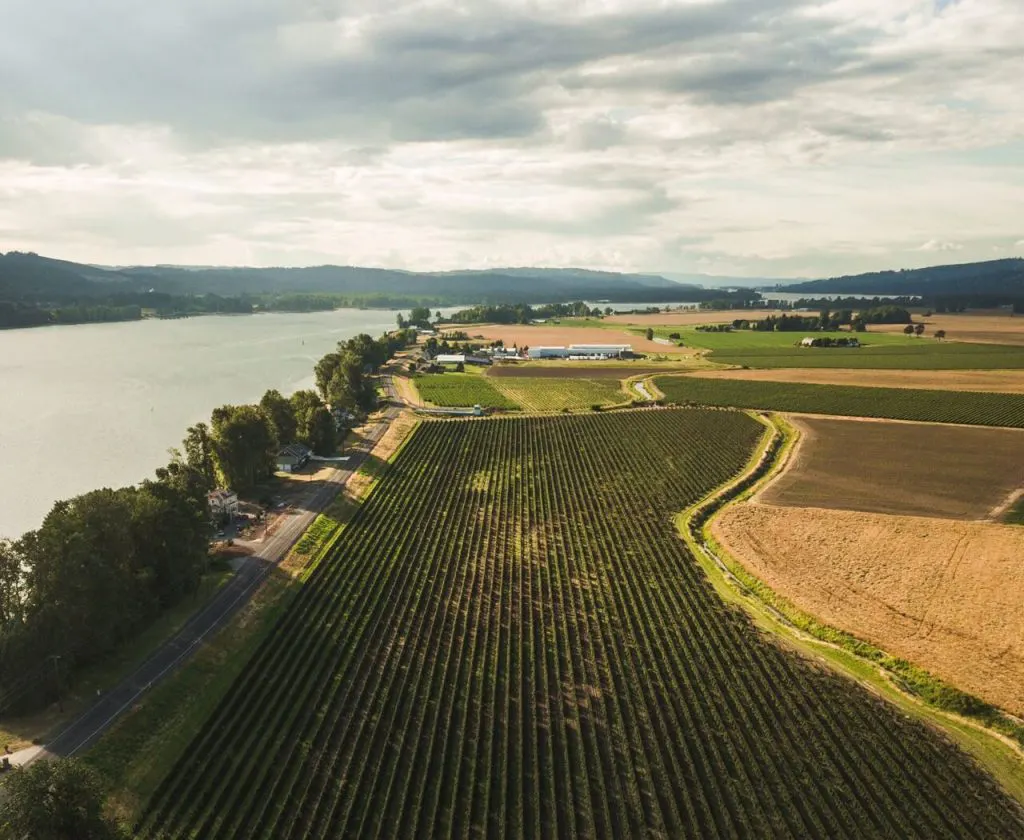
Equipment / Manufacturing
Columbia Fruit saves money with organized inventory
4,000+ COMPANIES RELY ON ASSET OPERATIONS MANAGEMENT
Leading the Way to a Better Future for Maintenance and Reliability
Your asset and equipment data doesn't belong in a silo. UpKeep makes it simple to see where everything stands, all in one place. That means less guesswork and more time to focus on what matters.
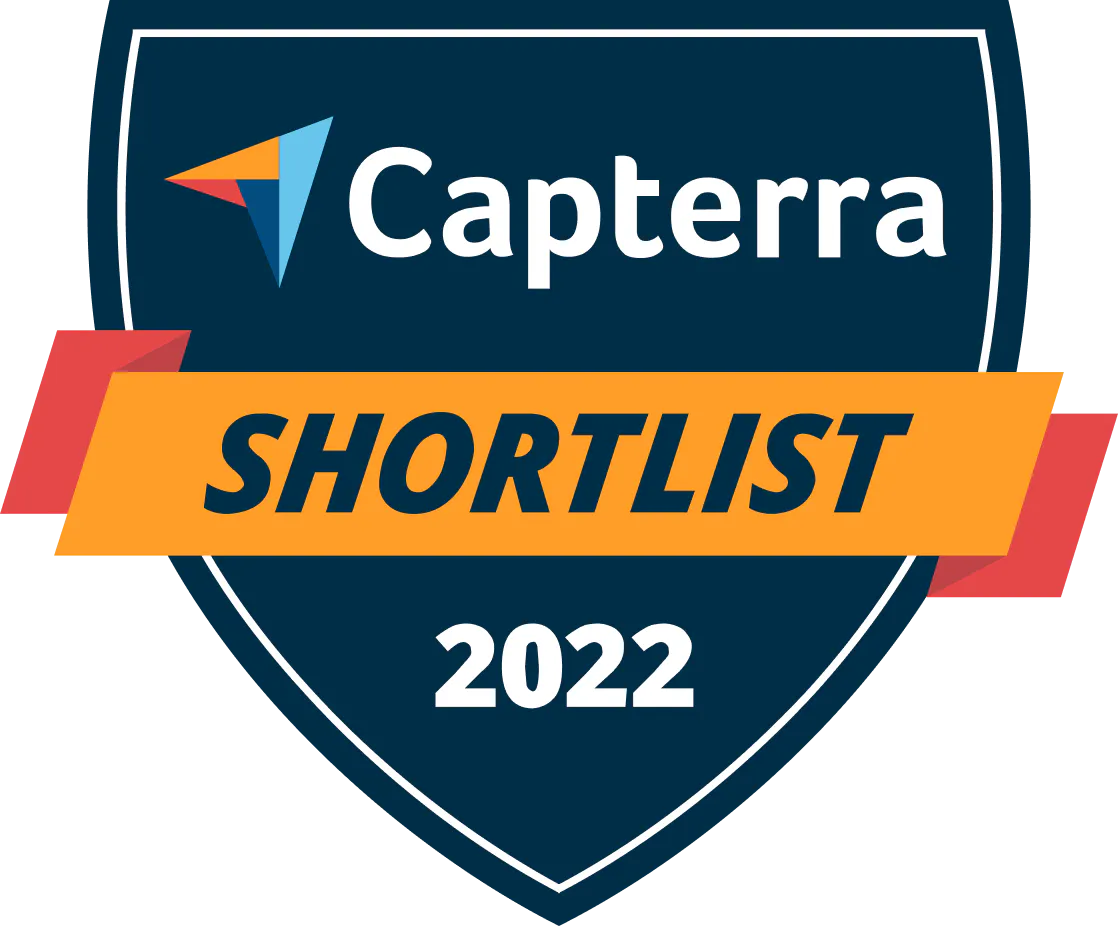

![[Review Badge] GetApp CMMS 2022 (Dark)](https://www.datocms-assets.com/38028/1673900459-get-app-logo-dark.png?auto=compress&fm=webp&w=347)
![[Review Badge] Gartner Peer Insights (Dark)](https://www.datocms-assets.com/38028/1673900494-gartner-logo-dark.png?auto=compress&fm=webp&w=336)
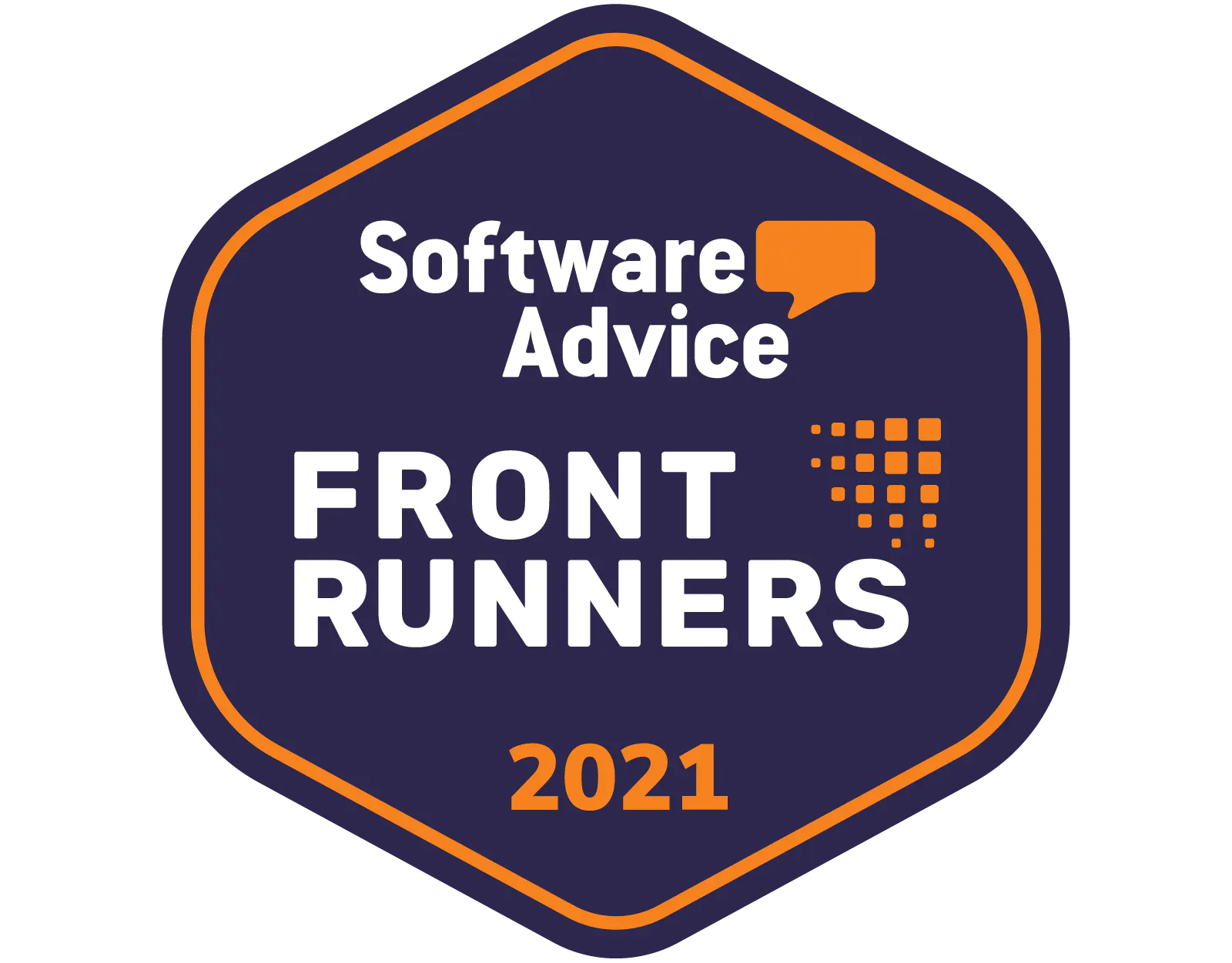